Statement: Steven Lindsey, Sierra Nevada: NASA’s Commercial Crew Development Program: Accomplishments & Challenges
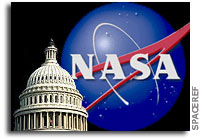
[Note: OCR from a PDF document – original here]
Hearing on NASA’s Commercial Crew Development Program: Accomplishments and Challenges
U.S. House of Representatives Committee on Science, Space, and Technology
Rayburn House Office Building Room 2318
Steven W. Lindsey, Colonel, USAF (ret.) Director, Flight Operations, Sierra Nevada Corporation Former Chief, NASA Astronaut Office Pilot, STS-87 & STS-95; Commander, STS-104, STS-121 & STS-133
Thank you, Chairman Hall, Ranking Member Johnson and Members of the Committee for this opportunity to present Sierra Nevada’s perspective on the Commercial Crew Program.
Sierra Nevada Corporation (SNC)
Before addressing the questions you asked in your invitation letter directly, I’d like to provide you with a brief description of Sierra Nevada Corporation to indirectly answer how the depth and breadth of our company provide us with the capabilities necessary to develop a human-rated spacecraft for our Nation. Sierra Nevada Corporation (SNC) is a proven systems integrator, electronic systems and space systems provider with a reputation for rapid, innovative, and agile technology solutions. As a 100% U.S., privately held, woman-owned and operated business, SNC has been under the current ownership since 1993. It employs a highly talented staff of over 2,200 people, mostly engineers, scientists, or technical personnel. Our seven business areas have operations in 20 states. SNC has a very solid financial foundation and an uninterrupted profitable growth history with no long-term debt. SNC’s strong financial track record and stable leadership structure are a key element in the successful yearly execution of hundreds of government contracts. SNC holds one of the highest possible Dunn & Bradstreet rating scores.
Sierra Nevada Corporation is currently in our sixth year of development of a human-rated spacecraft called the Dream Chaser Space System. The SNC team has invested a substantial amount of capital, engineering, time and effort to develop the technologies that support our Dream Chaser spacecraft. These technologies and expertise include hybrid propulsion systems, complex composite structures, airframe design, spacecraft components, adapter rings, navigation and control, life support, and integrated system design and testing capabilities. This previous work and our continuing NASA partnership will significantly lower development time and risk, and will help to ensure program success.
SNC has also assembled a world-class team of spaceflight experienced partners to execute the Dream Chaser Space System program. Boeing Experimental Systems Group has great expertise in lifting body spacecraft including analysis, avionics, Guidance, Navigation, and Control software, and flight control. Their recent X-37 spacecraft experience fits perfectly with our Dream Chaser development and risk reduction activities. United Launch Alliance (ULA) has been on our team for more than 5 years; jointly collaborating on an integrated launch vehicle that rapidly brings a safe, reliable, and cost-effective commercial Crew Transportation System to the Low Earth Orbit market. ULA is assisting SNC with integrated aerodynamics and risk retirement. Aerojet, a propulsion leader, is developing the main Reaction Control System. Draper Lab, with unparalleled GN&C experience, is leading orbital Guidance Navigation &Control development. NASA’s Langley Research Center adds expertise in HL-20 analysis and modeling, while NASA’s Dryden Flight Research Center adds flight test expertise for our extensive flight test program. In fact, we are using the expertise from seven NASA Centers to ensure we are building the best spacecraft possible. AdamWorks is assisting SNC in structural fabrication using our combined composite manufacturing capabilities. The University of Colorado is applying young minds to conduct displays and controls layout and evaluations and refine the integrated system Human Rating Plan, with assistance from Special Aerospace Services. United Space Alliance is using their extensive Space Shuttle experience to provide operations and software development support. SNC and Virgin Galactic are working together to plan for global marketing, sales, and commercial operation of the orbital Dream Chaser. In addition to coordinating and managing the team, SNC manages all internal systems, propulsion, structure, Launch Vehicle integration, and systems engineering. This superb team of experienced space companies allows us to use heritage hardware and software to rapidly develop our space system and provide a cost effective and safe way to transport people to and from low Earth orbit.
Dream Chaser Space System
Our primary Dream Chaser Space System goals are to safely, reliably, and cost effectively transport crew to the International Space Station and return to a hard surface runway. The heritage Dream Chaser design evolved from the NASA Langley Research Center’s HL-20, which was originally derived from the Russian BOR-4 orbital test vehicle that flew 4 orbital flights. Langley performed more than 1,200 wind tunnel tests, wrote 60 journal papers and NASA contractor reports, and performed thousands of piloted simulations in its decade-long investment refining HL-20 aerodynamics, performance, and controls. To take advantage of the orbital flight and wind tunnel heritage, SNC retained the HL-20 design center of gravity limits and outer mold line, but made significant upgrades in composite structures so as to take advantage of modern construction techniques and materials and we incorporated a new safer, more operable, flexible propulsion capability. Bottomline, SNC consolidated the fragmented HL- 20 aerodynamic data, filled in the database gaps with significant additional analysis, and have designed a very sophisticated reusable space plane that can satisfy NASA’s low Earth orbit needs.
The Dream Chaser vehicle features a reusable, piloted lifting body design capable of transporting two to seven persons and pressurized cargo. Dream Chaser orbital missions are launched on an extremely reliable Atlas V 402 booster rocket and return to land on a conventional runway. The baseline launch site is Kennedy Space Center and the baseline landing site is the Shuttle Landing Facility. But, The Dream Chaser is designed to be able to reach and land on any 10,000 foot hard surface runway for any nominal or abort landing. The DC is almost entirely reusable, with exception of some propulsion system components and the chemical batteries. Post-flight Dream Chaser spacecraft refurbishment and launch processing will occur at the Kennedy Space Center prior to re-flight certification.
The Dream Chaser spacecraft has the capability for launch pad abort and intact ascent aborts from any point on its trajectory to hard surface runways. The Dream Chaser spacecraft’s > 1,100 nautical mile cross-range capability is significantly better than the typical capsule cross range. Every-orbit deorbit to runway landing capability exists for emergencies and there is sufficient cross range to accommodate multiple daily Continental U.S. runway landing opportunities. Low 1.5 g entry loads are considerably less than those experienced by capsules during reentry which allows Dream Chaser to have large down-mass capability for g-sensitive science experiments and touchdown shock is far lower than capsule loads which can be as high as 15 g’s for water landing (e.g., Apollo 12 and 15). These reduced loads lessen the possibility that a vehicle will require post-mission repair for re-flight. Runway landings avoid expensive ship-based recovery and salt water exposure.
We selected the reliable Atlas V launch vehicle specifically for its heritage, demonstrated reliability, ability to human rate, and compatibility with the DC spacecraft. This Nation has launched multi-billion dollar national assets on the Atlas due to its reliability. The Atlas has demonstrated 98 consecutive successes since 1993, including a 100% mission success record for all Atlas II, III, and V flights, with all spacecraft reaching proper orbit.
After nominal orbital insertion, Dream Chaser is reconfigured for orbital operations to support crew Flight Day 2 rendezvous and docking. Orbit adjust is performed using the SNC-developed on-board hybrid rocket motors and reaction control system. The hybrid motors are improved versions of the successful SNC developed SpaceShipOne rocket motors. This technology is also being used on the SpaceShipTwo program resulting in extensive flight heritage and experience before our first orbital flight. The DC is designed for 3.5 days of on-orbit loiter without ISS docking. The DC is designed to dock to the NASA Docking System (NDS) located at appropriate ISS docking locations.
The DC provides assured crew return capability while docked to the ISS. DC can remain docked to ISS for extended periods (up to 210 days, assuming the DC shares ISS cabin atmosphere while docked and receives ISS power transfer to support battery trickle charge).
Dream Chaser Space System Accomplishments to Date
The following milestones were completed from December 2009 to September 2010 during the Commercial Crew Development Program, Phase 1 contract (CCDev1):
Milestone 1: Program Implementation Plan Delivered. This included management planning for design, development, testing, and evaluation supplier engagement, risks and anticipated mitigations.
Milestone 2: Space Vehicle Manufacturing Review of Aeroshell Tooling. This included manufacturing the aeroshell tooling, a review of the aeroshell design, manufacturing plans, and readiness to begin fabrication of the Dream Chaser’s aeroshell.
Milestone 3: Space Vehicle Prime Motor Manufacture and Multiple Restart Firings. This milestone include manufacture of and ground based motor firings of a single hybrid motor with 3 restartable firings for a minimum duration of 5 seconds for each firing, including one firing in a vacuum condition.
Milestone 4: Space Vehicle Primary Structure Testing. In this milestone the Dream Chaser’s primary structure was designed, fabricated, assembled, and tested to support landing gear and hybrid motor thrust loads.
All milestones were completed on time and under budget.
In addition to these milestones, The Dream Chaser spacecraft went through extensive aerodynamic, thermal protection system, guidance, navigation, and control system analysis. We completed development of our desktop simulator, completed extensive systems engineering, developed a risk management plan, a human rating plan, and significant program documentation to support further Dream Chaser development.
Since we finished our four milestones under budget during CCDev1 and because of our commitment to the success of this program, we added multiple unfunded milestones. We designed, developed, and successfully flight tested a scale model of the Dream Chaser spacecraft, dropped from over 14,000 feet at the NASA Dryden Flight Research Center. This flight test signaled the beginning of the atmospheric test program for the Dream Chaser vehicle. We also developed our first simulator to begin engineering development simulations, and built several mockups to use for engineering development.
We are currently six months into the CCDev Phase 2 contract (CCDev2). The following milestones have been completed (or are about to be) in the CCDev2 program:
Milestone 1: System Requirements Review. Presented a briefing and plan of the overall system requirements for the Dream Chaser Space System.
Milestone 2: Canted Airfoil Fin Selection. Complete wind tunnel tests and Computational Fluid Dynamics analysis on candidate airfoil fin outer mold line and select final fin shape to ensure proper aerodynamic performance of fins.
Milestone 3: Cockpit Based Flight Simulator. Complete fabrication and assembly of cockpit structure, install simulator designs and controls, and conduct a Simulator Readiness Review to verify readiness for engineering and pilot evaluations.
Milestone 4: Vehicle Avionics Integration Laboratory (VAIL). Design, manufacture, and integrate the VAIL to support testing, verification, and validation of Dream Chaser avionics and software.
Once again, all completed milestones were finished on schedule and under budget, with remaining funds being re-invested to accomplish additional work to accelerate our program.
Remaining Milestones in CCDev2 and road to Critical Design Review
Milestone 5: System Definition Review. Conduct Dream Chaser System Definition Review, which completes the first design cycle of the Dream Chaser Space System architecture and design. This milestone will be completed on Oct 27, 2011 – on schedule.
Milestone 6: Flight Control Integration Laboratory. Design, manufacture, and integrate the flight control integration laboratory to begin developmental engineering tests of flight control actuators and surfaces. Complete test hardware such that it is ready to support Engineering Test Article flight control tests. This milestone will be completed on Nov 17, 2011 – on schedule. Milestone 7: Engineering Test Article (ETA) Structure Delivery. Complete assembly and deliver the ETA primary structure for start of systems integration and installation of secondary structures. Scheduled for completion in Dec 2011.
Milestone 8: Separation System Test. Complete design and construction of the prototype Dream Chaser separation system and demonstrate activation to validate concept and verify performance of the separation system. Scheduled for completion in Feb 2012.
Milestone 9: Preliminary Design Review. Conduct Preliminary Design Review of the Dream Chaser Space System. This review will complete the second design cycle of Dream Chaser Space System. Scheduled for completion in May 2012.
Milestone 10: Captive Carry Interface and ETA Landing Gear Drop Tests. Complete fabrication of the ETA captive carry prototype mechanism and perform release test to verify performance of system to ensure readiness for captive carry. Perform drop test of ETA landing
gear to evaluate landing gear dynamic limit loads and landing load attenuation capability to ensure adequate performance of landing gear. Scheduled for completion in Jan 2012.
Milestone 11: ETA Captive Carry Flight Test Readiness Review. Complete Captive Carry Flight Test Readiness Review to verify ETA readiness for captive carry testing. Scheduled for completion in March 2012.
Milestone 12: ETA Captive Carry Flight Test. Conduct ETA captive carry flight test on carrier aircraft to characterize integrated vehicle performance. Schedule for completion in April 2012
Milestone 13. ETA Free Flight Test. Conduct unpiloted ETA Free Flight Test from carrier aircraft to characterize handling qualities and approach and landing. Scheduled for completion in July 2012.
At the completion of the Preliminary Design Review in May of 2012, the Dream Chaser team will begin Design Cycle 3, which will culminate in our CDR (Critical Design review) in the mid to late 2013 timeframe. During this design cycle, all systems will be matured through design, analysis, building of flight-like hardware and extensive testing – culminating in subsystem CDRs to support the overall system CDR. We will build a Structural Test Article for further loads testing, and continue test flights, both unpiloted and piloted in the Engineering Test Article. Additionally, we will build our Suborbital Vehicle and complete powered flight tests to validate and verify Guidance, Navigation, and Control in the low supersonic region. The Suborbital Vehicle flight test program will conclude with a Pad Abort test to runway landing.
NASA’s Commercial Crew Program: Procurement Strategy Challenges
A common question often asked about NASA’s commercial crew program is “How can commercial companies build and provide spacecraft for crew transportation in and out of low earth orbit?” The answer to this question is that commercial companies have been doing this for the past 50 years. Every single United States human-rated spacecraft has been built by a commercial company. Companies such as McDonnell Aircraft Company, prime contractor of the Mercury capsule, to Rockwell International, builder of the Space Shuttle orbiter, to current companies like Sierra Nevada which are today developing new crewed spacecraft. Other spacecraft developed in the future for beyond earth orbit missions will also be built by commercial companies.
So what’s different about what we are doing when compared to previous human-rated spacecraft programs? There are two primary differences – the procurement mechanism, and how NASA and our companies interact. Under the current Commercial Crew Development program, the contractual mechanism is the Space Act Agreement – a fixed price, pay for performance, milestone based program. Space Act Agreements are easy to implement, easy to change, and easy to terminate. If companies don’t stay on schedule or milestones aren’t met, then companies aren’t paid. Companies are also expected to contribute financially to the program. Losses to the
government for a non-performing company can by minimized through the use of milestone- based payments, and cost overruns are simply not possible. The next phase of the Commercial Crew Program is planned to be a FAR based contract that will retain many of the good things about SAAs, including fixed-price and milestone-based payments. These types of contracting mechanisms are a cost effective way for the government to retire technology development risk and mature an integrated design.
Interaction between NASA and Sierra Nevada on our Space Act Agreements has evolved into a very unique partnership. Typical government interaction with commercial companies building spacecraft involves providing guidance, receiving insight into our design, and having oversight over our requirements. Guidance has been provided to us by NASA in the form of spacecraft system requirements and specifications, just as in traditional contracting approaches. We are required, in the end, to meet those requirements and specifications or NASA simply won’t contract for our services. To accomplish the insight function, NASA has embedded a ‘Partner Integration Team’ of human spaceflight experts directly into our company to provide a true inside view of our day-to-day operations. They share offices with us and attend all of our meetings, allowing complete government insight into the development work we are doing. This has the dual advantage of removing many of the burdensome day-to-day reporting requirements, while at the same time providing our team with valuable government advisors and consultants as we work together to build a new spacecraft.
Insight versus Oversight
In the next phase of the Commercial Crew Development Program, the proposed contracting mechanism is a firm fixed price Federal Acquisition Regulations-based contract. While the complexities of this type of contract will be much greater than the current Space Act Agreement milestone-based contract, the insight and oversight model shouldn’t change significantly for Sierra Nevada. During the current CCDev2 contract, we have allowed complete NASA insight into our day to day operations. NASA technical experts are embedded within all of our design, development, and test teams – providing both expert advice to us as well as critical insight to NASA’s Commercial Crew Program. This approach has proved to be very effective – requiring less oversight due to the extraordinary level of insight.
The challenge with this next phase of the program will be to balance oversight versus insight. For example, NASA should provide oversight and direction in all cases where they see a need to improve the safety of a spacecraft being developed for their use. However, that does not mean that every technical change suggested by the government should be accepted. If a change makes the design ‘better’ but doesn’t impact safety, then the commercial company must have the leeway to accept or reject the change, based on technical, cost, and/or schedule considerations. This is where the partnership between NASA and a commercial company that is truly responsible for the technical design of a crewed spacecraft can make a huge difference – keeping costs and schedule under control while at the same time developing the safest spacecraft possible for the defined mission.
The future Low Earth Orbit commercial market
The SNC business case is strong. We have performed multiple internal and external market research studies during our 6-year Dream Chaser program. We are developing multiple potential markets for our Crew Transportation System, many of which are best serviced by a lifting body such as ours. These markets are human transportation, critical cargo transportation, orbital servicing, and orbital sensor and testbed operations. Five primary client groups include: NASA and other civil agencies, commercial space corporations, military agencies, international markets, and tourism. NASA and crew transportation to ISS will be the anchor tenant for Dream Chaser, but after an early start-up period will not be the major revenue provider. SNC, through its expanding operations expects to place hundreds of satellites in orbit during the next few years and will become its own servicing client. All of our markets are expected to grow substantially and are not limited in time. SNC will develop a number of Dream Chaser vehicles from the same platform, similar to an airplane platform like the 747 or C-130, with each variant optimized for the specific mission. Virgin Galactic recognizes the market for the DC and they have joined our team to begin marketing and sales of orbital human transportation services.
A key advantage of the Dream Chaser is the ability to land on a runway, allowing for many viable orbital and suborbital missions to be accomplished. The spacecraft has substantial pressurized cargo down-mass capability with low g reentry and runway landing at many landing sites. It can be adapted from a full seven-person crew to two crew members with increased cargo capacity to fully autonomous operations. It is also scarred for potential future servicing Extra Vehicular Activity capability and robotic manipulator use. Our low stress runway landings will allow us to carry the greatest range of passengers, and provide researchers with the best possible path for maintaining the integrity of their experiments through a low-g return and quick access to science samples. Our non-toxic propellants and runway landing capability allow us to land at domestic and international locations without special services. We are currently refining our business model to capture variables such as market share, seat price, and launch vehicle price while considering parameters such as turnaround time and fleet size. This will allow evaluating the sensitivity to market and technical factors.
We have a dedicated business development team who sell SNC space services and products around the world. This team has relationships with future customers who we periodically brief on our Dream Chaser progress, receiving in return information on their needs and future missions. Our relationship with Virgin Galactic will allow utilization of its existing marketing infrastructure for the SpaceShipTwo program to rapidly develop critical non-NASA global markets for the Dream Chaser Space System.