Hacking Curiosity: Adding an aftermarket sample collection capability to the Mars Science Lab
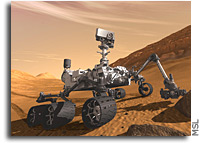
By: Doug Mohney – Satellite.tmcnet.com — NASA’s withdrawal from a joint ExoMars 2016/2018 mission has left the planetary science community grieving the at loss of the first step in a sample return mission: collection of samples. However, there’s a $2.5 billion rover with a mechanical arm and plenty of power scheduled to land on Mars in August. (1) Can the Mars Science Lab (MSL) Curiosity be fitted with a couple of “aftermarket” sample collection racks once it completes its primary mission of one Martian year? The author believes there is the potential to do so.
Capabilities of Curiosity
Assuming a successful landing at Gale Crater in August (1), Curiosity is expected to have enough power for at least fourteen years of operation, according to the MSL website. Given the operational records of the solar-powered Mars Exploration Rovers Spirit and Opportunity, as well as the Viking landers, it is not unreasonable to believe Curiosity will be available far beyond its expected initial mission of 687 Earth days.
As a part of its Sample Acquisition, Processing, and Handling (S/SPaH) system, Curiosity has a robotic arm capable of scooping up soil and small rocks, dropping soil into a pair of inlet tubes on the top deck of the rover. The arm also has ability to rotate/swap between three drill bits.
Exact details on the mechanical capabilities and limitations of the arm — specifically the range of motion relative to how far it can “reach” on the top deck and the maximum amount of weight/mass it might be able to lift — do not appear to be available on the Internet, so some parts of this discussion fall into the arena of educated guess.
Adding a rack (or racks) as aftermarket equipment
Presumably the easiest way to load a sample rack on Curiosity would be to use the rover’s mechanical arm to grab it from a container or simply a flat surface at a delivery point on the Martian surface, swing it into position, and then release it where it needs to go. While the arm doesn’t have “fingers,” it does have a mechanism and process designed to swap drill bits. A rack to be put on the top deck or hung off another point of the rover would have a fixture identical to the back of a drill bit. Loading a rack would be a matter of commanding/programming/reprogramming the arm to reach out and grab the figure on a rack, moving the rack to where it would go, then releasing and securing it.
The sample rack would be made of a lightweight material, such as titanium or carbon fiber. One potential concept would be a square or rectangle shaped rack with 3 (square) or 5 (rectangle) sample containers designed to sit on the rover equipment deck, with the remaining space reserved for a simple mechanism to fasten/secure the rack to the rover using an existing structure.
Each sample compartment would be a simple mechanical container, with a spring-loaded lid able to be opened and closed with a toggle or other low-force push. Before loading a sample, the arm would open the compartment, reach down to scoop up the target sample, drop it into the compartment, and then toggle it closed.
Compartments would be designed to hold small rocks and soil, but not be pressure tight. The design objective would be to hold most — if not all — of a soil sample in the compartment during travel, and for the lids to be tight enough to prevent soil samples from freely mixing together in case of a bumpy ride during the rover’s travels or if soil accidentally spills on top of a closed bin when loading an adjacent open compartment. Lids should also be strong enough to hold individual samples in place if the rack is inadvertently tipped or dropped when it is being unloaded from the rover and into a return vehicle.
Electronics and fancy mechanical structures should be avoided at all costs. Weight is the key factor and one hopes/assumes that an empty add-on sample rack would mass less than half a kilogram — preferably less. A very small amount of dust/soil loss during transport would be acceptable since a tight seal is likely to add complexity, weight, and expense.
There may be more than one place to add sample racks on Curiosity, but the total number of racks would have to be weighed against the operational complexity of putting more than one rack onto the rover and any sort of functional degradation which might be caused by adding too much weight to the rover.
Rack development and load testing
Several different sample rack configurations could be built and rack loading procedures tested using MSL support equipment here on earth. Other procedures to be tested would include loading of soil samples into individual compartments and the ability for the arm to unfasten the securing mechanism(s) of the rack, grasp the grapple point on the rack, and lift a fully loaded rack off the deck, keeping it level, and deliver it into an open slot on a notational sample return vehicle.
Delivering aftermarket hardware
Assuming there are no technical show stoppers in the ability of MSL’s arm to perform the described task, delivering a sample rack or racks should be a challenging but straightforward. Among all the delivery challenges, the biggest would appear to be to accurately deliver a low mass payload to within a kilometer or less of Curiosity’s anticipated travel path, preferably ahead of the rover so a major detour is not required.
The first feasible launch window to deliver hardware is 2016. While the author would prefer a launch attempt in 2014, it is highly unlikely NASA could embark upon and implement this project in two years from decision to launch.
With no electronics, a sample collection rack of carbon fiber or titanium should be sturdy enough to handle launch and Mars entry G-forces without sustaining physical damage or deformation. If not, a low-tech, low-cost packing to provide cushioning shouldn’t be a big problem.
Speaking of weight, since a rack is expected to weigh under a kilogram, a delivery system for a rack should be relatively simple and presents the opportunity for other lightweight instrumentation and experiments to be bundled in. The author is no rocket scientist, but assumes that a light to medium-class launch vehicle would be more than sufficient to put several racks in the neighborhood of Curiosity.
One configuration for an entry “vehicle” could consist of a hypersonic aerodynamic decelerator (HIAD), an off-the-shelf precision airdrop system modified for Mars use, and a Pathfinder airbag style lander configuration — or lighter. The entry vehicle provides the opportunity for real-world testing of a HIAD in Martian atmosphere.
GPS-based precision airdrop systems have been used in high-altitude environments for about a decade, with a CEP delivery of 100 meters or less. Mars use will require modifications including a larger parafoil and a guidance system to utilize RF transmissions emitted by the rover as a homing beacon.
Since accuracy with a low-cost delivery system is likely to be less than optimal, one option for hardware delivery might be to have several smaller entry vehicles to provide better odds for at least one sample rack to be close enough for pickup. Using multiple entry vehicles provides opportunities to experiment with different HIAD designs, flying/delivering CubeSat-style/sized experiments to Mars, and the ability to observe/characterize the Martian atmosphere from multiple data points in a specific time period.
Upon landing and a smooth stop, the entry vehicle should open up and have the rack sitting out in the open on a flat and relatively smooth surface for pickup. A small electronics package could transmit a couple of photos of the area to help in defining location and confirming successful delivery and availability of the rack.
Sample return operations
Detailed mechanisms for sample return go beyond the scope of this article. If sample collection is successful in 2016-2018, a sample return mission could be conducted in 2018 or 2020.
Mechanically, sample return would require Curiosity to drive up to the return vehicle, remove a fresh empty sample tray, then remove the filled sample tray from its top deck and insert it into the now-waiting slot of the return vehicle. If the filled tray cannot be moved from Curiosity due to mechanical difficulties, samples could be moved either in part or in whole, one by one, to the empty tray and then loaded back into the sample return vehicle. Otherwise, the empty tray goes onto the back of Curiosity for another round of sample collecting.
Curiosity drives off to a safe distance while the sample return vehicle starts fuelling and then turns to document the launch of the vehicle into Martian orbit.
The sample return vehicle would hopefully/presumable be fueled using in situ resources, providing an opportunity to test and verify technologies applicable to both robotic and manned operations.
A second sample return vehicle would be delivered by a solar electric tug in the 2020-2022 timeframe — another advanced technology requiring demonstration and verification for Mars operation –at the next window. The solar electric tug would pick up the first in-orbit sample container and wait in orbit to get the second one before starting its return to earth.
Readers should note the author believes capabilities for sample return should be build to demonstrate and validate technologies for future manned operations. In addition, capabilities discussed above (in situ fuel generation, solar electric tug) should be useable and available as a part of a broader infrastructure for future robotic and manned exploration of Mars, rather than stand-alone “one and done” missions.
Economics and other advantages
Adding additional capability to Curiosity shouldn’t sound like a radical concept. Hubble has had its capabilities overhauled on a man-tended basis many times over the years. Providing Curiosity with a simple sample collection capability, if within the rover’s technical capabilities, gets planetary researchers one step closer to a sample return mission while allowing NASA to fully leverage the capabilities and multi-billion dollar investment it has made in MSL.
In addition, delivery of the low-mass sample rack hardware provides a quick and affordable opportunity for demonstrating the ability to perform Mars CubeSat missions and to test one or more HIAD concepts in real world conditions.
Mars Pathfinder cost under $300 million to demonstrate a wide range of technologies. Delivering a simple piece of hardware should cost less, even when you add in a couple of CubeSats along for the ride and assuming a SpaceX Falcon 9 would be the vehicle of choice to launch the mission.
# # #
(1) If Curiosity crashes and burns in August, please disregard this proposal.