Wayne Hale’s NASA Blog: Shutting Down the Shuttle
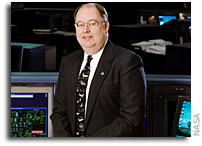
Shutting down the shuttle
I believe it was General Norman Schwartzkopf who said: “Arm chair generals study tactics; real generals study logistics”.
One of the first lessons I learned in program and project management is that attention to the details of supplies, vendors, and parts manufacturers will determine success or failure more than anything else that management does. They are not glamorous, Hollywood does not make movies made about them, but logistics and supply chain are the unsung pillars on which every major project rests.
It is nice to have eloquent oratory and high flown philosophical statements, but the real way that real programs are really controlled is through the money. When the logistics and supply budget is stopped, the program is over. Momentum and warehoused supplies can carry on for a short period, but when those are exhausted, its time for the museum.
Starting four years ago, the shuttle program in its various projects made “lifetime buys”. That is, we bought enough piece parts to fly all the flights on the manifest plus a prudent margin of reserves. Then we started sending out termination letters. About two years ago, we terminated 95% of the vendors for parts for the external tank project, for example. Smaller, but still significant, percentages of vendors for SSME, Orbiter, and RSRB have also been terminated.
A lot of things that go into the shuttle build up are specialty items. Electronics parts that nobody makes any more (1970’s vintage stuff). Hey, if it works, why invest money in certifying new parts? Certifying new ones would be even more costly! Specialty alloys to meet the extraordinary demands of space flight, parts that are made by Mom and Pop shops mostly in the LA basin are norm rather than the exception. You might think that simple things like bolts and screws, wire, filters, and gaskets could be bought off the shelf some where, but that thinking would merely prove how little you know about the shuttle. The huge majority of supplies, consumable items, maintenance items, they are all specially made with unique and stringent processes and standards.
Our shuttle history tells us that when we try to cut corners, trouble results. Small, even apparently insignificant changes have caused big problems. For example, the unheralded end of production of a solvent caused enormous complications for the SRB folks a few years back when things started falling apart unexpectedly. It took a huge engineering detective effort to determine that small chemical changes in the new solvent were the culprit. Anything coming apart in the SRB is not good. There are hundreds of similar examples.
There is a long and arduous process to certify a vendor to produce the logistical parts for the shuttle. Not many companies do this work. Almost all of them are extraordinarily proud of the role they play in America’s space program. A lot of them have been there from the beginnings in the middle 1970s. So when a Mom and Pop specialty shop gets a termination letter from the shuttle program after 35 years of production and they have other customers, guess what happens? Mom and Pop decide to close the shop, pension off their highly skilled workers, and then Mom and Pop move out of LA to their retirement cottage in the mountains or at the sea shore.
A lot of this has been happening over the last four years; most of it over two years ago.
So, just for the sake of argument, lets see what would happen if somehow we decided to fly the shuttle some more flights?
From time to time a vendor of specialty parts for the shuttle has gone out of business. Our experience then is that we have immense problems getting anybody to even bid on making replacement items. Sometimes, with hat in hand, we have to knock on doors. Always, we have to offer premium payments to get those exotic, small production run parts made.
Given time and money, anything is possible. But we are always short on time and money. Life seems to be like that.
To take one little example: if we started today to build another external tank at MAF, there are probably enough parts on the shelf. But very shortly we would exhaust supplies of some parts. Maybe on the second tank — which we need to start in 3 months or so — would have to get a new supply of specialty parts. Sometimes the old vendor is still there and could be persuaded to make more of the old parts. But in many cases, a new vendor would have to be found. Since the production run would be small, a premium price would have to be paid; and a certification effort requiring 6 to 12 months would start. Initial production likely would have a number of rejects as the workers learn the process. Hmm. In probably 15 to 18 months would would have the parts to build that second tank — only a year or so later than we needed them. So a new gap would form. Not between shuttle and orion but between shuttle and shuttle.
And what would we get: even higher price per flight of an old technology which is not nearly as safe as we would like . . .
Hey, I am the biggest shuttle hugger there is. I think it is the best spacecraft ever built. But I also deal in the real world.
Where does the money come from? Where do the people — who should be working on the moon rocket — where do they come from?
We started shutting down the shuttle four years ago. That horse has left the barn.