Critical Call: Rigorous Quality Control at NASA Isolates Space Shuttle Main Engine Flaws
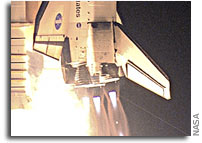
This article appears in the 27 June 2005 issue of Aviation Week & Space Technology
Reprinted with permission of Aviation Week & Space Technology – www.aviationnow.com
The NASA/Boeing-Rocketdyne Space Shuttle Main Engine project is correcting flaws in critical Honeywell SSME electronic components that could have caused a potentially dangerous launch pad abort.
The manufacturing defects, found in Honeywell SSME Block II engine controllers, caused a shuttle engine to shut down in 2004 during ignition on a rocket test stand in Mississippi, says Gene Goldman, SSME project manager at Marshall Space Flight Center in Huntsville, Ala. That SSME controller had already flown four shuttle missions and was being acceptance- tested for additional flights.
The “several month investigation” stemming from the incident is causing Honeywell and NASA to replace about 1,600 electronic capacitor components in all 20 of the program’s engine controllers. The flaw is no longer a flight safety concern.
The same capacitor manufacturing “misalignment” characteristic involved in the engine shutdown was found in other Honeywell SSME controllers. “We wanted to make sure that none of these slipped through,” says Goldman. And the type of capacitor causing the concern “is used at multiple locations and for multiple purposes inside each controller,” he adds.
“All of the controllers are being purged” of the suspect components, says Mike Kynard, deputy SSME project manager.
The SSME program’s rigid test and quality control procedures have also detected a totally different type of capacitor manufacturing flaw on planned Advanced Health Maintenance System additions to the engine, separate from the controller’s internal components. And those other flawed parts also are being “purged” from the program, says Goldman (see p. 23). An unrelated Pratt & Whitney oxygen pump seal issue is also being assessed.
The action on the Honeywell controllers is a sharp reminder that in spite of enormous public and media attention on Columbia debris and in-orbit repair issues (unlikely to be a shuttle problem again), the inherent risks and rigid safety measures associated with the rocket engine side of the shuttle will always be a huge challenge. That point has never been lost on NASA and contractor shuttle propulsion managers and engineers, who have maintained an extremely aggressive SSME test and quality control program during the last two years.
In the failed controller test that caused large numbers of capacitors to be removed, the engine cut off 1.5 sec. into its start sequence on a stand at the Stennis Space Center, Miss. The controller is the large, complex computer box mounted on the exterior of each shuttle main engine. It controls and monitors thousands of SSME parameters, including the critical start sequence. Launch pad aborts have occurred safely five times in shuttle countdown, mostly because of oversensitive instrumentation. But they are supposed to occur only in dire engine emergencies.
More Flaws Intercepted Craig Covault/Kennedy Space Center Quality control for the shuttle main engine project has caught manufacturing flaws in electronic components intended for the new SSME Advanced Health Monitoring System (AHMS). These are in addition to the problem components found in engine controllers. The AHMS will be used starting in late 2006 to sense abnormal engine vibrations to trigger emergency shutdowns. The health-monitoring-component flaws were discovered in bench testing of the parts, not a firing test as with the controller. “It was another manufacturing defect . . . and we have also purged the system of those types of parts,” says Gene Goldman, SSME project manager. These flaws were found well in advance of integration of the components with flight engines. In this case, the manufacturing flaws were found to stem from “internal mechanical stresses caused by rapid expansion of water vapor internal to the capacitor, during the soldering process.” The SSME project and its contractors maintain tight test and control procedures to catch such flaws, says Jim Paulsen, Boeing/Rocketdyne SSME program manager. Neither of the capacitor problems is expected to be a major issue at this week’s Flight Readiness Review, because managers believe fixes are well in hand. The SSME quality control program has also discovered cracks at two knifeedge seal locations in Pratt & Whitney liquid oxygen pumps, an SSME topic that will be discussed at the FRR. Micro cracks were discovered using dye penetrate examination. The “tooth seal” areas where the cracks were found are extremely small, only twenty-thousandths of an inch wide. One area involves a four-tooth seal; the other, a twotooth seal. “We have found the condition in several oxygen pumps,” says Goldman. Five cracks in total have been discovered in various engine pumps, some where material is now missing. But due to the location and nature of the defect, “it is not a downstream foreign object damage concern nor something that could lead to a catastrophic engine failure.” Testing and analysis indicate the problem involves high-cycle fatigue in the affected engine pump area. Only parts well below the fatigue life of the components involved will be flown. |
There are about 80 capacitor assemblies of the type that caused concern in each of 20 SSME Honeywell main engine controllers, says Kynard. Twelve of the controllers have had the changeout, and eight others are in the cue.
In addition, NASA and Honeywell have issued a formal warning to the rest of the aerospace industry about the use of this type of capacitor with the manufacturing defect, says Goldman.
The engine controllers on the orbiter Discovery have already been equipped with the new capacitors, as have those on Atlantis and its backup engines to support the shuttle’s return to flight— pending the pivotal final Flight Readiness Review here late this week. The FRR, set for June 29-30, will involve more than 100 NASA, contractor and safety personnel from across the country. It will be the final program-wide safety and engineering review to commit the shuttle back to launch, 2.5 years after the loss of Columbia and her crew.
During the FRR, managers will discuss final assessments on external tank ice-debris risks to the orbiter, and other issues. The FRR will also include Marshall Space Flight Center/contractor review of a Pratt & Whitney SSME liquid oxygen pump seal fatigue-life issue. This is unrelated to the engine controller and the health monitoring capacitor manufacturing flaws.
If the FRR assessments, especially on the ice-debris issue, are satisfactory, the FRR team will set a formal Discovery STS-114 launch target within the July 13-31 launch window to the International Space Station. The FRR will follow the planned meeting earlier this week in Washington of the Stafford- Covey Return to Flight Task Group. That June 27 meeting is to be the group’s final meeting to determine whether NASA has fulfilled the 15 recommendations of the Columbia Accident Investigation Board (CAIB).
“Since the Columbia accident, there has been a lot of public visibility on the orbiter,” says Jim Paulsen, Boeing/Rocketdyne program manager for the SSME. “But we took the CAIB report very much to heart throughout the SSME program too, and the engine program has not sat idle during this time.” Finding the potentially hazardous controller electronics flaw is “a good example of why the shuttle engine program tests extensively to find problems that we did not know could even exist,” says Goldman.
This was the case with the SSME controller electromagnetic filter capacitor tank, insulation and repair of the or isolated as the cause of the engine shutdown at Stennis. “It was the first failure of this kind that we had ever had, and it exhibited itself [in a manner] there was no way to screen for at the time,” he said. This particular type of capacitor is made by bonding thin layers of material together.
The accuracy of the material alignment in manufacturing plays a role in whether the capacitor would fail after a certain number of thermal cycles. When the separation occurs, the electrical contacts in the capacitor no longer function properly, says Goldman. The industry standard screening process and additional Rocketdyne standards on how to screen for problems with this type of capacitor proved inadequate to weed out the kind of failure that occurred.
“We have found other parts that had this flaw, this misalignment, but we do not know whether it would have resulted in a failure somewhere downstream, or at what point in time any additional failure would have occurred,” says Goldman. “Honeywell has modified the manufacturing technique to make sure the condition no longer exists [in newer parts] and the capacitors are now being hermetically sealed to minimize thermal stresses.
“We have assured ourselves that the manufacturing and inspection of those parts now meet [new] standards that will ensure that we do not have the same condition,” says Goldman.
Honeywell public information managers Bill Reavis and Ron Crotty told Aviation Week & Space Technology they hoped to provide Honeywell executives or engineers to comment on the problem, but were unable to do so by the magazine’s publication deadline.