Statement: Elon Musk, SpaceX: NASA’s Commercial Crew Development Program: Accomplishments & Challenges
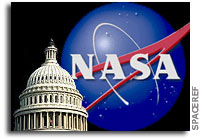
[Note: OCR from a PDF document – original here]
Statement of Elon Musk CEO & CTO Space Exploration Technologies Corp. (SpaceX)
before the House Committee on Science, Space and Technology U. S. House of Representatives
October 26, 2011
Chairman Hall, Ranking Member Johnson and Members of the Committee,
On behalf of Space Exploration Technologies (SpaceX) and our more than 1,500 employees across the United States, thank you for the opportunity to participate in today’s hearing.
I also want to thank you and the members of the Committee for your continued support of NASA and America’s space exploration programs. The goals of this agency, unlike nearly any other, are focused on advancing the state of human knowledge and human achievement. Even as we face tough fiscal challenges as a Nation, NASA and the cause of space exploration deserve support, particularly through efficient investments and public-private partnerships that provide best value for the taxpayer.
America’s endeavors in space are truly inspirational. I deeply believe that human spaceflight is one of the great achievements of humankind. Although NASA only sent a handful of people to the moon, it felt like we all went. We vicariously shared in the adventure and achievement. My goal, and the goal of SpaceX, is to help create the technology so that more can share in that great adventure.
With your support and NASA’s invaluable partnership through the Commercial Orbital Transportation Services (COTS) program, SpaceX made history last year as the first commercial company to successfully recover a spacecraft from Earth orbit. The inaugural flight of the SpaceX Dragon confirmed what we have always believed – the responsiveness and ingenuity of the private sector, combined with the U.S. government’s investment and technical support, can deliver an American spaceflight program that is safe, achievable, sustainable and affordable.
SpaceX is honored to continue our partnership with NASA as we work together to develop commercial crew capabilities. Our goal is to develop the safest, most reliable and affordable crew transportation system to low Earth orbit and, ultimately, beyond. Indeed, carrying humans into space has been a cornerstone of SpaceX’s vehicle designs from the day the company was founded. There is no more critical and precious responsibility than having the opportunity and privilege to transport the true heroes of America’s astronaut corps into space and, in the event of a mishap or failure, providing them with an effective, life-saving abort capability. This awesome responsibility informs and shapes SpaceX’s every design, decision and operation.
Mr. Chairman, the United States needs safe and affordable domestic systems for transporting American astronauts into space. Most pressing is the need to restore our ability to carry crew to the International Space Station (ISS) for which the country has spent so much effort, sweat and national treasure. The ISS’s research and scientific potential is constrained by the current inability to achieve a full complement of astronauts on board. Sole reliance on the Russian Soyuz is not a remedy.
With our NASA colleagues, SpaceX is working hard to deliver a solution. I am pleased to provide the Committee with an update on SpaceX’s human spaceflight advances to date and challenges ahead as we progress toward the capability to transport human beings into space aboard the Falcon launch vehicles and Dragon spacecraft.
I. Commercial Cargo Efforts Leading to Crew Carriage
In 2006, SpaceX partnered with NASA under the Commercial Orbital Transportation Services (COTS) program. The COTS program was the first of its kind for NASA: a “pay for performance” partnership between the government and private business to rapidly design and prototype critical technologies. NASA structured the COTS program as a collaborative venture with commercial space companies – sharing the risks, costs and rewards of developing new space transportation capabilities. That “experiment” resulted in the first U.S. launch vehicle developed since Saturn with engine out reliability. As demonstration of its reliability, this launcher flew successfully for its first two missions. This reliable launcher is also the only U.S. launch vehicle that is competitive in the international marketplace and will help bring launch dominance back to the U.S. This experiment also resulted in a reusable spacecraft that will service our critical national asset – the ISS.
One of the central tenets of the COTS program is that public-private partnerships leverage private capital to supplement government dollars, yielding products and services more cost- effectively and more rapidly. In pursuing its mission to create “new commercial space transportation systems and demonstrate capabilities to provide cost-effective transportation services to orbit,” NASA’s COTS office granted its partners “latitude to freely innovate and optimize their launch vehicle and spacecraft designs and operations.”1
1 NASA COTS video, www.nasa.gov
2 NASA independently verified SpaceX’s total development costs of both the Falcon 1 and Falcon 9 at approximately $390 million in the aggregate ($300 million for Falcon 9; $90 million for Falcon 1). NASA, Falcon 9 Launch Vehicle NAFCOM Cost Estimates, August 2011.
That latitude fostered SpaceX’s ability to focus on safe, simple, proven designs that are cost- effective. As a result, SpaceX developed the Falcon 9 rocket for a fraction of the cost NASA would have paid under a traditional acquisition model. NASA’s internal studies using the NASA-Air Force Cost Model (NAFCOM) concluded that it would have cost NASA $1.7B to $4B to develop the Falcon 9 rocket. By contrast, in partnership with NASA’s COTS program, SpaceX developed the Falcon 9 for approximately $300M.2 It bears noting that the Falcon 9’s development included designing, building and testing SpaceX’s Merlin engine, the first new all- American hydrocarbon engine for an orbital booster in forty years.
Likewise, SpaceX developed the Dragon spacecraft – a free-flying, reusable spacecraft – from a clean sheet of paper to the first demonstration flight in just over four years for about $300 million.
a. SpaceX’s COTS Flight Success and Upcoming Launch
In June of last year, SpaceX performed a successful demonstration launch of the Falcon 9 on its maiden voyage. Then, on December 8, 2010, SpaceX successfully launched the Falcon 9 with the Dragon spacecraft, becoming the first commercial company in history to launch, reenter and successfully recover a spacecraft from Earth orbit. SpaceX’s COTS demonstration mission blasted off from Launch Complex 40 at Cape Canaveral. The Falcon 9 lofted the Dragon to orbit where it twice circled the Earth and then reentered the Earth’s atmosphere, splashing down safely in the Pacific Ocean. Until late last year, launching, orbiting, reentering and recovering a spacecraft was a feat previously performed by only six nations or government agencies: the United States, Russia, China, Japan, India and the European Space Agency. NASA’s expert advice and mentorship throughout the development process helped SpaceX build upon 50 years of U.S. space achievements to reach this goal.
In preparation for the next COTS demonstration mission, which is set to occur in the next few months, the Dragon spacecraft design has been upgraded to meet all requirements for ferrying cargo to and from the ISS, including the proximity operations sensors to guide the vehicle safely near the ISS. This mission will be an extended mission to the ISS, lasting more than three weeks. Consequently, two solar array wings have been added to the Dragon trunk to enable positive power generation throughout the flight. Additionally, a redundant active thermal control system loop has been installed in the Dragon trunk to reject excess heat into space; protect the spacecraft from excessively hot or cold temperatures; and provide an environment inside the spacecraft that is acceptable for cargo and for the ISS crew when berthed to station.
In accordance with our COTS milestones, a series of tests have been conducted on the fully integrated Dragon spacecraft, including a 12-day thermal vacuum test during which, the entire avionics system was exercised while flowing telemetry 24/7. (No notable issues were uncovered and the thermal data matched model predictions closely.)
Dragon’s proximity sensors are critical for the ISS approach and have been put through extensive performance testing in open loop and closed loop simulation using flight hardware and software. Significant testing emphasis has also been placed on the new Dragon mechanisms, which have all completed qualification testing. These mechanisms include the forward hatch, solar arrays, guidance, navigation and controls (GNC) bay door that exposes the Flight Releasable Grapple Fixture (FRGF) and a claw that provides electrical and data connections between the capsule and trunk.
Several joint SpaceX-NASA tests have been completed, including the Passive Common Berthing Mechanism (PCBM) testing and cabin acoustic noise verification. Most recently, the vehicle completed radiation testing of all avionics components and an Electromagnetic Interference (EMI) test in keeping with NASA requirements.
We are rapidly progressing toward the next COTS demonstration flight and are still engaged with NASA to finalize vehicle verifications and the mission plan. This next COTS mission represents a huge milestone not only for SpaceX, but also for NASA, the U.S. space program and American free enterprise. When the astronauts stationed on the ISS open the hatch and enter the Dragon spacecraft for the first time, it will mark the beginning of a new era in space travel.
b. Commonality between Cargo Falcon 9/Dragon and Crew Falcon 9/Dragon
SpaceX conceived the Falcon 9 and Dragon with crew carriage in mind and undertook designs from inception to meet human certification requirements, including increased structural factors of safety, triple-redundant avionics, trajectories with acceleration limits within human safety limits, and many others. Because SpaceX planned for the current cargo Dragon to evolve into a crew version, many of the Dragon’s systems are identical in the cargo and crew versions. In fact, Dragon was designed to meet NASA’s human engineering safety requirements in SSP 50808 because the cargo Dragon will fly in close proximity to the ISS, berth with the ISS and support on-orbit crew habitation during cargo transfer operations.
Designed to be as safe as possible from a clean sheet in 2005, the Dragon crew transportation system takes advantage of 21st century technology advances and lessons learned throughout the history of human spaceflight. The Dragon spacecraft is comprised of three main elements: the Nosecone, which protects the vessel and the docking adaptor during ascent; the Spacecraft, which houses the crew and/or pressurized cargo as well as the service section containing avionics, the Reaction Control System (RCS), parachutes and other support infrastructure; and the Trunk, which provides for the stowage of unpressurized cargo and will support Dragon’s solar arrays and thermal radiators.
As a result of the commonality between the cargo and crew versions of Dragon, many of the critical components of the Dragon crew transportation system are already operational and flight- proven. Other systems for crew accommodation require some development, but the only major development is for the launch abort system. This commonality enables SpaceX to plan for crew demonstration flights in 2014, with a rapid transition to operational capability.
c. Lessons Learned from the COTS Program Model
The NASA-SpaceX COTS partnership has successfully enabled and promoted genuine innovation while maintaining safety and reliability standards. The COTS program helped guide the development of Dragon and Falcon 9 to pass a set of specific requirements and verifications required for any ISS visiting vehicle, but left the design and aspects of analysis and testing largely to the contractor. This allowed for rapid prototyping and design iterations in which components could be designed, tested, modified and retested, often times in a matter of hours. And NASA could be confident in the final design because all design and test data were available for review. Also critical for innovation was the fact that decisions about “how to meet the requirements” were generally left to the contractor. Rather the critical metric was that the requirement was clearly met. I note here that specificity as to how to meet requirements is inherently prescriptive and often results in less innovation.
Safety and reliability standards have been maintained through insight into the entire system design and insight and oversight into safety critical systems. Systems that interface with the ISS are thoroughly reviewed by independent contractors, NASA employees providing regular and ongoing support, formal NASA panels and other subject matter experts. These safety-critical systems are also subject to strict requirements and verifications that ensure they will function as intended.
Overall, this teaming approach with NASA has proven invaluable. NASA has a wide array of resources and deep technical expertise that was generally made available in a partnership approach. Testing facilities, analyses, subject matter experts and a host of other contributions helped solve difficult technical problems, improve the safety and robustness of vehicle and help advance innovative approaches.
II. Commercial Crew Development Efforts: CCDev2 and Flight by 2014
The goal of SpaceX’s crew transportation system is to safely and reliably transport up to seven crew members from our launch pad on Cape Canaveral to the ISS, dwell on the ISS for up to 210 days and return the same number of crew safely to Earth. A two-stage, liquid oxygen and kerosene launch vehicle, the Falcon 9 possesses robust reliability features. The nine SpaceX Merlin engines that power Falcon 9’s first stage provide engine-out reliability from liftoff – a feature not offered by the Russian Soyuz – and the engine’s turbopumps run at lower pressure, making them more resistant to failure from foreign object debris (FOD) ingestion. The Dragon offers improved avionics redundancy and failure tolerance compared to Soyuz’s single gyroscope and accelerometer.
SpaceX selected the Dragon design so that it would be naturally stable entering the earth’s atmosphere, thereby maximizing the chances of a safe return to Earth even in the event of the vehicle’s control systems’ total failure. Other features vital to the cargo Dragon’s ability to safely reenter Earth’s atmosphere, such as the PICA-X heat shield, are already integrated into the Dragon capsule and will gain significant flight heritage during the Commercial Resupply Services (CRS) missions.
In the coming years, SpaceX will collect significant data and experience on the Falcon 9 and Dragon system from upcoming COTS and future CRS missions. Specifically, the Dragon spacecraft and Falcon 9 launch vehicle are currently scheduled to fly together at least 8 more times before a crew demonstration in 2014. The Falcon 9 itself is scheduled to launch a total of 14 missions prior to the first Dragon crew mission. The commonality between the cargo and crew versions of Dragon allows for significant end-to-end flight heritage and operational experience to be gained on critical functions – including launch, navigation and control, thermal protection, thermal control, power generation and distribution, avionics, software, entry guidance and recovery – well before the first crew flight. The avionics hardware is highly scalable, allowing SpaceX to significantly leverage the architecture tested and proven on cargo missions for use on crew missions.
Crew transport launch operations are similar to our cargo transportation launch operations inasmuch as they will take advantage of the safety, reliability and availability benefits of the “aircraft-like” operations of the Falcon 9. For example, full-stage static fire tests, similar to an aircraft ground run-up, are performed prior to each launch. During terminal countdown, the Falcon 9 throttles up to full power before being released for liftoff, allowing anomalies during engine startup to be safely mitigated. The Falcon 9 can support multiple full-thrust static fires and engine aborts without need for refurbishment, allowing for true “test-like-you-fly” operations. Additionally, Falcon 9 avionics support hardware-in-the-loop testing to prove out flight software in the actual flight hardware configuration.
a. CCDev 2: the Criticality of Launch Abort Systems
Under NASA’s Commercial Crew Development II (CCDev 2) program, SpaceX has opted to focus on accelerating the development of an efficient, life-saving launch abort system (LAS). SpaceX’s crew Dragon includes an integrated LAS, which we believe will yield numerous safety and performance benefits. The Dragon’s LAS is carried through orbit and reentry, with the abort systems available for use throughout the time the Dragon is boosted into space. Carrying the abort system all the way into orbit also eliminates the jettison of the abort system as a required event for the safe completion of a nominal mission.
SpaceX is further addressing launch vehicle malfunction detection and initiation of automated aborts as well as developing the necessary LAS engine hardware to implement such a design. This development will culminate in a series of engine tests to demonstrate safety, reliability, maximum thrust, minimum thrust, throttling capability, throttling rate and specific impulse.
The Dragon LAS is a vehicle-integrated, side-mounted engine system selected for its safety, reliability and performance after a system-level analysis conducted by SpaceX. Eight abort engines (known as SuperDracos because they are modified versions of Dragon’s existing Draco thrusters) are located around the periphery of the Dragon service section and fed by hypergolic propellant stored in the spacecraft propellant tanks. SuperDracos will carry the spacecraft away from the booster and are capable of separating the Dragon crew spacecraft from a failing booster while on the pad all the way through nominal on-orbit separation of Dragon from the second stage.
The LAS will be enabled after crew ingress and securing on the pad and will be disabled on orbit after Dragon separation from the second stage. The launch vehicle malfunction detection system for automatic abort will monitor the Falcon 9 and Dragon for engine failures, flight control failure, failure of the booster propellant tank and failure of the booster’s primary structure, among other signatures.
Abort responses will be determined by failure(s) detected and the phase of flight, in order to maximize survivability. For example, a significantly off-nominal change in tank pressure while the vehicle is on the pad may result in an instantaneous high-acceleration abort, while a performance-related failure of the second-stage engine during ascent may result in a delayed abort until ideal entry conditions are met, a pre-abort shutdown of the second-stage engine and a low-acceleration abort profile.
Ultimately, this technology, research, design and intellectual effort are about one thing: protecting human life. No one has summed it up better than Garrett Reisman, former astronaut and one of the heads of development for the Dragon LAS at SpaceX, who said, “We are not going to design a vehicle that I wouldn’t strap myself or my friends into.”
b. CCDev 2: Successes To Date and Approach Going Forward
To date, SpaceX has successfully completed four of the ten milestones in our CCDev2 Space Act Agreement (SAA) for a total of $40M of the $75M under SpaceX’s CCDev2 agreement. The first three milestones included a detailed program plan roll out, LAS propulsion Conceptual Design Review, Design Status Review and LAS Components Preliminary Design Review (PDR). In successfully meeting those milestones on schedule and on budget, SpaceX provided NASA with comprehensive Falcon 9/Dragon crew systems concept design insight including cabin layout, seat design, space suit design, life support system design, abort scenarios, concepts for the launch abort system, ground systems, abort trajectories, aerodynamics of ascent and entry and mass margins. The Design Status Review provided an opportunity for SpaceX to work with both NASA and industry teammates as partners and make desired crew systems design concept changes after peer review and feedback on the system-level designs and concepts.
With regards to the LAS components PDR, our most recently completed milestone, SpaceX engineers demonstrated to NASA’s satisfaction that the maturity of the LAS propulsion components design is appropriate to support proceeding with detailed design, fabrication, assembly, integration and test of LAS propulsion components test articles. We also provided evidence that the LAS propulsion design meets all system requirements with acceptable risk and can be developed within schedule.
Going forward, milestones will include abort engine fabrication and testing and further maturation of the vehicle system design and concept of operations. In addition, design and construction of a test facility for the launch abort engine is underway at the SpaceX rocket test facility in McGregor, Texas. The remaining hardware milestones will culminate in all key launch abort system propulsion components undergoing initial fluid and environmental development testing. Here, the SuperDracos will be hot-fire tested for a full duration. We will also demonstrate throttle capability, which is essential for abort maneuvers.
With respect to the crew systems design efforts, SpaceX will incorporate feedback from NASA and industry partners, present safety and mission assurance studies and provide a draft of the Vehicle Certification Plan (the path forward for getting crew flights certified by NASA). SpaceX is also investing in two self-funded milestones for crew cabin development with engineering prototypes of the cabin layout including seats where NASA astronaut trials will provide feedback on cockpit design.
c. CCDev 2: Designing Crew Accommodations for the Dragon
In parallel with the design and development work on the launch abort system engine and components, SpaceX is working on the design of other systems necessary to carry astronauts in the Dragon spacecraft. These systems include seats, spacesuits, an environmental control and life support system, displays and controls and ground systems.
SpaceX is designing the Dragon to carry seven crewmembers seated in two rows. The seats will be conformal and a mechanical force accommodation system will cushion any off-nominal landing impacts to assure crew safety. The crew will wear spacesuits to protect them from any rapid cabin depressurization emergency event. The suits will be rated for operation at vacuum and provide communication and cooling systems.
The Dragon environmental control and life support systems will provide the crew with fresh air ventilation, remove carbon dioxide and control humidity and cabin pressure. Fire detection and suppression systems will protect the crew in the event of an emergency. Accommodations will be provided for food preparation and waste disposal.
During the span of the CCDev2 SAA, SpaceX is completing preliminary designs on modifications to our launch pad and mission control center to be ready to fly astronauts. The launch pad will have a new tower and access arm to allow crew to enter the Dragon and egress quickly in the event of a launch pad emergency. Mission control will have a new console position for a flight surgeon for human missions.
In addition to these crew vehicle systems, the operation of the vehicle for nominal, contingency and emergency situations is being outlined for all phases of flight. A crew cabin mock-up is being constructed to allow NASA astronauts to evaluate crew accommodations and other human factors considerations. We are conducting preliminary designs for crew display and manual control hardware. The detailed operation of the launch abort system is also being characterized by defining abort modes, triggering events and abort trajectories. Finally, the safety and mission assurance analyses are being evaluated with the goal of ensuring that the Dragon and Falcon 9 vehicle will achieve a level of safety better than any human spacecraft ever flown.
This work on crew accommodations, along with the design and development of the launch abort system, as part of NASA’s CCDev2 program will result in a preliminary design of all the upgrades necessary to convert the cargo Dragon spacecraft and Falcon 9 into a certified crew transportation system.
d. Critical Design Review-level Development
Each flight of the Falcon 9 and cargo Dragon to the ISS brings us one step closer to flying astronauts to the ISS. Each of these flights will demonstrate many of the common elements between the cargo vehicle and the crew vehicle. Ultimately, the Falcon 9 will be one hundred percent common as between the cargo and crew vehicles. Therefore, though there is much work ahead, SpaceX already is beyond a Critical Design Review (CDR) equivalent level of maturity – and even into the production phase – with respect to many aspects of the vehicle system. This includes the main propulsion systems, structures, thermal protection systems (including the Dragon heat shield), power generation systems, altitude control, on-orbit propulsion systems, thermal control systems and GNC systems.
Crew-related modifications that have yet to reach a CDR-equivalent level of maturity include the remaining work on the launch abort system. The most significant remaining milestones will be full-scale pad abort and max-drag abort flight tests. In addition, crew displays and controls, a voice communication system, cabin layout and seats, space suits, environmental control and life support systems, launch pad and control center modifications, final approach guidance and control and the docking system will need to be matured to a CDR-equivalent level. The most significant remaining technical milestones for these systems will be human-in-the-loop testing of the environmental control and life support systems and spacesuits as well as static and dynamic testing of the seats and other mechanisms.
Beyond the launch abort system and crew accommodations, SpaceX’s efforts to transport crews aboard Dragon also require additional ground facilities and crew training equipment. These would support flight crew training for nominal, off-nominal and emergency conditions. Full- scale spacecraft mock-ups may be required for training. Launch Control and Mission Control teams will be certified as planned for other Falcon 9 and Dragon missions, including joint operations training with NASA Mission Control Center – Houston (MCC-H). The launch pad will also be modified to include gantry access for nominal ingress/egress and emergency egress of crew and pad support team.
e. SpaceX Falcon 9 / Dragon vs. Russian Soyuz
The Russian Soyuz is an unquestionably capable vehicle with significant flight heritage. Indeed, SpaceX has benefited from lessons learned from Soyuz operations and predecessor spacecraft. That said, we do not intend to duplicate the capabilities of Soyuz, but to improve upon them. Critically, the Dragon will have the capability to transport up to seven crew members to the ISS – four more astronauts than Soyuz. Further, the Dragon has the capability to carry additional unpressurized cargo to the ISS as well as the capability to return cargo from the ISS – areas in which the Soyuz is highly limited.
Additionally, the Dragon and Falcon 9 offer several safety improvements relative to the Soyuz, including:
* modern electronic control systems and computers;
* improved redundancy in the automatic control system;
* simpler and safer egress from the vehicle during an emergency on the launch pad;
* improved data displays for ascent and entry;
* capability for the crew to initiate an abort during the launch phase of the mission;
* capability for the crew to initiate the deploy of the landing parachutes;
* first stage engine out capability; and
* NASA insight into design, testing and production (NASA has limited insight to the
Soyuz rocket design as well as limited access to the production facilities for the
spacecraft and the rocket).
One of the largest safety distinctions between the Falcon 9 and Dragon system over the Soyuz transport system is the reduction in separation events – failure of separation events is one of the most common events leading to mission failures of space systems. The Soyuz launcher and spacecraft must release four side-mounted booster modules, the second stage, the third stage, the launch escape tower, fairing, propulsion module and habitation module prior to the point where the crew can enter safely in the Soyuz descent module. For the Dragon and Falcon 9, there are only four separation events which must occur prior to the Dragon’s entry: separation of the first
stage, second stage, external cargo module or trunk and for a nominal mission separation of the nose fairing.
III. Commercial Crew Integrated Design Contract Proposal
NASA’s recently issued draft request for proposals (DRFP) for the Commercial Crew Integrated Design Contract (CCIDC) has incorporated key features critical to facilitate successful commercial partnerships. SpaceX appreciates the fact that the contract will be firm fixed-price and milestone-based; includes cost sharing with fixed government investment; and waives cost and pricing data requirements inherent in certain Federal Acquisition Regulation (FAR) based contract formulations. SpaceX has offered NASA several suggestions to improve the DRFP and the subsequent contract implementation. Those suggestions focus on resolving certain key technical issues prior to contract award; focusing NASA approval authority with respect to design, development and test activities; placing a greater emphasis on development and test activities; and defining an insight plan that creates a teaming relationship between NASA and the contractor.
The DRFP indicates that several documents, including any proposed alternative technical standards, the integrated system baseline review (ISBR) and integrated critical design review (ICDR) plans, and the project management plan, are to be provided as drafts or initial documents at the time the proposal is submitted. All of these documents will have significant cost and schedule impacts and the technical standards will also drive the design of the vehicle. However, the final versions of these documents will not be approved until after the contract is signed. This timing makes it difficult to know exactly what commitments a contractor is making in its bid response. This concern can be easily addressed by having these key documents agreed to prior to signing the CCIDC contract.
SpaceX has found that the COTS and CRS public-private partnership approach with NASA combines and capitalizes on the strengths of both partners. The requirements in this DRFP have the potential to mitigate the proven benefits of this approach by exponentially increasing NASA’s involvement in design, development and testing.
SpaceX has also suggested that insight personnel be teammates. According to the DRFP, the NASA insight team is to be given full access to the contractor’s activities while being specifically precluded from providing any NASA resources (services, technical expertise, or access to Government property) to the contractor. As a result, the insight team is tasked to “audit and report” and thus becomes a second oversight team. Instead of an “audit and report” model, given successes witnessed under the interactions to date on the COTS and CRS programs, we propose that we work together as partners to a larger degree.
IV. The Commercial Space Market
At present, SpaceX has over forty flights on manifest, representing approximately $3.5 billion in revenues from the U.S. government, commercial and international business customers. NASA missions represent approximately 40 percent of those flights. Our ability to compete successfully in the domestic and international commercial market demonstrates the long-term viability of our business model and allows us to keep our costs to the U.S. taxpayer low.
SpaceX currently has the lowest launch prices in the world and, as noted by a Chinese government official earlier this year, even the Chinese do not believe they can beat them. Although our prices shatter the historical cost models of government-led developments, they are not arbitrary or premised on capturing a dominant share of the market, nor are they “teaser” rates meant to lure in an eager market only to be increased later. SpaceX’s prices are based on known costs and a demonstrated track record and exemplify the potential of America’s commercial space industry.
Critically, as the provider of an end-to-end solution for crewed missions, with our own manufacturing of the launcher and the spacecraft, and with the provision of all launch and recovery operations, SpaceX is uniquely positioned relative to competitors with respect to the impact of sales of commercial crew missions on the overall business. Each NASA purchase of our crewed capabilities complements our booster sales and production because the Falcon 9 will be the same for satellite carriage, cargo carriage, and ultimately crew carriage. Moreover, the commonality of features between our cargo Dragon and crewed Dragon likewise speaks to the economies of scale that we can achieve with spacecraft production and operations, maximizing efficiencies and driving down costs for the consumer. This is a key differentiator as between SpaceX and others when considering the commercial human spaceflight market.
However, as to the commercial human spaceflight market alone (taking into account the concept above that this market ties directly to the other well-known markets), NASA is the primary market driver for launching human beings into space. NASA is currently purchasing those services on the commercial market from Russia, the only currently available supplier. As a Nation, we are paying too a high price for those services – currently $56M per seat – due to the lack of competition and supply.
There is ample evidence of a demand for spaceflight beyond NASA, though it has yet to emerge as a substantial operational secondary market. In the past decade, seven individuals bought eight very expensive tickets to fly to the ISS on a Russian Soyuz. That may not seem like much, but even as prices dramatically increased since Dennis Tito first flew back in 2001, every seat available for sale has been sold. No tickets have been sold for the past two years because Russia is providing one hundred percent of their Soyuz capacity to serve the ISS partnerships. This evidence ratifies our view that offering seats for half or a third of the Soyuz price will expand the human spaceflight market. Moreover, alternative low-earth destinations such as the Bigelow space modules provide another strong market opportunity.
Non-spacefaring nations are also interested in space access. Between 1978 and 2010, ninety-six astronauts from thirty-one nations without indigenous spaceflight capabilities traveled into orbit.3 According to NASA’s Commercial Market Assessment, there is a desire among other countries “to send astronauts into space to perform scientific research, acquire technical knowledge, and increase national prestige.”4
3 NASA. Commercial Market Assessment for Crew and Cargo Systems Pursuant to Section 403 of the NASA Authorization Act of 2010 (P.L. 111-267), p.12, April 27, 2011.
4 Ibid. Further market potential also exists in the United States. The ISS is America’s national laboratory in space and like all laboratories its productivity depends on how many scientists can visit the lab, conduct their experiments and return to their public or private enterprises. NASA currently bases astronauts at the ISS for six months. That limitation is based on how many Soyuz capsules are produced each year, how long the Soyuz is rated to last on orbit and the high price of Soyuz seats.
The ISS can actually support seven crew members once we have a better crew rescue capability. Commercial crew will deliver that capability. Should the U.S. space industry lower the cost to between $20 and $30 million per seat, it will be possible for research scientists to visit the ISS for shorter periods of time, conduct dedicated research and return to Earth. Less costly, more regular access to ISS will enable more scientists to do more research in the same amount of time, with the same amount of dollars.
Overall, SpaceX’s business model is based on a diverse customer base that spans multiple markets. We have increased the U.S. share of the commercial space launch market since we started competing for and winning launches in 2008. For the first time in more than three decades, America last year began taking back international market-share in commercial satellite launch. Whereas in 1980, one-hundred percent of commercial launches took place from within the United States; last year, it was less than twelve percent. NASA’s and SpaceX’s efforts and investments are bringing critical launch revenue back to the U.S. and will bring thousands of jobs with it.
This remarkable turn-around was sparked by the investment NASA made in SpaceX in 2006 as part of COTS. By leveraging private funding with federal investment, controlling our costs and developing a diverse customer base, we are able to offer competitive pricing to our commercial and government customers. Safe, reliable and affordable transportation of cargo and astronauts to low Earth orbit by an American company will keep jobs in the United States; eliminate reliance on Russia to support the ISS; and providing significant taxpayer savings that instead can be invested in what NASA does best: pursuing the next frontier.
___________
Mr. Chairman, I am honored by your invitation to provide testimony today. Through continued public-private partnerships like the one that helped develop the Falcon 9 and Dragon system, commercial companies will transform the way we access space. Together, government and the private sector can simultaneously increase the reliability, safety and frequency of space travel, while greatly reducing the costs.
NASA’s Commercial Crew Development Program has the potential to be the most fiscally responsible means to rapidly advance American human spaceflight. To date, it has protected taxpayer dollars with fixed-price, pay-for-performance contracts. It has forced companies to compete on safety, reliability, capability and cost. And it leverages private investment – making taxpayer dollars go further.