Roaring Comeback
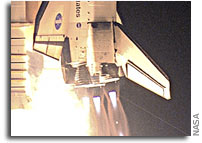
Space Shuttle Main Engine and solid rocket testing doubled to buttress launch safety
This article appears in the 11 July 2005 issue of Aviation Week & Space Technology
Reprinted with permission of Aviation Week & Space Technology – www.aviationnow.com
The orbiter Discovery’s 8-min. 30-sec., zero-to-Mach 25 launch to orbit will be propelled by Space Shuttle Main Engines and Solid Rocket Boosters that have undergone substantially increased testing and rigorous quality oversight in the two years since the Columbia accident.
Any serious propulsion emergency on the 4.5-million-lb. vehicle, climbing initially on 7.4 million lb. thrust, could be a life-or-death issue for the seven-memberSTS-114 crew.
The liftoff here is scheduled for 3:50:47 p.m. EDT July 13 and will move about 25 min. earlier each day in the event of a launch slip.
In preparation for the return-to-flight, testing has been doubled for the SSME and SRB programs during the last year, even though neither system was involved in the Columbia accident. The added testing has reversed a situation in which major cutbacks in SSME firings at the Stennis Space Center, Miss., were being considered by NASA Headquarters before the Columbia accident. Both NASA field center and contractor engineers were becoming concerned about this engine-test cutback, managers told Aviation Week & Space Technology.
Following Columbia Accident investigation Board (CAIB) recommendations, more independent oversight of the SSME program has also been introduced, and this has sometimes been “painful” for the project’s established engineers.
“This is to make sure we are not missing the forest for the trees,” says SSME Rocketdyne project manager Jim Paulsen. One change will be more formalized assessment and disposition of minority engineering opinions on test data. Manned launches will always have risk, but the added SSME and SRB testing has increased the safety odds for the STS-114 launch and subsequent missions, say astronauts and managers. One SSME to be used on Discovery is flying its first mission, while another is flying its third and the other its fifth launch.
Shuttle external tank debris and orbiter repair issues have dominated the more visible NASA post-Columbia environment since they directly involve Columbia accident factors. But no amount of post-launch inspection, Mission Management Team action or in-orbit repair can aid astronauts if they face a serious SRB or SSME problem as the vehicle accelerates to 17,500 mph. en route to orbit. Propulsion safety requires rigorous pre-launch testing and quality control, which earlier found a manufacturing flaw in Honeywell electronic capacitors for the critical SSME engine controller (AW&ST June 27, p. 22).
The major contractors for the three reusable 500,000-lb.-thrust SSMEs are Boeing-Rocketdyne, Pratt & Whitney and Honeywell. Rocketdyne is the prime SSME contractor, but Pratt is in the process of acquiring Rocketdyne. The main contractors for the shuttle’s twin reusable SRBs are ATK Thiokol and United Space Alliance, while ATK Thiokol is specifically responsible for the 3.3-million-lb.-thrust Reusable Solid Rocket Motor (RSRM), which is the core of the booster (see p. 60). NASA Marshall Space Flight Center in Huntsville, Ala., oversees both projects.
NASA/Rocketdyne facilities at Kennedy now handle the assembly of all SSMEs—work that, before Columbia, was largely based at Rocketdyne’s Canoga Park, Calif., facilities. Moving it to Kennedy has saved costs and enabled more focused expertise. The engine work at Kennedy for return-to-flight has involved a Herculean effort to build, ship to Stennis for test, then return back to Kennedy nine flight SSMEs. Three have been installed in Discovery and three in Atlantis, while three others are ready backups to use in Atlantis. These backups would be used should Atlantis require an immediate SSME changeout after any potential Atlantis pad abort for an emergency Discovery crew rescue mission.
“Post-Columbia we sat down very earnestly here at Rocketdyne not only as a program—but also as a company— to rethink how we look at flight safety,” says Paulsen. The SSMEs, unlike the solid boosters, involve extremely complex turbomachinery with thousands of parts, some rotating at nearly 40,000 rpm. And unlike the more massive SRBs, the liquid engines can be tested more frequently.
“When you look at both Columbia and Challenger, the two failure scenarios were directly in front of us, yet we had a hard time seeing them,” he adds. Both the Challenger and Columbia accidents very much affected us emotionally . . . and we have strengthened some things that we think are very important,” notes Paulsen. That is also the case at Pratt & Whitney, which builds the SSME’s 33,932rpm. high-pressure hydrogen turbopump and 22,380-rpm. high-pressure oxygen turbopump. These are two of the more critical and complex elements in the entire space program.
Since the shuttle grounding, NASA SSME managers in Huntsville have been especially concerned that they not allow “process creep” to disarm flight safety, says Gene Goldman, engine project manager at Marshall. “This has been to assure ourselves that we are not getting into the ‘normalization of deviance’ that has been cited” as a key factor in the Columbia accident (AW&ST Apr. 28, 2003, p.29).
“As part of our return-to-flight investigations, we went back and looked at all of our previous design changes, all of our operation and maintenance requirements, all of our launch-commit criteria and our foreign-object-damage limits, both internal and external to the SSME,” says Goldman.
In addition, instead of cutting back on SSME static firings, the shuttle program has fully reactivated a second SSME test stand at Stennis. That extra stand is now enabling engineers to begin firing an SSME about once a week, with the goal of building toward 50 tests per year. “This has been a boon to the program,” he says.
The twin-stand operation is enabling not only standard testing of flight engines and components, but also trials that “explore the edge of the envelope” on internal engine parameters. This is something engineers had not been able to do for several years when using just one test stand at Stennis, says Mike Kynard, Marshall deputy SSME project manager. During engine development years ago, up to four test stands were used—two at Stennis and two at Rocketdyne’s Santa Susana facility near Chatsworth, Calif.
Maintaining a steady pace of ground firings is vitally important to flight safety “because each individual SSME is so complex, analytical models are not going to accurately convey what type of phenomenon that you might have,” says Goldman.
Project engineers have always done pre-firing reviews about what to expect from a given test, based on previous static test and flight history. Results are then always scrutinized to determine not only what occurred, but also if there are any subtle differences from the predicted. That, in turn, can lead to a follow-up review seeking to learn why differences occurred, even though they were not anomalous.
All of this then becomes part of the program’s “approved knowledge,” information certified as meaningful—not necessarily good or bad—but a history of hardware characteristics, says Goldman.
“We just had our anniversary of 1 million sec. of testing on SSME [since June 1975], which is something we are very proud of, but also something we leverage-off of 100% for quality control,” says Paulsen.
“But we were under a lot of pressure to get the number of tests down. And we would have fought that very rigorously at both Rocketdyne and Marshall,” he says. “There were some initiatives to get it down to 15-20 tests per year,” but the second Stennis stand has reversed that trend.
While building to a higher rate, the program has had about 50 tests totaling 24,000 sec. of firing time since the Columbia accident. Most of the runs are for the SSME 520 sec. flight duration and include the throttling sequences. Goldman says runs since the shuttle was grounded involve:
- About 44 broad-based tests. These include acceptance tests for all nine flight engines before their shipment back to Kennedy. They also include runs to increase the proven reliability of key individual components such as the relatively new Pratt high pressure hydrogen turbopump that runs with a 1,110F discharge flow.
Such runs should ultimately verify a fuel turbopump’s ability to be “green run” acceptance-tested after any major internal teardown, then usable on a flight engine for up to 11 starts on the launch pad.
- About six runs for “corner-of-the-box” testing. The propellant temperature and pressure conditions in the engine must be maintained within a few degrees for a normal ignition.
These tests are exploring what happens in the engine if those parameters are varied slightly, as could happen on the launch pad. Although CAIB members have specifically praised the SSME program for its rigorous test plan, more corner of-the-box testing is a direct response to CAIB views.
- Future developments. There will be increased tests on SSME Advanced Health Management System capability to safely shut down an engine if the AHMS sensors detect vibrations that could signal an imminent catastrophic failure. The system is slated to fly starting in late 2006.
With just one test stand, Goldman says managers were pretty much limited to a “fleet leader extension program” to build test time on individual components. The SSME program never flies any hardware that exceeds one half of the test time on the fleet leader for any major component such as pumps and key valves. Two stands now allow that philosophy to be maintained and, in parallel, the exploration of other engine characteristics off line of the basic testing.
Independent reviews by outside rocket propulsion experts with no ties to the shuttle schedule are also more frequent. “We actually did seven independent reviews, covering various aspects of the SSME” over the last two years,” says Paulsen. “It was a little bit painful for the SSME engineers to do that. But the bottom line is, we found it very valuable and the engineers then found it was very rewarding,” he adds. These have often been done in connection with Marshall.
The Huntsville center itself has brought in more of its own “old head” experienced propulsion engineers for independent SSME reviews there, notes Goldman. And Ron Tepool, Marshall’s highly experienced SSME chief engineer, routinely holds his own oversight sessions as well.