Report on Top-Level Assessment of Use of Apollo Systems for ISS CRV (part 1)
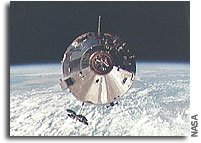
1.0 Background
A small team (Appendix 1) was chartered by NASA to make a top-level assessment of the viability of using the Apollo Command and Service Modules the basis for a Crew Return Vehicle, and potentially for a Crew Transfer Vehicle, for the International Space Station. This assessment was conducted 13-14 March 2003.
2.0 Leverage Provided by Apollo
The Assessment Team focused in on a small set of factors that might make the application of the Apollo Command and Service Module (CSM) an attractive option for serious consideration for the OSP CRV and perhaps the CTV.
3.0 Major Conclusions
The Team concluded unanimously that an Apollo-derived CRV concept appears to have the potential of meeting most of the OSP SRV Level 1 requirements. An Apollo-derived CTV would also appear to be able to meet most of the OSP Level 1 CTV requirements with the addition of a Service Module. The Team also surmised that there would be an option to consider the Apollo CSM concept for a common CRV/CTV system.
It was further concluded that using the Apollo Command Module (CM) and Service Module (SM) as an ISS CRV and CTV has sufficient merit to warrant a serious detailed study of the performance, cost, and schedule for this approach.
4.0 Cost
It was not possible to make an estimate of the cost of the design, development, and manufacturing of an Apollo-based CRV in the time available for this assessment. On one hand, the Apollo system is well understood, and the documentation should e helpful as a starting point. On the other hand, it was concluded that virtually every system would have to be redesigned , even if it were decided to be replicated.
It was judged that use of existing Apollo hardware (museums, storage) would not be possible due to obsolescence lack of traceability, and inability to qualify these components for flight. It is also doubtful that many Apollo drawings could be used directly in the manufacturing of the CMCRV because no tooling remains, and because of the incompatibility of these drawings with modern CAD/CAM design systems used by the US aerospace industry.
There was not agreement on the cost benefit of the use of extant Apollo documentation in the design of, what was agreed would be, a new vehicle with all new subsystems. However, it was judged that the development and manufacturing costs of an Apollo-derived CRV has the potential of lower cost than a winged vehicle die to its lower complexity level.
It was recognized that life cycle costs (LCC) are strongly dependent on ground support systems and recovery site infrastructure. It was therefore concluded that this factor must also be analyzed in depth (and with creativity) to produce valid LCC comparisons.
Although several prior studies have examined concepts based on the use of Apollo components, it is recommended that this new study should be in sufficient depth to permit it to be traced with other approaches being considered by NASA to the same set of current OSP requirements.
5.0 General Description of a Candidate Apollo-based CRV
This section provides a general description of the envisioned CRV based on the Apollo system. A more detailed description of each of the major CRV subsystems is contained in a subsequent section.
It was assumed that the CMCRV berthing can be done by attaching a slightly modified Apollo tunnel to the adapter. It was not clear whether the Apollo probe and drogue hardware would still be required in the CM docking tunnel to permit contingency docking, for example.
6.0 Water and Land Recovery Options
Water Recovery
This issue has significant impact on the viability and life cycle cost of an Apollo-based CRV and CTV. The Apollo CM utilized three parachutes to afford a water impact at approximately 28 ft/sec.
The hypersonic L/D of 0.4 for the CM resulted in a cross range of only about 18 miles. The landing accuracy was very high, however and resulted in a landing dispersion of approximately one mile from the target point. However, a substantial naval and air presence was deployed for the recovery operation.
The requirement for getting an injured or seriously ill to “definitive care within 24 hours” of the decision to evacuate the crew member places significant requirements on the recovery infrastructure. The low L/D means that a large number of landing sites must be chosen to ensure that one can be reached with a deorbit burn within the on-orbit dwell capability of the CMCRV. Furthermore, each landing site must be staffed 24/7 because of the need to recover the crew after an ISS emergency, which could occur without much advance notice.
To meet the OSDP requirements, the water landing sites would have to be selected close to land, so that helicopter recovery of the crew could be nearly immediate. Given that the propulsion module will follow the CM CRV in an entry trajectory of its own, not far behind the CMCRV, the water landing sites would have to be selected on the West coast of land masses, or near islands. Water recovery also would probably preclude the reusability of the spacecraft due to issues of corrosion.
Although the Apollo water landing approach can be used, it would require many worldwide water recovery sites near land, and would involve considerable risk and complexity to assure safe recovery of the crewmembers.
Land Recovery
Land recovery for the CMCRV eliminates the logistical burdens associated with water recovery, but places a new requirement to manage impact g loads to prevent injury, or aggravating injury to an ill or injured crewmember. A land recovery system also has the potential of developing a reusable spacecraft for the CRV. Options for ground impact load reduction include one or a combination of the following approaches:
- Soyuz-type landing rockets
- X-38 type parafoil
- Air bags
- Stroking/crushable seat structure (Apollo CM has such a system)
The issue of the entering propulsion module entry relatively close behind the CMCRV still exists however. Western coasts or islands are still candidate sites. Entry range-limiting of the propulsion module through another controlled retro burn or high speed ballutes would be options to ensure water impact (of the propulsion module) for more inland recovery sites (for the CTV).
The number of sites is still likely to be large, however, and the life cycle cost penalties must be evaluated in some detail. A smaller crew (4 vs. 6, for example) could be traded for more fuel and therefore a higher on-orbit dwell time and fewer landing sites necessary to meet the 24-hour requirement. The 24-hour requirement itself should be validated because of its significant impact on any CRV.
If a Block II CRV/CTV were developed using a more capable service/propulsion module, similar in concept to the Apollo service module, additional on-orbit dwell time could be significantly increased.
7.0 Potential Expansion of CMCRV to meet OSP Requirements for CTV
CTV Version of CRV
A CTV system based on the Apollo CM and a tailored Service Module would have much in common with the simple CRV. The internal systems and spacecraft itself would be very similar. The all-up CTV/Service Model would also have rendezvous and docking capability.
The CM/CRV and Service Module “stack” would also include the Apollo Launch Escape System for crew escape form launch to initial ascent. The stack would interface with an EELV as is currently planned for the OSP CRV/CTV.
The Service Module would lessen the internal CMCRV constraints on consumables and power and provide a very substantial Delta V capability and increased on-orbit time. This translates to capability to accommodate perhaps up to 7 crewmembers and the potential to reduce the number of worldwide land recovery sites an attendant life cycle costs. For the CTV system, land recovery would probably be required for life cycle cost reduction and crew safety, based on routine use.
The Service Module would not be recovered, and like the de-orbit propulsion systems, would reenter behind the crew module. The earth impact of these systems must be managed by selection of land recovery sites and potential use of downrange limiting systems for the SM/propulsion module to ensure ocean impact.
Common CRV/CTV Configuration
An intriguing option would be to develop in series or somewhat in parallel, a common CRV/CTV with a Service Module. The “Block II” vehicle would be configured for optimum on-orbit time relative to landing sites. A Crew Module/SM would be berthed at the ISS for emergency use. Crew Module/SM would also serve as the CTV.
If the vehicles could be held identical, it might be possible to bring crew to ISS on the CTV and return the homeward crew on the CRV, much the same as is done on the Soyuz today. The CTV Launch Escape System is jettisoned in powered ascent, thereby providing the same Crew Module configuration as the CRV, for entry.
A summary comparison of the CRV and CTV features and development effort is shown in Table 1. It was judged that the incremental time for development of a CTV/SM over that of the CRV alone would be about 1-2 years, including integration with the EELV.
8.0 Comparison of Command Module –Derived CRV with OSP Level I Requirements
Table 2 contains a summary Assessment of the Command Module-derived CRV and the CTV (with Service Module) against Level I OSP Requirements. Because of the top-level nature of this assessment, it was not possible to carry out numerical analyses. Where possible, factors that contribute to safety, cost, and schedule were included as related to the Apollo-derived systems.
9.0 Assessment of Subsystems for Command-Module-Based CRV (CMCRV)
The following preliminary assessments of the required subsystems for the CRV are provided to assist in understanding of the configuration and the required development effort. Most of the features described are also applicable to the CTV.
Structure
The outer mold lines of the Apollo CM would be retained, but the spacecraft structure must be redesigned for a 15 psi internal pressure. The Apollo CM was a 5 psi system. Use of the 5 psi design would impose significant interface issues on the ISS. Micrometeorite object damage vulnerability must also be analyzed, as for any CRV. The small profile of the CMCRV in all aspects is advantageous.
New structural materials should reduce weight and provide increased internal system capacity. It would be possible and probably desirable to scale up the 13 ft diameter base to the maximum size that could be accommodated within the orbiter payload bay. This would add valuable volume for packaging the internal systems (and perhaps allow for 7 crewmembers),
The weight should be able to be maintained per Apollo specifications, but maintenance of the c.g. appears to be a bigger challenge when rearranging the entire interior layout, including crew seat positions. Full scale, max gross weight entries of the CMCRV will be required to qualify the system. If an Apollo CM could be secured, it would serve as a useful early mockup (and possible boilerplate entry test article).
Guidance, Navigation, Control, Displays
Entirely new electronic systems and displays will be required. Triplex digital flight controls and a redundant integrated GPS/laser inertial navigation system, along with new avionics interfaces will have to be developed. Radiation hardened computers should be examined for use. There will be some legacy Apollo software specifications that could be useful in the design, such as the CM Digital Autopilot Control Laws.
The Apollo CM rotational hand controllers would probably be replicated. The weight, power, and volume of the total avionics and control systems would be expected to be quite less than that used in Apollo.
Modern system integration and software development and qualifications would be used. There are no extraordinary software requirements, but it will be 100% new software.
ECS/Life Support/Thermal Control
A 15 psi internal environment based on stored high pressure 02 or missed gas. Redundant flash evaporators would provide internal thermal control, but at the penalty of substantial water storage,. An alternative of radiators on the CMCRV should be examined. Suit connections for the larger CRV crew size would not be an issue.
The amount of consumables able to be contained within the CMCRV is a critical factor in the viability of the self-contained CRV. It is highly desirable to avoid storage of fluids/gases on the de-orbit propulsion module to support the CRV.
De-Orbit Propulsion/RCS
The CRV would utilize and externally-mounted de-orbit propulsion system. A replicated, scaled UDMH/N2O4 rocket, based on the Apollo Service Propulsion System should be studied as the baseline. The life storage limits on-orbit must be confirmed. Sizing would be the result of trade for delta-V vs. weight for on-orbit operations or cargo transfer. The de-orbit propulsion systems components developed by Aerojet for the X-38 CRV should be examined for applicability to the CMCRV. The RCS system is presumed to be MMH/N2O4 thrusters, based on the Apollo design. The on-orbit long term storage of propellant must be confirmed. The thrusters themselves can probably be replicated/scaled form Apollo design.
Recovery/Parachute System and Rocket Terminal Landing System
Weight of the CRV/CTV would be maintained very close to the Apollo CM system to enable use of the same drogue and ringslot main parachute system. Fabrication of the parachutes may be necessary and desirable with new, lighter weight materials. Materials used for the X-38 parachutes should be examined for use.
There will a requirement for an exhaustive parachute/pyrotechnic system test and qualification program comparable to that done for the Apollo CM. The Apollo test program can serve as a guide. Long-term space storage of a high-density packed parachute would be a major challenge in qualification.
The development of a terminal rocket landing system is suggested to enable a land recovery approach. The Soyuz system can serve as a reference model for the system. A weight penalty of approximately 500 lb was estimated based on recollections of earlier NASA studies. Land recovery issues are: side impact loads with obstructions, redundant rocket array, and rocket initiation sensors. There are available techniques and hardware to address this design without extraordinary risk.
Alternatives to the rocket system include a parafoil parachute system (change from Apollo parachutes!), airbags, or load absorbing seats.
Launch Escape System
The proven Apollo Launch Escape System (LES) would be replicated for the CTV only. This system provided a large escape envelope during the initial ascent trajectory. There were numerous abort modes throughout the ascent that provided a robust approach to crew safety. An extensive full-scale test and qualification program will be required.. The Apollo test program can serve as a guide.
Electrical Power
State of the art batteries would provide all electrical power. No fuel cells would be used. A new electrical power distribution system would be required. For the CTV, additional batteries can be carried in the Service Module
Heat Shield
The phenolic epoxy resin ablator used on the CM heat shield is no longer manufactured. There are much-improved ablators tat have flight experience that could be qualified for a crewed reentry spacecraft. These ablators can handle the heating load from earth orbit at lower weight. The baseline approach would be to design the ablative heat shield to be replaceable.
The cooler parts of the CMCRV can likewise be protected with modern materials, perhaps integrated into the structure. Apollo heating experience is substantial, and can be used to specify the heat protection required. A complete ground and flight test program is required for qualification, including entries and max gross weight.
Crew Seats
The seats can be replicated form Apollo specifications and designs. Te arrangement of seats can be based on the Skylab Rescue Study of 1972. Their placement in the CMCRV may be a critical issue from the perspective of maintaining the c.g. close to that of the original Apollo CM.
Communications and Telemetry/Instrumentation
Standard communications and telemetry adapted from the STS can be used, including TDRSS interfaces, uplink, S-band and UHF systems. Because of weight, power, and volume, packaging challenges are expected for the basic CRV, the instrumentation list must be constrained to safety for flight for the CRV.
Docking System
A berthing system will be required to interface with the ISS. An adapter could be used to interface the CMCRV system with the ISS system. This adapter could be prepositioned on a port prior to delivery of the CRV. A new berthing system for the CMCRV could also be considered to be able to be berthed directly to the ISS.
Appendix 1
Assessment Team Members
The Team members participating in this assessment were:
Aaron Cohen
Former Director NASA JSC; former Manager of the Command and Service Module in the Apollo Spacecraft Program Office; former Space Shuttle Orbiter Project Manager, responsible for design, development, production, and test flights,; former acting NASA Deputy Administrator.
Vance Brand
Apollo Soyuz (ASTP) and CDR for STS-5, STS41B, STS-35
Dale Meyers
Former V.P. and Program Manager- Apollo Command and Service Module, NAA/Rockwell; Former NASA Associate Administrator for Manned Space Flight; Former NASA Deputy Administrator
John Young
Gemini 3, Gemini 10 (CDR), Apollo 10, Apollo 16 (CDR), STS-1 (CDR), STS-9 (CDR)
Kenneth Szalai
Former Director, NASA Dryden; Chief Engineer NASA F-8 DFBW with Apollo GNC systems
The team convened 13-14 March 2003 to conduct the assessment.
Part 1 (text) | 2 (tables)