NASA Encounters Possible Problems With Crew Launch Vehicle Design
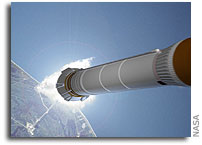
According to industry sources, NASA has encountered some problems with its planned CLV (Crew Launch Vehicle) design as spelled out in the yet to be (formally) released Exploration Systems Architecture Study (ESAS) Final Report.
Sources report problems have been encountered in designing an expendable version (RS–25) of the current SSME (Space Shuttle Main Engine) for the CLV’s second stage that can be air-started. Concerns have also been raised that a possible alternate second stage engine, a derivative of the Apollo era J-2S engine, may be underpowered for the task.
These sources also talk about interest on NASA’s part of moving to using a 5 segment SRB (Solid Rocket Booster) as the first stage of the CLV instead of the initial plan to use the current 4 segment booster used by the Space Shuttle. In so doing, NASA would now be creating what would, in essence, be a wholly new launch vehicle.
NASA has considered bringing in contractor representatives soon to discuss this issue since a change in the CLV design would lead to other delays – including the CEV.
Background Material
NASA ESAS Final Report November 2005: Section 6.0 Launch Vehicles and Earth Departure Stages
Excerpts
6.4.2 LV Trades Overview 6.4.2.1 Crew Launch Vehicle
CLV options derived from Shuttle elements focused on the configurations that used an RSRB, either as a four-segment version nearly identical to the RSRB flown today or a higher-performance five-segment version of the RSRB using HTPB as the solid fuel. New core vehicles with ET-derived first stages (without Solid Rocket Boosters (SRBs)) similar to the new core options for EELV were briefly considered, but were judged to have the same limitations and risks and, therefore, were not pursued. To meet the CEV lift requirement, the team initially focused on five-segment RSRB-based solutions. Three classes of upper stage engine were assessed—SSME, a single J–2S+, and a four-engine cluster of a new expander cycle engine in the 85,000-lbf vacuum thrust class. However, the five-segment development added significant near-term cost and risk and the J–2S+/expander engine could not meet the 2011 schedule target. Therefore, the team sought to develop options that could meet the lift requirement using a four-segment RSRB. To achieve this, a 500,000-lbf vacuum thrust class propulsion system is required. Two types of upper stage engine were assessed—a two-engine J–2S cluster and a single SSME. The J–2S option could not meet the 2011 target (whereas the SSME could) and had 6 percent less performance than the SSME-based option (LV 13.1). The SSME option offered the added advantages of an extensive and successful flight history and direct extensibility to the CaLV with no gap between the current Shuttle program and exploration launch. Past studies have shown that the SSME can be altitude-started, with an appropriate development and test program.
6.1.3.2 Recommendation 2
Initiate immediate development of a CLV utilizing a single four-segment RSRB first stage and a new upper stage using a single SSME. The reference configuration, designated LV 13.1 in this study, provides the payload capability to deliver a lunar CEV to low-inclination Earth orbits required by the exploration architectures and to deliver CEVs configured for crew and cargo transfer missions to the ISS. The existence and extensive operational history of human-rated Shuttle-derived elements reduce safety risk and programmatic and technical risk to enable the most credible development path to meet the goal of providing crewed access to space by 2011. The series-burn configuration of LV 13.1 provides the crew with an unobstructed escape path from the vehicle using a Launch Abort System (LAS) in the event of a contingency event from launch through Earth-Orbit Insertion (EOI). Finally, if required a derivative cargo-only version of the CLV, designated in this report as LV 13.1S, can enable autonomous, reliable delivery of unpressurized cargo to ISS of the same payload class that the Shuttle presently provides.
6.1.3.4 Recommendation 4
To enable the 1.5-launch solution and potential vehicle growth paths as previously discussed, NASA should undertake development of an EDS based on the same tank diameter as the cargo vehicle core. The specific configuration should be a suitable variant of the EDS concepts designated in this study as EDS S2x, depending on the further definition of the CEV and Lunar Surface Access Module (LSAM). Using common manufacturing facilities with the Shuttle-derived CaLV core stage will enable lower costs. The recommended EDS thrust requirements will require development of the J–2S+, which is a derivative of the J–2 upper stage engine used in the Apollo/Saturn program, or another in-space high performance engine/cluster as future trades indicate. As with the Shuttle-derived elements, the design heritage of previously flight-proven hardware will be used to advantage with the J–2S+. The TLI capability of the EDS S2x is approximately 65 mT, when used in the 1.5-launch solution mode, and enables many of the CEV/LSAM concepts under consideration. In a single-launch mode, the S2B3 variant can deliver 54.6 mT to Trans-Lunar Injection (TLI), which slightly exceeds the TLI mass of Apollo 17, the last crewed mission to the Moon in 1972.
6.1.4 Recommended Launch System Architecture Description
6.1.4.1 Crew Launch Vehicle (LV 13.1)
The recommended CLV concept is derived from elements of the existing Space Shuttle system and is designated as ESAS LV 13.1. It is a two-stage, series-burn configuration with the CEV positioned on the nose of the vehicle, capped by an LAS that weighs 9,300 lbm (pounds of mass). The vehicle stands approximately 290 ft tall and weighs approximately 1.78M lbm at launch. LV 13.1 is capable of injecting a 24.5-mT payload into a 30- x 160-nmi orbit inclined 28.5 deg and injecting 22.9 mT into the same orbit inclined 51.6 deg.
Stage 1 is derived from the Reusable Solid Rocket Motor (RSRM) and is composed of four field-assembled segments, an aft skirt containing the Thrust Vector Control (TVC) hydraulic system, accompanying Auxiliary Power Units (APUs), and Booster Separation Motors (BSMs). The aft skirt provides the structural attachment to the Mobile Launch Platform (MLP) through four attach points and explosive bolts. The single exhaust nozzle is semi-embedded and is movable by the TVC system to provide pitch and yaw control during first-stage ascent. The Space Transportation System (STS) forward skirt, frustrum, and nose cap are replaced by a stage adapter that houses the RSRB recovery system elements and a roll control system. Stage 1 is approximately 133 ft long and burns for 128 sec. After separation from the second stage, Stage 1 coasts upward in a ballistic arc to an altitude of approximately 250,000 ft, subsequently reentering the atmosphere and landing by parachute in the Atlantic Ocean for retrieval and reuse similar to the current Shuttle RSRB.
Stage 2 is approximately 105 ft long, 16.4 ft in diameter, and burns Liquid Oxygen (LOX) and Liquid Hydroxen (LH2). (This was changed to 5.5 m in diameter at the close of the ESAS.) It is composed of an interstage, single RS–25 engine, thrust structure, propellant tankage, and a forward skirt. The interstage provides the structural connection between the Stage 1 adapter and Stage 2, while providing clearance for the RS–25 exhaust nozzle. The RS–25 is an expendable version of the current SSME, modified to start at altitude. The thrust structure provides the framework to support the RS–25, the Stage 2 TVC system (for primary pitch and yaw during ascent), and an Auxiliary Propulsion System (APS) that provides three-axis attitude control (roll during ascent and roll, pitch, and yaw for CEV separation), along with posigrade thrust for propellant settling. The propellant tanks are cylindrical, with ellipsoid domes, and are configured with the LOX tank aft, separated by an intertank. The LH2 main feedline exits the Outer Mold Line (OML) of the intertank and follows the outer skin of the LOX tank, entering the thrust structure aft of the LOX tank. The forward skirt is connected to the LH2 tank at the cylinder/dome interface and acts as a payload adapter for the CEV. It is of sufficient length to house the forward LH2 dome, avionics, and the CEV Service Module (SM) engine exhaust nozzle. Stage 2 burns for approximately 332 sec, placing the CEV in a 30- x 160-nmi orbit. After separation from the CEV, Stage 2 coasts approximately a three-quarter orbit and reenters, with debris falling in the Pacific Ocean.