Transcript of a NASA Press Briefing with Bill Parsons, Wayne Hale, and Bill Gerstenmaier
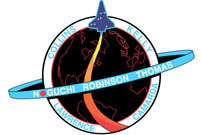
PRESS BRIEFING WITH
BILL PARSONS, SPACE SHUTTLE PROGRAM MANAGER
WAYNE HALE, DEPUTY SPACE SHUTTLE PROGRAM MANAGER
BILL GERSTENMAIER, INTERNATIONAL SPACE STATION PROGRAM MANAGER
Johnson Space Center
Houston, Texas
Friday, April 29, 2005
(TRANSCRIPT PREPARED FROM A TAPE RECORDING.)
MS. KLEM: Good morning, welcome to Johnson Space Center for the continuation of our return to flight status briefing.
Here with me today are Bill Parsons, the Space Shuttle Program Manager; Wayne Hale, the Deputy Space Shuttle program Manager; and Bill Gerstenmaier, the International Space Station Program Manager. The gentlemen have a few opening remarks and then we’ll open it up for questions here at the Johnson Space Center and other centers.
Bill?
MR. PARSONS: Good morning. You earlier heard from Mike Griffin and Bill Readdy, and I don’t have a great deal to add.
I would say that we have often told you that we were milestone driven and that we had a number of reviews that we had to go through building up to launch. As we’ve gone through those reviews, we’ve learned new things, as we anticipated we would. And in this case when we had the design certification review down at the Kennedy Space Center and then the debris verification review here at the Johnson Space Center last week–or this week, we determined that it was the work and the analysis that we had to do and other things that we learned in those reviews, it was the best thing for us to move along to the July window.
A lot of people have done some great work. We have processed the orbiter. We have moved it out to the pad. We have had a tanking test, which again we’ve learned a great deal during that tanking test. We will keep the orbiter and the vehicle out at the pad for some time to do some troubleshooting and to continue to do processing, and then at some point in time we will decide to move the vehicle back to the vehicle assembly building and then do additional things that we need to do to get ready for the STS-114 mission.
With that, I’ll just wait and get your questions later.
MR. HALE: Let’s see. I told him I’d put it in a little bit of a context. As you know, the foam off the external tank caused the Columbia disaster, and we have been working very hard for the last two and a quarter years to eliminate any debris sources that can strike the shuttle heat shield and cause a catastrophe of that sort in the future.
We concentrated on the foam because that was the cause of the accident, but we knew that we had to do an exhaustive search through everything that could be a potential problem. After a great deal of test and analysis we’ve been able to take some 175 potential debris sources off our worry list. We believe we’ve mitigated those or they’re not a concern, and we have the engineering evidence to prove that they’re not a concern.
We knew that we had three or four more items to work on, and we also knew that there was this ice that forms on certain places on the external tank, which we thought was probably not a major concern, but we need to ensure that. So what you’ve seen here I think is the diligence and rigor of going through every piece of the process to ensure that we’ve eliminated or at least to the best of our ability mitigated a hazard from (?) and debris, that we’ve come to the conclusion that we really need to do something about this ice. We have a plan to deal with it–actually, we have several options to deal with it, and it is going to take us just a few more weeks to deal with that problem, and we certainly cannot fly until we have convinced ourselves that it’s safe to fly.
That’s been our principle from day one on this journey to return to flight, and that’s what you’re seeing here played out in front of you.
The testing on the ice lagged behind the testing on the foam. The engineering analysis was clearly put in second place, and that’s why it’s taken us to this point, but we knew we were going to have to do the work before we can go fly, and we knew that if our intuition that the ice was not a problem was wrong, we were going to have to deal with it. We had a plan, as I said, really three plans, on how to deal with it. And now that we know that we have to do something about it we’re going to execute that plan.
And we are very open about it. I think you guys have had a great deal of information on that, and will continue to see us be very open about the status of our analysis and our progress toward return to flight.
Now, our customer, as it were, Bill Gerstenmaier of the International Space Station Program, we keep them informed, but I want to let Bill tell you a little bit about what they’ve done and where they stand with all of this.
MR. GERSTENMAIER: Okay, thanks, Wayne.
This morning I talked to the International Partner Program Managers, my counterparts in Russia and Europe and Japan and Canada, and I talked to them about the delay from the May/June window into the July window.
And I think each one of the partners was a little disappointed in the fact that we’re not going to be in that first window. They were really getting prepared and excited, but I think they understood clearly what the rationale was, and they’re 100 percent supportive of the decision that was made by the shuttle program to essentially move to that second window.
From an overall space station standpoint, we’re still in very good shape. We’ve been planning for an 18 Progress launch on the 17th of June. That’s still in work. We were planning that manifest two different ways, one if the shuttle launched and one if the shuttle didn’t launch, so we have that second manifest option all ready to go. We’ll put a little extra water on that Progress. We put a Rodneck(?) tank on that Progress vehicle to carry extra water, and we’ll carry some water up. That will be our tightest consumable coming into the spring, will be water, and we’ll be right around skip cycle at the time that the Progress docks.
But again, it looks fine from a water standpoint, and we were planning that kind of all along.
There’s another Progress in August, and we’ll do the same kind of thing. We’ll do a dual manifest planning for that Progress in August. We’ll do one with or without the shuttle and we’ll be prepared to operate either way.
Cargo down at the Cape, it’s in the canister. The MPLM is in there; the CMG is in there. It’s in the vertical position. It’s ready to be installed in the orbiter. We can stay in that configuration for an extended period of time all the way through September, so there’s really no issue with any of our hardware down at the Cape. It will just stay packed up and ready to go.
Also we’ve looked again, and the partners offered, that if there was anything that they could do to help in terms of either moving manifests around or changing cargo, they were willing to do anything that was possible that would help us overall. We’ll look potentially at the Soyuz in September, see if there’s some things there we may want to go ahead to do to help give a little larger window for the shuttle in that timeframe.
But again, I think the partners understand the decision. They’re very supportive. I can’t imagine a bigger supportive team that supports the shuttle program as much as my partners. They are willing to do anything that is required, and any way they can help out, help return the shuttle safely to flight, they’re willing to do their part and do what it takes. So again, I think the shuttle team has the benefit of the backing not only of their team that supports them but also the International Space Station team.
Thank you.
MS. : Let’s start with questions here on the side and we’ll work over. Mark?
QUESTIONER: Thank you. This is Mark Carreau, the Houston Chronicle. My question is for Bill Parsons and Wayne Hale. Could you discuss the points, the fixtures on the tank that the ice forms on that you’re most concerned about? I think you did lay a really nice foundation for this after the April 14th tanking test, but could you also explain if that tanking test was sort of the milestone that really brought this issue to the fore? I think there’s– it’s not quite clear to me whether that’s really the case or not. And just those fixtures that you hope to deal with where the ice is originating that you’re talking about.
MR. PARSONS: I’ll give it a shot and then I’ll let Wayne fill in the blank spots.
First of all, the tanking test was done on a relatively low humidity day in Florida, and so we started out with about 50 percent humidity, and then we–and then it climbed during the day. But overall, we didn’t have the kind of humidity to grow a lot of ice. We looked at the feed line bellows area and on that particular day we would have been okay to launch, based on our assessment of the amount of ice that was there.
So in some ways it didn’t give us a great deal of information about what it would be like on a high humidity day, which we would expect in a May/June window or even a July window. But it did tell us how well the drip lip would work in those particular conditions.
Again, that LOX feed line goes all the way down the external tank, and along that way, of course, that’s where you’re flowing this cryogenic propellant. We have a couple of bellows along the way. It allows for that line to expand and contract as we load the propellants and then as we fly into orbit. And so that’s where some of the ice is formed, and I think you’ve seen pictures of that as well.
In addition to that, you have to hold that line on with brackets and those brackets have very thin pieces–thin foam applications on those, and so there’s some ice that forms around those bracket areas and so that’s another area that we have to be concerned about.
And then there’s other lines that go all the way up the top of the tank that have some brackets on them that we were concerned about, not as much about ice but some of the foam that’s on those lines as well.
Those were the three areas. What’s that line called, the prepress line? Those were the three areas we were coming out of the initial debris verification review that we needed to go look at more and understand better, and that’s why we were really holding the delta debris verification review.
During that they went off and they looked at a lot of imagery, on-orbit imagery and on-the-ground imagery. We had people did an awful lot of research to look at what kind of ice would form. We had some testing fixtures that we had built and we started doing testing at the Marshall Space Flight Center and at the Stennis Space Center. And some of that testing was–that information was just breaking here as we came into the debris verification review.
So you kind of added all that together, plus the analysis that was being done with our folks on transport and other things, and when that was all put together it told a story. And when we heard that story, then we had to make some decisions about what we needed to do.
Wayne, you may have–
MR. HALE: Well, I’d just say that one of the things we’ve learned, or I’ve learned anyway, is you have to be very careful with your every-day intuition in this business because what we’re dealing with defies every-day intuition, whether you’re talking about orbital mechanics or in fact ice.
We’re doing a lot of testing of impact, when you shoot a hunk of ice at the tile or a reinforced carbon- carbon panel. One of the things we’ve found out is that the density of that ice really doesn’t matter. It can be really hard ice or it can be kind of slushy ice, and it really doesn’t make any difference. The damage is about equivalent. That’s counter-intuitive. Most of us–I certainly did–most of us thought that if you had low- density ice you probably had less risk. Our testing now shows that’s probably not the case.
In the very recent testing that we’ve been doing at the Red Stone Arsenal at Huntsville, Alabama, put this assembly where we generate the ice, in an acoustic vibration facility and subjected it, after having grown ice, to the shake, rattle and roll that it has during ascent. And we found out something very interesting, which is the hard ice tends to hang on better because it just grows into the little pores in the foam or for other reasons. And the soft ice tends to come out easier.
So the days that we really thought, when we built this inspection criteria, were going to be okay-to-launch days, now that’s not panning out. The test data shows that they’re probably not good days to go launch even with this lighter amount of ice. So we’re going to have to deal with it, and that’s kind of the bottom line, is the last set of tests that we’ve been doing it–and in fact still continuing on–are showing that we have more concern over this ice than every-day intuition would tell you we needed to have. And that, more than the tanking test, was the reason that we decided that we need to do something.
QUESTIONER: Nancy Holland, KWTV. Are you going to at this point try to put some sort of heater on this tank? And you mentioned that there were a couple of additional things in addition to the ice that you had concerns about. Could you kind of tick off what those additional concerns are as well?
MR. : We are going to try to install the heater. We’ve been working on this heater for this area for quite some time. We also did a modification on the LOX feed line bellows are and did a drip lip, and we thought that drip lip would reduce the amount of ice to a point that would allow us to be able to fly and accept the risk. Again, our understanding has grown over time, and we continue to do testing and understand this better, but the whole time we were doing that, we were doing a design for a heater to eliminate this completely, as not even–well, we didn’t even have to worry about any risk whatsoever.
And so we continued to do that design, continued to build towards that. We had it on the third tank, which is currently at Michoud. And so we have the kits that are in work to be retrofitted to the tanks that we have now. Again, as we learned more and we realized that this was something that was not acceptable to the program to have ice in this area, then we will retrofit the two tanks that we have and the next flight we have will have the heater modification on that tank.
The second part of the question was?
MR. : The second part was the other work that we’re going to do, and that really is there are four foam applications on the external tank in the very forward part of the tank, up near the nose, that we did not change. We didn’t redesign, we didn’t reapply, that have a little bit of a history of voids inside that we’re going up to do a little more statistical analysis on.
We think that’s going to be okay, but the fact of the matter is we have to do the engineering analysis to prove that it’s okay before we’re ready to go fly. There’s always the risk that we might do that analysis and come back and say we’ve got to do something else, but right now we don’t think we’re going to have to. But those four foam applications are up in the nose and forward part of the external tank.
MR. PARSONS: And in addition–I told you about the brackets that hold this LOX line on, and those brackets create some ice. We have to understand that ice and understand if there is a mechanism that can cause that ice to come loose and be transported and cause damage to the vehicle.
Again, this is one of those things we believe we understand, but we still have some analysis that we’re going to do, and it could cause us to–I mean we may have to make some changes there. I know that we will be looking to make changes–any area that’s growing ice we’re going to try to eliminate it, and that will be done over time. Even if it’s a little bit of ice, we would like to eliminate it, so we’ll continue to work and look at this external tank and eliminate those sources.
But again, we believe through analysis we’ll show that that’s probably okay. We’ve still got a little work to do in those areas though.
QUESTIONER: Kevin Quinn with KTRK. Would you in your estimation characterize this as a setback or not? And the second part, do you feel that all the requirements of the Stafford Covey group will be met by July?
MR. : Well, we would always like to have made the May/June window. It would have been–it was something we were working towards. We had gotten the hardware processed and we were working towards that. We had shipped the external tank. But I think all of us knew that we had a lot of work to do. We were doing it concurrently as we were processing the hardware, and we realized that we were going to learn things along the way and that we might have to take a step back and go do some other things.
I think that getting the hardware down to the Kennedy Space Center was very important and was the right thing to do. I also think getting the vehicle out to the pad and being able to do a tanking test–we’ve learned a great deal through that tanking test. And we found some issues that we need to go work on and some things that we need to fix. I think Bill Readdy said it was October 2002 when we had the last vehicle out to the pad. So this has been a great learning experience for us, and to refresh a lot of things that we haven’t done in quite some time.
So in my mind these are successes, they’re all moving towards a launch date, and the right launch date because we’re learning things as we go along. Is it disappointing? Sure, it’s disappointing. I mean we would have liked to have cleared all these issues up and been able to make it out to the pad and launch in the May/June window. We were–if things had gone our way and exactly as we anticipated, we would have been able to do that. But they haven’t, and so we’re going to take a step back and do it right.
QUESTIONER: Mark Evangelista with the Clear Lake Citizen. My question is for Mr. Gerstenmaier. Could you give us an update on the CMGs and talk about the impact of not being able to fly those to station? And also an update on maybe how oxygen generation is going on station.
MR. GERSTENMAIER: I can do both of those. In terms of the CMGs we still have two good functioning Control Moment Gyros on board station. We continue to watch those very closely, and we’re pretty conservative in the way we use those CMGs. We limit the amount of motion they have, and it seems to be doing very well.
We won’t do anything different even with the shuttle slip. We’re good in this configuration. If something were to occur and we had a CMG failure and we would be in a potentially high-propellant usage mode, we’ve got some attitudes we can go to minimize the amount of propellant usage, and we could always go EVA if we had to and do the little patch panel reconfigure to regain another Control Moment Gyro.
So again I think really nothing has changed, and we’re still in a good stable configuration. Things are fine with respect to CMGs and we’ll get the one changed out and get the patch panel switched whenever shuttle return to flight is, so that’s not big issue to us.
In terms of oxygen generation, the electron is currently not operating. It ran I think yesterday or the day before for about 3 hours. This unit is kind of at its end of life. We’re trying to get as much run time out of it as we can, and eventually we’ll switch to another unit, Unit 6. At the right time the Russians will make the decision to go do that. Even if the electron doesn’t come back and generate any oxygen from now until the Progress. We’re fine.
We have enough oxygen stores on board station and enough oxygen stored in solid fuel candles that we can operate without any concerns. And then the Progress that comes in June, it docks on June 19th, it will carry about 110 kilograms of oxygen on it, and again that will carry us through to the next Progress, again, without any functioning electrons. So again we’re in a fairly stable configuration overall in terms of oxygen and Control Moment Gyros.
MS. : Let’s go to NASA Headquarters, some initial questions there. We’ll come back here if we have time.
QUESTIONER: Tracy Watson, USA Today, for Mr. Hale or Mr. Parsons. I’m wondering if this extra time you’ve got is going to allow you to tackle some other things maybe with imagery or TPS repair that you wouldn’t have had the time to do with a May 22nd date?
MR. : Well, in all those areas we’ve always had forward work planned, and even if we had launched 114 on time we would have continued to work on TPS repair and imagery and other things, and so we were always–had things that we were going to do to improve in those areas. We will continue to work towards that, and there may be some improvement in our capabilities along the way.
I feel like that we already heard about a few improvements yesterday in the Program Requirements Control Board when they gave us–they laid out all the TPS repair capability that we currently have and what we would have as we march towards the future, so there’s some improvements already that we’re seeing that we might be able to have for the July launch window.
QUESTIONER: This is [inaudible] from Washington Post for Bill Gerstenmaier. Bill, is the problem that you have with the electron, could that have an impact on your ability to provide enough oxygen in case of the need for safe haven?
MR. GERSTENMAIER: Again, our calculations that we do for the CSCS capability assumes that the electron has failed and is not operating, so that’s taken into account in our calculations, in our numbers. So again the fact the electron’s not operating is what we’ve been prepared for and the way we’ve done the calculations so it has no impact to the CSCS durations that we’ve been quoting before.
QUESTIONER: Bob Zimmerman, UPI. This is for Bill Parsons or Wayne Hale. The ice that’s forming along those fuel lines in the three areas that you’re finding ice now, correct me if I’m wrong, is that ice forming because you’re no longer putting foam in those areas, or if that isn’t the case and you never put foam there, why was a heater not installed in those areas to begin with on the external tank that’s flying on Discovery? I want some clarity on why a heater wasn’t put on to begin with.
MR. PARSONS: I’ll try to explain that. As Wayne said earlier, we focused on what caused the accident and that was foam, and the (?) foam, and then we started looking at other debris sources. In our research of debris sources there were a number of areas that we put a lot of work into and tried to eliminate those debris sources.
Of course we did realize that–and by the way, along that LOX feed line bellows, what you have is, you have an area that has to be able to move. If you were to foam that area it would move, break the foam, and then create a debris source. And so what we’ve always done is we don’t put foam in those bellows areas. And so we’ve never done that. There’s always been ice that has been created there.
But when we did our initial research we didn’t see any evidence that ice could break loose and transport itself and damage the orbiter. Again, we were continuing to look, and we kept again focused on finding debris sources, but recently, just recently, as we have done in-depth evaluation of all the debris sources, we found that there was a transport mechanism and evidence that ice had actually contacted the orbiter and the SRBs.
And so with that new information and with the fact that we thought we had reduced the ice to a point that it would not be a problem, and we were going to go forward and continue to retrofit the vehicle–and by the way, we do a lot of things like that as we fly in space. We will find things that we will make improvement on in the next mission or the next mission, and we phase those in because of the way we have to do our design and everything else.
At that particular point we thought we could make it better, but we thought it was good enough until that new information came in and we realized it wasn’t good enough, and that we needed to go back and put this heater mod in. And so when we got that data and when we understood that data, we decided that we couldn’t make this window.
Wayne, do you have anything you want to add?
MR. HALE: No. You know, it’s a continuous improvement. I mean if you have a complicated system like a space shuttle or any number of things, you always want to look for continuous improvement, so we have a number of improvements out there. And we have the heater which had been a secondary emphasis to us in design, and in fact, we’ve completed the design and the design reviews and installed this heater on the third tank that’s in production in New Orleans, thinking that we’d have it for subsequent tanks. And now it’s just become apparent we need to go ahead and do something on the first two tanks that have been delivered.
So there’s a continuous improvement process, and what we’re really seeing is we need to accelerate this particular design improvement.
QUESTIONER: Hi. It’s Beth [inaudible] with Government Executive. Bill Readdy mentioned in the earlier briefing some new RCC data. Have you just explained all of that to us or is there something else that came through that you haven’t told us about yet?
MR. : I’m sorry. I didn’t–the new what data?
QUESTIONER: New RCC data.
MR. : That would probably most likely be the testing that’s been done, and particularly ice on RCC that’s demonstrated that this low-density ice has the same propensity to cause damage as high density ice. But I guess I’m speculating. I missed the first part of the previous conference, but I think that’s what it’s got to be.
MR. : I mean there’s still some–I mean just recently at the debris verification review we did get some additional information about impact tolerances on RCC and tile. And that may be what he’s talking about, but most of this we’ve been–you have almost gotten it as fast as we have.
QUESTIONER: This is [inaudible] with Aviation Week for Bill Parsons. Could you describe the process of installing these heater kits on the tanks that are already in Florida? And also could you elaborate a bit on the troubleshooting for the liquid hydrogen sensors that came up during the tanking test?
MR. PARSONS: Okay. Well, I can give you my understanding of the installation process for the heaters. First of all, you don’t have access at the pad. You cannot do this kind of work at the pad, so we would have to be in the vehicle assembly building. We can do this work with the orbiter attached to the external tank and it sitting in the cell there, the integration cell. So we do have good access to that. What you do it’s a heater that’s very similar I think to the heater on the RSRM joints, so it’s a heater that we understand very well. It’s something that we’ve worked with.
You put it up inside the bellows and you really have to make a place for it again, remove some foam so that you can put that heater in place. And then there’s some bonding that you have to do and some foam sprays that you have to do in there, of which they–again, they’ve practiced and worked on at Michoud. And then you have to run the wires back inside I guess the inner tank area to where you can make the connections for the heater joint. It’s been described to me as relatively easy, not a difficult installation.
They also worked on removing it to see if in fact you put it in and you wanted to take it back out because some other mitigation that we’re working on, we might use something else other than the heater if we found that we might have a problem or something like that.
You can actually take it out and cause no harm. So in some ways they’ve done a lot of testing, and again, there is some risk involved in any kind of work that you do like this, but it was described to me from the folks that do this work it was fairly low risk.
The troubleshooting on the sensors. When we did the tanking test we had a couple of sensors that failed. We didn’t know if the sensors were bad or if we had a line problem. It turns out that you can check the sensors out, and we did, and it appears that the sensors are working correctly.
So then we started looking at possible connectors that are up in the–after the orbiter. We’ve gone through and done a number of wiggle tests and looking for any kind of connection and any wiring that might have caused these sensors to fail. At this point in time we have not been able to find anything that we can point at definitively. So that troubleshooting continues. But we do have to figure this one out before we can go fly. So we will continue that troubleshooting while we’re out at the pad, and try to determine what we need to do if anything.
MS. : Now we’ll go to the Kennedy Space Center for questions.
QUESTIONER: This is Mike Cabbage with the Orlando Sentinel for either Bill or Wayne. I realize it’s still early here but can you talk a little about the sort of road map ahead now? I understand that TCDT is still on tap for next week. You talked about troubleshooting you want to do. I guess there’s also been discussion of another tanking test. At some point you’re going to have to roll back. Just in general what is your game plan and what sort of time frames are you looking at for rolling back and then going back out to the pad and that sort of thing as far as you know right now?
MR. PARSONS: Well, let’s see, I’ll give it a shot, and I’ll let again Wayne fill in the blanks.
First of all, we don’t have a plan completely put together yet. That’s something that the Kennedy Space Center is working on right now. We have people here at the Johnson Space Center that have to look at the troubleshooting plan, the fault tree. That’s been in work for a couple of days, but we’ll probably need the weekend to continue to work on that fault tree and determine which are the first things we should go look at, which ones create the most problem for us. If we were to find out that we needed to go change out the sensors or something like that, that would be a fairly long work item, and so we need to go ahead and figure that one out first.
So what we need to do is get that fault tree laid out and determine which ones are the hardest to perform the work afterwards if we were to find out that that work was required, and try to eliminate those or determine if that’s what the problems are.
So between the external tank people, the people here that work on the main propulsion system here at Johnson Space Center and the Kennedy Space Center looking at all the different options, they’re all collectively getting together, working their way through that, and we think we’ll probably have a plan put together early next week.
So currently we’re going to let these folks do their job, make sure that they are thorough in their assessment, and then come back to the program and offer us their suggestions. So I really couldn’t speculate when we would roll back. I’d have to see the troubleshooting plan and everything that we need to go do.
What we would like to do is get as much done–and I think Bill Readdy laid this out–get as much done as we possibly can while we’re out at the pad, do some things that are fairly–the milestones that we could get behind us that we wouldn’t have to repeat once we came back out to the pad, and then we’ll determine we can roll back.
And the heater kit, the mod kit is not available even till May the 5th. So we won’t have it at the Kennedy Space Center till May the 5th. So we have until then to get the vehicle back into the VAB to start that work. We may decide to take some of those contingency days that Wayne talked about, those 20 contingency days, continue to do some work out at the pad and retrofit the second tank, and then have that possibility of bringing the vehicle back and moving Discovery over to the next stack and rolling back out to the pad.
So we have many options and many different ways that we can go do this, and we just need the people at the Kennedy Space Center and the troubleshooting folks to determine what’s the best course of action at this point.
Anything to add?
MR. HALE: The only thing I’d add is I think our folks are really happy to have both of us over here talking to you today so they can get this work done and we’re out of their hair. So it is a complicated scheduling problem with a lot of options, and we will have a plan early next week, and I’m sure that there will be a couple of places where we can change direction depending on what the outcome of some of our testing is.
QUESTIONER: And I have a follow-up question also for Bill or Wayne. You mentioned just a moment ago the fact that at the top of the liquid oxygen line, in addition to the joints where you get ice is also brackets. Talk about how you would mitigate any sort of ice buildup on those brackets, anything that you’re looking at right now?
And one other real quick final question. I’ve seen several launch dates flying around out there. Could you confirm that the opening of the window is July 13th and give us a launch time on that date if you have one?
MR. : Sure. The launch, the window opens on July 13th. I think it goes through July 31st. I’m pretty positive about that. We believe–it’s 4 o’clock in the afternoon, 3:45, 4 o’clock in the afternoon, somewhere in that range. We’ll pin that down a little bit closer for you, but it’s about the same time that if we had launched on May 15th it’s about the same time as that for the July 13th opening of the window.
As far as the feed line brackets, some things that we’re looking at is some heat source that we can put on the pad to them possibly melt that ice or keep the ice from growing at a rate that it would cause a problem. That is one thing we’re looking at.
We’re going to do some testing to see if that would actually be a benefit or might cause more issues. We don’t know that yet. We need to go do some testing.
And we’re also looking for the future for some different materials that we might use in that area that might again reduce the amount of ice in those areas. There’s a lot of folks still looking at other things as well, and I can tell you they’ll bring them forward just as soon as they think they’re viable and that they would help us to again further eliminate debris sources.
MR. : I would just add that the NASA Engineering Safety Center has provided us with a design option to put a shrink-wrap plastic around some of these areas that could also be helpful in preventing ice from forming, and yet would articulate as the vehicle shrinks and expands with the thermal changes. So there are a couple of other options that we’re going to continue to look at that are perhaps a little less mature than the heater design.
And if we find that additional work is necessary or if the heater doesn’t pan out–because quite frankly we have a little bit of testing left to do on that–then we have a backup plan. I mean that’s kind of rule 1 in this business, is you don’t put all your eggs in one basket. You have a plan, but you also have an alternate of a backup plan and probably a couple of those just in case it doesn’t pan out.
QUESTIONER: Bill Harwood with CBS with a question for Wayne I think, or maybe it’s Bill, I’m not sure. That recirculation–not recirculation, I’m sorry–the pressurization relief valve I guess that was cycling more than expected–and this may be a dumb question–but is there any thought that the bipod heater could have played a role in the operation of that–and I guess I’m just interested philosophically in the law of unintended consequences–if you’re putting the heater on the bellows itself, I’m just wondering if any of that is something that is a potential problem for you down the road.
MR. : Well, changes that we made to the tank and including taking a bipod foam ramp off and putting a heater in there are blocks on the fault tree that we have to go through and conclusively demonstrate did or did not contribute. I personally think that’s low priority, but then I made a little speech a while ago about every-day intuition can mislead you. We’ve got to be rigorous and make sure that’s not the problem. It’s a little bit of a puzzle to us and we’re going to have to do some troubleshooting.
It is possible that one of the changes that we made to the tank contributed to this situation. There were other things that were done to the tank that had nothing to do with the Columbia accident, in fact had been done to this particular tank before–in fact, years before it was being assembled–the accident, that could also contribute.
And we’re in the process of laying all those things out or the folks are, and we’ll work through all of them.
MR. : And, Bill, we’re always concerned about unintended consequences. As you make changes to this vehicle, you’d better be very careful to understand what those changes do to the performance of this vehicle.
So one of the things that we will be looking very closely at is when we put this LOX feed line bellows heater in is did we do no harm? And I think that’s the first rule, is do no harm.
So we’ve got to make improvements, not cause another issue, and so that’s part of the testing and qualification and certification of this piece of hardware.
QUESTIONER: Thanks. And one follow up for me for Wayne. On the ice and the recent testing that you’ve done, I mean we’ve got a sense of what size foam can cause entry critical damage, realizing there’s lots of variables, location, velocity, all of that. Can you give us a sense of what size pieces of ice have you concerned? I don’t have a clue.
And the second part of that question is, you know, obviously you flew 113 flights without a drip lip and without a heather, and so I mean part of this comes down to characterizing the risk, for me, which is were you just lucky in 113 flights with this ice? I don’t have a sense of how all that plays together.
MR. HALE: Well, as usual, Bill, you could have been right in the middle of our debate. We have done, as I say, the shake test out in Alabama where they have built a fixture and grown ice on it and put it in the acoustic environment. We had some pieces–now this is a 17-inch diameter pipe, that’s a pretty good size pipe–that’s got a small area that is exposed, that the cryogenic temperatures are exposed to the outside air and water can condense and form ice inside that cavity.
In some of that testing we liberated pieces as large as 5 inches long, so 5 inches by probably a couple of inches of ice. That’s a pretty sizeable piece of ice. We’re going up to a Mach 3 wind tunnel to throw pieces of ice into the Mach 3 air stream and see if ice will hold together. That’s going to be one of our tests that’s coming up. People at the wind tunnel I think have had to take some extra special precautions so that they don’t damage their wind tunnel.
So there’s testing going on. But clearly, a piece of ice that big going 3 times the speed of sound can do some serious damage. So we need to go understand a little bit about the dynamics. But the bottom line is if we can eliminate it, that would be the best.
MR. PARSONS: And, Bill, I would add too, this is a very complex problem because the ice can come off early in the flight and it doesn’t have a transport mechanism to ever get to the vehicle. There’s a small region in there when you’re at a particular Mach number that you have a transport mechanism that gets this ice to the vehicle. That’s what we’ve learned. And by the way, Bill, we learned that through a lot of research to previous damage that the vehicle had received.
We have hits on SRB cork. We’ve had–that we contribute to the LOX feed line bellows ice. We’ve had some hits in the tile that we contribute at this point in time to the LOX feed line bellows ice.
So that was the information that said, wait a minute, you know, yes, we have–maybe we’ve been a little lucky. Maybe we don’t understand this problem as well as we should, and therefore we need to go and understand this problem and understand if we’ve been lucky or if we’ve been actually–the design of this vehicle and the way that this ice comes off won’t transport it toward the vehicle. We determined that there is a very low probability, but still a probability that pieces of ice can come off and hit the vehicle and cause damage in the LOX feed line bellows area.
Because of that it became important to eliminate that. Once you know, you have to take action, and so with that knowledge we are taking the appropriate action.
Have you thought about installing rubber pockets on the areas where you cannot put heaters and so you could inflate them like on airplanes to break off the ice before liftoff?
MR. : You know, that is an idea that was floated, having an acoustic or a thumper type device the way wing leading edges on airliners have been installed on some airplanes to remove the idea. That concept right now is a little immature.
I got to tell you, it does fill me with some concern because now you’re putting something flexible and that could itself become a debris source as you go through the SM phase. And, remember, the outside of the foam on this external tank can reach temperatures of several hundred degrees due to the aerodynamic heating. You are traveling at three or four times the speed of sound while you’re still in the relatively low part of the atmosphere, so there’s a lot of aerodynamic pressure on. And so anything that you put that would stick out or be on the outside, you’ve got to be very careful that you didn’t add a new debris source to.
So that’s a thought that people have had, but it’s really immature. We’ve got absolutely no design or test ready to go today on that. I’m sure that that will go on our forward thinking as a potential future improvement, but it’s not a near-term idea that we would implement.
QUESTIONER: And what about rubber pockets that you could have come off the tank just a few seconds before liftoff?
MR. : Well, you got to–how do you get them off the tank? You know, you have a lanyard that goes, you know, 200 feet down to the ground. I’m not–these are all good ideas. We have brainstorming teams that are working through a number of ideas like this, but you got to recognize that many of them have drawbacks.
We’ve talked about things as bizarre as putting a jet engine on a tower alongside the external tank to blow hot air over it, dry, hot air over these areas.
There are all kinds of ideas out there. Some of them are better than others. Some of them pose more risk than the problem we’re trying to solve, quite frankly. Some of them are easily implementable in the near term. And some of them will take years to put in process.
So there’s the brainstorming team that’s got a lot of really good ideas, and they’re evaluating potential pros and cons for future application. But as I can tell you, for the near term we have three concepts that we’re working on. The heater that we’ve been talking about quite a bit. The IR, infrared lamps that we’re looking at installing alongside the launch pad that can focus some heat energy up on the tank and provide us some relief from some of the ice. The drawback to those is obviously you can only see part of the tank, you can’t see on the back side of where you might have ice, melt that. And a third one is what we call a sacrificial material that actually puts an insulating gel or beads up in this cavity and covers it with a Saran wrap or a shrink-wrap material to hold it in. And that appears to be not–it appears to be causing more debris problems than it’s solving, quite frankly, in our early tests.
But those are the three that we have in the near- term implementation state. We are most likely going to go install the heater, and I think that we are also likely to install these heat lamps at the base of the pad. But we have not made those decisions. We’re still working through the engineering to make sure that they’re the best options we’ve got.
QUESTIONER: This is Jay Barbree (ph) with NBC. First, Bill, I’m getting more confused. Do you know now if you are for certain going to install the heater on this tank?
MR. : Well, I think what Wayne is doing is he’s observing the right to make sure that we go through the rigorous process that we established for anything that we’re going to install on this vehicle. Currently there’s still some testing that needs to be done on these heaters. Our intention would be to install these heaters on the tanks that we intend to fly.
But, again, if anything occurred during this testing that came out that said we need to do further work or something like that, we may look at some of these other mitigations to see if they were sufficient. There’s analysis going on and testing going on to look at other mitigating ways to get rid of this ice. The heater is the one we think is the best option, but it doesn’t–but we do have a backup plan and an alternate to the backup.
And so we’re going to do the analysis and the rigor to see what those concepts do as we work through the final testing of the heater modification.
I have, again, some confidence in the fact that this heater will work, and Wayne is just trying to lay out the fact that if at any point in that process we found something that caused us to change direction, we will change direction and do the right thing and make sure we cause no harm.
QUESTIONER: Also, this is about the first time in 15 years that we haven’t had a [inaudible] manager-type sitting in the seat of the Administrator. Now we have an Administrator up there who’s got a whole drawer full of degrees, one of the most experienced people in the background, in the science of your missions. Did he play any part in this decision? Is he coming out a hands-on guy? What did Administrator Griffin do?
MR. : Mike attended our debris verification review, and he was–he sat in the back and participated some. The fact is, though, he offered some observations. He was learning as much as he could, like he said earlier today. I don’t–I don’t think that any one comment he made would have changed the direction of what we were learning and what the community would have–the conclusions this community would have come to.
But, again, as you said, he is one of the more knowledgeable NASA Administrators we’ve had since I’ve been with the agency when it comes to the engineering and the different things that we do. And so his insights and his observations are taken very, very seriously, as well as all other NASA Administrators. But the fact is with his technical background, he offered some good insight, and we accepted that and, you know, took that along with all the other input that we were getting from all the people that were at the debris verification review.
So, again, I can’t say that he influenced this. I think that we were headed in this direction with the findings that we had. But I do think that he participated and was learning along the way what we were finding.
MR. : Thank you, Bill.
QUESTIONER: Todd Halverson (ph) of Florida Today for either Bill Parsons or Wayne Hale. Given the uncertainties and the troubleshooting you still have ahead, I’m wondering how confident you guys are that you could, in fact, make the July window?
MR. PARSONS: Until I see the troubleshooting plan for the things that we have to do out at the pad, I probably need to reserve a little bit of my overconfidence about making July. If all we had to do was some of the analysis work that we have laid out–I’ve seen the schedule for that, and we’ve got plenty of time to do that and do it in the manner and the rigor that we need to go do it, and we even have some contingency in that in getting to the July time frame, so that makes me feel very, very good.
But until I understand what we have to do to clear the engine cutoff sensors and to understand this repress issue, it would be difficult for me to say that something wouldn’t come up during that troubleshooting or something, some work that we have to go do that would not allow us to make the July window.
Let’s say all that clears up the way we anticipate it to and that we were able to solve those issues and move on in a fairly rapid manner, then July is easy to make. We were processing along the way, and we were getting towards– from a processing standpoint and a hardware standpoint, we were very close to the May-June window. From an analysis standpoint and now this additional work in the LOX fuel line bellows area, that’s moved us. And if that’s all we had to do, July would be very makeable. But we need to hear the troubleshooting plan for what we’ve got from the external tanking test.
Wayne, I don’t know, do you–
MR. HALE: I would just add that, you know, when we had the low-level sensor phenomenon during the tanking test, we recognized that as a problem that we had to go fix. The pre-press or the pressurization problem that occurred during the tanking test, frankly, again, I didn’t think that was a big concern at the time. And when we talked, you know, the evening of the tanking test, I didn’t think that was a big concern.
However, the engineers that do the analysis have come back and said, you know, this is something we need to figure out, this is important and we need to troubleshoot it. And that has been the result over the last couple of weeks.
So we’ve got to figure that out. It’s just a fact of going to fly. We wouldn’t want to fly the vehicle until we did figure out, and it’ll take the time that it takes.
MR. : You know, that–the number of cycles, we’re at the upper level of the launch commit criteria. So, I mean, it was well within our–it was not well within our spec. It was the upper limit of our spec. But when we went back and looked, it was not normal. That’s not normally what we have. So there was something going on, and when they did their review, they decided that we need to go understand this much better than we do at this particular time.
QUESTIONER: And I’m wondering, is the plan now to try to launch STS-121 during September? And my understanding is that the Soyuz launch in September effectively leaves you with about a five-day window, and I guess for Gerst, are your Russian partners willing to move that launch out? And if so, how many days can you buy back?
MR. GERSTENMAIER: We talked to them today, and they’re well aware what we can do in terms of launch window to help there, and they’re willing to do what we need to go do. We’ll make a formal request once we understand things a little bit better. But I think we can get a couple weeks, two weeks or so, if we need to go ahead and move to the right, maybe 11 days or so, and that will give us the full lighted window.
So I think we’ll have those discussions with them at the right time, but they sure were supportive today to help with the overall launch sequence. Again, the partners are willing to help wherever they can in any way they can to get the shuttle back to flight.
QUESTIONER: David Waters (ph) from Central Florida News 13. Tell us from whichever of you, either Wayne or Bill Parsons, talked to the crew there, and how have they been informed about the process. Obviously you folks are the ones making the decisions, but what have they said about this and what do they feel about this?
MR. : Let’s see. We had the crew–by happenstance, we had previously scheduled to meet with the crew, the STS-114 crew, yesterday afternoon, and at the wind-up time of our telecon with NASA headquarters, and they felt very good about it. They have been very encouraging all along that we need to do a good, thorough job to make sure their vehicle is safe to fly. I think Soichi had the key comment of the day when he said, we’ll we got four days closer to launch this time than we did last time, which is to say back in 2003.
So they’re anxious to go. They were excited about going down to KSC, coming your way to KSC to do the terminal countdown demonstration test, which is going on there next week. And they’re happy to use the time productively for some more training and other exercises.
MR. : And we would have loved to have been able to tell them this news, but unfortunately it had already been written about. And so they had already heard about it when they got there and were talking with us.
QUESTIONER: Kevin (?) with WFTV. I was just wondering, with the modifications that you’re talking about with the tank, are you going to do another tanking test?
MR. : Well, currently another tanking test (?) like we did before is not in the plan. But if the troubleshooting plan says that we need to go do some tanking of the hydrogen tank or do a full up-tanking test, then that’s what we’ll do. We need to wait and see what the troubleshooting plan is, and again, if that’s part of it, then that’s–then we’ll plan that.
QUESTIONER: This is Mike Cabidge (ph) with the Orlando Sentinel with one last question for Bill or Wayne. What is the latest on the blankets with the hydraulics fluid spill? Now that you have an opportunity to go back, are you going to swap all of those out? Are you going to do that at the pad? What’s your plan to deal with that?
MR. : First of all, I’ve talked to Steve Polis (ph), the orbiter project manager, and he’s going to put together his recommendation probably Monday or Tuesday and bring it to the program. He’s given us some preliminary results. The first thing is that the Kennedy Space Center can do it at the pad. They would prefer not to. And so that’s the first thing, is the conditions, the access, and other things. It’s doable, but it’s not the best conditions, and so that they would prefer not to do it out there. So that’s one piece of information.
The second thing is we’ve taken some samples and the hydraulic oil in the blankets is not nearly as bad as we thought initially. And so some of the testing that we did out at Huntington Beach to understand what problems this would cause with some surface coating of hydraulic oil, we had tested things that maybe were much worse than what we currently have on the vehicle. And that means we would have had to change the blankets out.
But with this new information, with some plugs that we’ve taken out of the blankets and things like that, it may very well be okay to leave the blankets in place.
But, again, we need to let these guys work their way through this. There’s other options to clean these blankets and do other things that they may very well bring forward to us next week. And so if they do say to change the blankets out, I think we’ll probably do that in the vehicle assembly building when we roll back. But they very well may say that they’re good to fly as they are or with some cleaning or some other things that we might be able to do to them.
MS. : We have a few more minutes for a couple of follow-ups that we’ll catch real quick.
QUESTIONER: Mark Carreau from the Houston Chronicle. I had a couple things.
One, I wanted to follow up on Bill Harwood’s question about the ice. Do you guys have a mass estimate for that, even something close?
And the second thing, in going back over this foundation of notes that I’ve taken this month as you’ve briefed, you also mentioned that the preparations for Atlantis were rather close, and I wondered if that may have factors into any of this at all, or did you have the backup mission where you wanted it?
MR. : Let me answer the Atlantic question first. Atlantic processing is going very well. All the lessons learned from, you know, when we processed Discovery was rudder speed brakes. And everything else had been incorporated, the main landing gear door cycles, nose landing gear door cycles and things like that, things that were kind of pacing items along the way for Discovery had been incorporated, and we’ve made great progress. Kennedy Space Center has just done a great job getting Atlantis ready. They’re a little behind, a couple days, maybe a week, but overall that would have fit well into our capability. After we moved the launch date to the 22nd, that really gave them a little bit of relief.
And so, no, that didn’t really play into the equation at all. Atlantis was going to be ready, and it’s currently still on track to meet the rollover dates as they are stated now with probably some delays that will occur, three or four days, five days, something like that. So it’s not a huge impact at all.
What was the first part of the question?
MR. : The mass [inaudible].
MR. : Here’s the thought problem, Mark. I’m not good at math so I’ll give it to you. It’s 57 pounds per cubic foot. It’s five inches by two inches by two inches. So anybody ought to be able to do the math, except I’m not going to do it in my head right now. The guys know the number. We can get it to you.
QUESTIONER: [inaudible] less than a half pound or a pound or–
MR. : A very small piece of ice can cause some problems, and I couldn’t give you a complete size. I would say, though, ice does not liberate the same way as foam. We understand the physics behind foam liberation much, much better and what causes foam to come off and what the pop-off velocities will be and how it will enter the air stream and then do the things that it does, because we’ve done an awful lot of testing.
We don’t understand as much about what’s, you know, the mechanism that causes ice to come off and when will it come off and how it holds onto the foam and things like that. We don’t understand that as well. And then it doesn’t have the same lift characteristics as a divot. And so the transport analysis in that says, well, in most cases we believe that it doesn’t have a transport mechanism to get back to the vehicle. But that’s some of the wind tunnel testing that we need to understand a little bit better and which sizes and if it comes off of the fuel line bellows in a five-inch piece like Wayne described or if it breaks up in smaller pieces, exactly what that will do and what the characteristics of that will be.
MR. : We will get you the number.
MR. : There’s a number. I just don’t have it on the top of my head.
MS. KLEM: : Okay. I think that will conclude our briefing for today.
A couple of programming notes. We will start replaying today’s briefings at the top of the hour on NASA Television, and then as Wayne mentioned, the internal countdown demonstration test is scheduled for next week. There are various opportunities for the media associated with those activities. So just a couple of notes.
The crewmembers will be arriving at the Shuttle Landing Facility on Sunday night, and there will be a photo opportunity, so get in touch with the Kennedy Space Center prep flight. And then also on Tuesday, there will be a Q&A opportunity. So if you’re interested in those, contact KSC.
Thank you.
[Whereupon, the briefing was concluded.]