NASA’s New CEV Launcher to Maximize Use of Space Shuttle Components
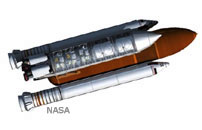
The decision on what new launch vehicles NASA plans to use in the coming decades is rapidly coming into focus. In some ways these launchers will be new – yet they will also look very familiar using hardware and concepts that have long and well-established flight histories.
Analysts have reviewed a wide variety of launch vehicle options for both manned and cargo-only versions of the NASA Crew Exploration Vehicle (CEV) and have settled for an all-solid booster configuration, according to sources close to NASA’s Exploration Systems Architecture Study (aka the “60 Day Study”)
But a year-long study initiated prior to the change in NASA Administrators and completed this spring gave an extensive review to both uses of a launch vehicle derived from the Space Shuttle’s Solid Rocket Booster (SRB) as well as a larger booster design using twin SRB motors flanking a derivative of the shuttle’s External Tank (ET), mated with a large liquid upper stage. Studies also looked at growth options from the nation’s Evolved Expendable Launch Vehicles (EELV) community.
Internal NASA documents detailing the review, which was completed in late June, were obtained by the authors. A second, related study has reviewed heavy lift options using the same shuttle-derived elements.
Analysis of Alternatives
Throughout most of 2004 and into the spring of 2005, the Exploration Systems Mission Directorate (ESMD) conducted a detailed series of trade analyses of launch vehicle options for both manned CEV spacecraft and cargo requirements. Booster lift capabilities studied ranged from as small as seven metric tons to in excess of 70 metric tons. (1 metric ton = 1,000 kg or 2,200 pounds). Very large heavy lift launch vehicle designs were also reviewed as part of a series of trade studies led by Johnson Space Center in Houston. These vehicles would be capable of in excess of 100 metric tons of lift to low orbit. The two series of reviews were separate but complimented each other in their wide-ranging assessments of launching options.
In addition, an assessment of heavy lift designs derived from today’s current Atlas V and Delta IV EELV was conducted. An integrated launch systems study was also conducted by ESMD. ESMD looked at 12 crew launch vehicle (CEV) options, 35 cargo launch designs, and three classes of new upper stage configurations. This evaluation looked at common elements shared between the upper stages of the CEV manned boosters and those upper stages that might be used in cargo lifters. A desired element was synergy between the CEV manned booster and its heavy lift family. NASA also evaluated the changes in or construction of new ground installations that would be needed to support the CEV launcher choices.
Families of Launch Vehicles-CEV/ET-derived Options
Fairly early in the analysis, planners determined that a new hybrid booster had no particular benefit over a launcher developed from either EELV or shuttle-derived designs. They also determined that cost effectiveness could be achieved if the launch vehicles chosen for CEV systems could yield a higher flight rate by multiple government users, such as the national security community.
Shuttle-derived launch designs were evaluated for both crew and cargo carriers. Designs for the Earth Departure Stage (EDS), which, under the lunar exploration scenario initially proposed by Project Constellation, would inject the docked CEV and lunar lander into lunar orbit, were evaluated from possible common use of engines and tankage used in the shuttle-derived launchers. This emphasis on shared component commonality was a continuous theme in the launch vehicle trades throughout the year.
For manned CEV flights, the series of in-line booster configurations included four and five segment SRBs derived from the existing space shuttle configuration; a series of shuttle External Tank-derived “in-line” launchers, and a pair of large heavy lift shuttle-derived manned in-line vehicles.
Multiple architectures were studied against possible multiple mission launcher options. Planners defined “affordability” as being characterized by reduced non-recurring costs, reduced recurring costs, or cost phasing-in. Risk assessments included evaluating risk from technology development, launch processing risks, and schedule risk. Moreover, any heavy lift choice must be scalable for manned and cargo deep space (Mars) use, possible national security payloads of the future, or possible adaptation for commercial variants during the lifetime of the vehicle’s operation.
According to planners involved in the 60 Day Study, a crew safety goal of one launch failure in 1,000 was the objective for the launch vehicle selected. This requirement is ten times greater than the 1/100 risk posed by the existing post-Columbia space shuttle orbiter fleet. Planners also observed that the larger number of in-space events needed to accomplish CEV missions, such as earth orbit rendezvous and docking of multiple vehicle components, the greater the risk to the astronaut crews.
Lastly, planners were directed that whatever series of launchers selected must comply with the January 2005 U.S. Space Transportation Policy. Johnson Space Center continued to study manned and cargo vehicle designs until late June of 2005. The ESMD analysis of alternatives I and II were folded into the exploration architecture study ordered by the new NASA Administrator Mike Griffin.
Shuttle-Derived Crew Transport
According to sources familiar with the launcher section of the so-called 60 Day Study, the future U.S. manned and heavy lift launch vehicle architecture will be based on two configurations of shuttle-derived vehicles. Both vehicles will launch from Kennedy Space Center. Existing launch pads and associated facilities will undergo extensive modifications and upgrading to accommodate the new designs, according to a semi-final version of the study.
Cargo vehicle studies using Space Shuttle ET and SRB hardware focused on two major variants: so-called “side-mounted” and “in-line”. Side-mount designs hang cargo and/or crew off the side of a large external fuel tank as is currently done with the space shuttle. In-line designs place the cargo (or crew) directly atop a lower first stage as did Saturn launch vehicles.
Budget pressures have intensified due to the grounding of the shuttle fleet after last week’s foam and debris shedding. This grounding and a possible hiatus before flights resume could lead to increased pressure to develop a side-mounted shuttle-derived heavy lifter similar in overall concept to the Shuttle-C launch vehicle proposed in the 1990s.
This side-mounted launcher would allow many existing shuttle facilities to be used either unmodified or with slight modification since the shuttle orbiter would be replaced with a cargo carrier and use the same ‘footprint’ as does the current space shuttle. The costs required to transition to such a new system would be less, and current cargoes (ISS components) could be integrated in a fashion nearly identical with how they are launched in shuttle orbiter cargo bays. The larger, more capable in-line shuttle-derived systems that have been studied would require substantial modifications to launch pads and ground support infrastructure.
This option may become a more attractive option for another reason. As reported several weeks ago (See: NASA Studying Unmanned Solution to Complete Space Station as Return to Flight Costs Grow ) , the White House has been directing NASA to limit shuttle flights wherever possible. This will inevitably result in a truncation and decrease in capability of the ISS. Concern is mounting among the other participating nations in the ISS program about what sort of space station they will get after all these years of waiting.
Click on image to enlarge
One thing Mike Griffin has been considering is halting the ISS assembly sequence (using shuttle orbiters) at one point, and then resuming it some years later by using a shuttle-derived launch system to ferry up the remaining components. Using a side-mounted configuration offers the least amount of new development of any option. This also places the development of this new launcher in the critical path of ISS assembly. In the 1990’s Russian hardware development was in the critical path for space station construction – and problems with that hardware (fiscal) caused considerable delays in building the station.
According to documents obtained by the authors, the original ESMD Mars mission plan, then called Spiral 4, would have involved a human fly-by of Mars around 2032. Spiral 5 was would have followed with human landings on Mars beginning in 2034. Planning documents also suggested that the original Project Prometheus nuclear electric propulsion system, needed for human and cargo flights to Mars, would be launched to Earth orbit by the in-line shuttle-derived launch vehicle variant.
Since the arrival of Mike Griffin and the departure of Craig Steidle, all detailed human Mars mission planning has been de-emphasized. According to NASA sources, this is due, in great part, to looming budget constraints facing the Griffin administration. Sources suggested that the main elements of the architecture review now focus on ISS assembly, CEV design and development, and human lunar exploration. Planners hope to ‘scar’ the architecture that will be set in place following the study so as to evolve to support future human Mars missions. This scaring includes what has been described as a ‘design evolution path’ towards a Mars CEV – one that evolves from the lunar CEV.
As of this writing, sources familiar with the various study options suggest that the earth orbital CEV, one designed to provide ISS crew transport, may not have full ‘traceability’ to the lunar variant. This situation might come into play if the earth orbital CEV is developed by another contracting process – an entrepreneurial approach which was been hinted at by Griffin and his staff. Sources suggest that while a CEV would be developed from a NASA RFP with a winning prime contractor – either a team led by Lockheed Martin or Northrop Grumman, such a CEV would be mandated for earth orbit capability – but not as an operational necessity. In other words, the RFP-derived CEV would be able to make piloted and automated flights into a low earth orbit, but its prime requirement would be human lunar orbital missions.
Such an entrepreneurial-derived CEV would have as its focus piloted and robotic cargo capability to the ISS and to make rendezvous with a Project Constellation fleet being assembled in an L-1 high earth orbit as well. Such details remained to be finalized as this article went to press in early August.
A Safer Escape
Two major requirements drove the CEV booster choice. First, NASA analysts placed a requirement on the CEV launch vehicle that mandated a full launch escape envelope for the crew. Appearing on NBC’s “Meet The Press” on 31 July 2005, Mike Griffin made it clear that he did not ever want to see another U.S. human launch system where things (foam and debris) could “fall back on the crew”.
To simplify escape options, planners have focused on a solid fuel tractor rocket mounted on a tower on top of the CEV. This design was heavily influenced by the Apollo Command Module Launch Escape System (LES) used from 1964 to 1975 on manned and unmanned Apollo Saturn boosters. The escape system would be jettisoned during a normal CEV ascent. Secondly, the overall launch vehicle design was to be substantially safer and simpler to maintain than the existing space shuttle orbiter, which ascends to orbit using a trio of liquid fueled engines firing on the orbiter along with the solid motors.
Safety issues associated with manned shuttle launch primarily revolve around both limited (or nonexistent) crew escape options and more limited engine-out architectures. Planners were made aware that the shuttle’s limited crew escape options were based on a mature operational safety level – one planned for, but one that was not ultimately achieved. Original shuttle crew escape was predicated on what was then termed “intact abort” meaning for the crew to survive a launch failure the entire orbiter had to return, intact, to a hard-surface runway. Orbiter ditching in the water was always considered problematical from a crew survival standpoint.
Following the 1986 Challenger accident, a capability for crew bailout from the orbiter in controlled gliding flight was added. However, few launch or landing malfunctions were considered likely that would leave a crippled orbiter under such full control. Many in the human spaceflight community felt that the bailout option was more of a palliative than an effective means of crew escape. Grafting a crew escape module on the existing orbiter airframe was considered too expensive, time consuming, and impractical.
Planners designing the CEV launch system hoped to avoid most of the shuttle’s safety issues by a simplified vehicle architecture that uses many of the same shuttle booster components but uses them in a different more robust launcher architecture. For the CEV crew to escape a launch abort, only the part of the CEV containing the flight crew would be explosively detached from the remainder of the CEV/launcher. This approximates, by comparison, the Apollo launch escape philosophy wherein the Command Module was separated from the remaining Service Module part of the Apollo spacecraft.
Current designs call for a large conical or biconic space capsule as a design reference for the CEV. Planners used a maximum 18-ft diameter width of the base of the CEV reentry vehicle as a size option. Planners have looked at a two-tier CEV general arrangement, sources told the authors, with crew accommodations for three, four and ultimately six astronauts. The bottom tier of the CEV capsule contained work stations, a galley, and crew waste disposal systems as well as lockers similar to those on the shuttle orbiter mid-deck.
The upper tier contained the crew couches and flight navigation and control displays. Gross liftoff weight of CEV designs studies this spring ranged from 20 to 30 metric tons, which included the CEV return capsule, a small supply unit at its base, and a propulsion system capable of performing a deep space abort if the Earth Departure Stage malfunctions. The CEV propulsion system also is the primary means astronauts would use to leave lunar orbit for the trans-earth return.
Storable fuels were the prime candidates for the CEV propulsion system. The configuration used differed in size for the different CEV missions. None of the CEV candidates under early evaluation by ESMD or JSC, reviews totally independent from the contractor RFP process, were capable of human interplanetary flight to the asteroid belt or Mars. Instead, human lunar missions were the focus of these CEV capabilities.
CEV Launch Options
One launch vehicle that was evaluated for lifting the CEV into Earth orbit was based on a modified Space Shuttle ET. Profiles were evaluated using one of two sets of engines on the tank; the Space Shuttle Main Engine (SSME) and the Rocketdyne RS-68 developed for the Delta IV EELV launcher. The study looked at two structural versions of the shuttle-derived ET. In both cases, use of any ET for a manned CEV requires extensive modifications of the current design. One approach that was evaluated would use a basic ET but with the liquid oxygen tank modified into a cylindrical shape with a new forward skirt added and a payload adapter. Under this design, planners proposed only partially filling the ET prior to flight to reduce the number of main engines used to two SSMEs.
A second ET design looked at by planners was referred to as a “Short Tank” ET. This variant was modified by removal of two 20-ft sections of the liquid hydrogen tank, SRB thrust ring attachments, and other related systems. This review looked at mounting RS-68 engines to the tank’s base.
For upper stages, two options were reviewed. One used a single SSME modified for air-start, the second studied use of a single J2S engine derived from the Apollo Saturn IB and V heritage launcher upper stages (Saturn IB second and Saturn V second and third stages). The SSMEs were assumed to operate at 104% thrust levels. The launch site was Kennedy Space Center; performance evaluation was assuming a 1976 atmosphere model with no winds at liftoff. Eight different configuration designs were looked at, which determined that the J2S yielded the smallest payload performance; which was 68,000 pounds. The RS-68 produced the largest; in excess of 70,000 pounds (this includes the weight of the stage plus the CEV stack).
SRB-derived Booster
Two series of boosters were evaluated derived from the Space Shuttle SRBs. Assumptions made included full recovery of the booster, use of a new retrorocket system, and a new liquid upper stage that would be large enough to inject the CEV into orbit and be restarted multiple times for approach to a lunar fleet, or to approach and depart from the ISS. Both four and five segment motors were studied.
Three upper stage candidates were evaluated. One using the SSME, one using the J2S, and one using the Russian AJ26-60 version of the N-1 launch vehicle’s NK-43 upper stage engine. All variants of an SRB booster could lift a 20 metric ton CEV package. But a five-segment motor would be required to launch a larger 30 metric ton. CEV design. Increasing the reference thrust of the SSME to 109% was also studied for the SRB CEV launcher’s upper stage. Both SRB designs require extensive launch pad and launch logistics modifications at Kennedy Space Center. For planning, stacking of the motors inside the VAB was assumed, which would require construction of new work platforms there. At the pad, a new mobile launch platform that would be shared with the shuttle-derived heavy lifter was also assumed.
Among the shortcomings of any SRB-derived launcher was lack of engine out capability. For all of the shuttle-derived manned launcher designs, SSME modifications were needed, the J2S would require technology improvements for updating, and the Russian engines would require new arrangements. One planner said that a 2-engine J2S would improve performance although it would add weight.
Side-Mount ET to the Moon
In the end, the two ET-derivatives; a side-mount vs. a stacked in-line produced better safety margins for the CEV aboard the in-line mold line. A side-mount ET manned launcher required development of the exploration carrier to produce a 6.5 x 25m payload envelope beneath the CEV. The cargo version replaced the CEV with a nose fairing. For manned flight, use of a derivative of the space shuttle orbiter OMS pods was studied, as was an entirely new on-orbit propulsion system using different propellants.
A lunar side mount manned launcher would use the five-segment motor, new OMS pods, and a liquid hydrogen upper stage. Both a side-mount and in-line ET manned CEV launcher could accommodate 20 and 30 metric ton CEV designs. A side-mount design had the lowest infrastructure change requirement for launch logistics. An in-line required the most modifications. An SRB motor derivative fell in the middle of these change-out costs. As time progressed, its long flight history seemed to outweigh its lack of engine-out ascent options, and its simplicity of use appeared to sway planners to its selection. For the ET derivatives, a heavy lift cargo-only design seemed the most promising, side-mount or in-line.
Next: How those trades were conducted.