NASA Solicitation: Lightweight Materials for CEV Parachute Assembly System
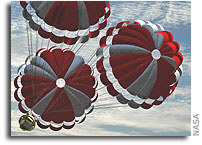
Synopsis – Jun 20, 2008
General Information
Solicitation Number: NNJ08256968R
Posted Date: Jun 20, 2008
FedBizOpps Posted Date: Jun 20, 2008
Original Response Date: Jul 10, 2008
Current Response Date: Jul 10, 2008
Classification Code: K — Modification of equipment
NAICS Code: 339999 – All Other Miscellaneous Manufacturing
Contracting Office Address
NASA/Lyndon B. Johnson Space Center, Houston Texas, 77058-3696, Mail Code: BH
Description
NASA/JSC has a requirement for Lightweight Materials for the CEV Parachute Assembly System (CPAS) shall be developed, manufactured, and laboratory and flight tested for use in the skirt to shoulder region of the main canopies. This effort is focused on CPAS meeting the required launch weight constraints and the required volume and mobility in the parachute compartment.
NASA/JSC intends to purchase the items from Airborne Systems. The lightweight Nylon broadcloth effort is irrevocably linked to their knowledge, as the CPAS subcontractor, of the CPAS configuration, design alternatives and changes, and test conditions. Materials must be flight-tested in the configuration in which they will ultimately perform, in order to verify that the relevant and complicated dynamic loads experienced upon deployment are tolerable. This requires access to Airborne Systems’ designs, which are proprietary, therefore will not be shared with another parachute company.
The lightweight Nylon broadcloth shall be a weight of 0.70-0.90 oz/yd2, and will therefore result in a weight savings of 25-50 lbs. to the system. Greater weight or lower weight savings is unacceptable. The technology shall offer significant reduction in parachute material volume in the constrained parachute compartment volume, aiding CPAS in avoidance of the increased risk introduced by high pack density. Pack density must be low enough to allow for complete and rapid deployment of chutes, without damage.
The approach shall be a phased approach. The first phase, Phase I, will be the laboratory phase, commencing with a fabric build, with a second to follow. Laboratory testing, to include vendor seam and joint testing, shall then be performed on the resultant fabric from each build to assess fabric potential for use in CPAS parachutes. Knowledge of the CPAS and access to CPAS subcontractor Airborne Systems’ propriety design shall be necessary for these evaluations. While a joint efficiency of 80% or higher is most desirable, seam and joint efficiency must be at least as high as 65%, which is the value of that of the reference CPAS parachute. The joint efficiency must be similar to that of baseline CPAS joints in the same region of the parachute. A report shall be delivered to document this work by September 30, 2008, as well as samples of material at a minimum of 4 yd2. It is at NASA’s discretion to opt out of the second fabric build if the first is satisfies optimal criteria.
If seam and joint efficiency do not meet the values of the reference CPAS parachute, a detailed analysis demonstrating that the new fabric with any reduced joint efficiency shall still provide significant mass and pack density reduction to the CPAS parachutes, may be accepted. In this case, the analysis would be performed by the vendor at no additional cost to NASA. Acceptability of any such analysis in lieu of attaining the efficiencies described above shall be evaluated by NASA.
The second phase, Phase II, shall be the flight test phase. Materials must be flight-tested in the configuration in which they shall ultimately perform, in order to verify that the relevant and complicated dynamic loads experienced upon deployment are tolerable. A single main parachute shall be built according to proprietary CPAS design specifications. It is NASA’s discretion to opt out of flight testing if the parachute manufacture is not successful. Flight testing shall be timed to take advantage of existing planned tests. A successful flight test shall demonstrate mass and pack density reduction, with parachute remaining packable and deployable, with complete and rapid deployment of chutes without damage. Flight performance needs be similar to reference CPAS parachute in inflation loads, parachute stability, and parachute drag area. CEV timelines are such that development and testing within the relevant system must be closely linked, and this work shall be completed by the CEV preliminary design review, November 21, 2008. A detailed report shall be delivered to NASA by the vendor, documenting Phase II of this effort, as well as the manufactured parachute.
NASA’s Johnson Space Center shall oversee this work and validate the materials testing. Each phase shall be broken into tasks, as delineated below:
Phase I: Fabric build I Vendor testing of build I fabric
Fabric build II Vendor testing of build II fabric
Seam and joint testing Final Report Phase II: Build single main parachute Flight test in cooperation with CPAS
Final Report
Each of these milestones shall be accompanied by delivery of any data generated and a brief report summarizing the task and any applicable findings, with an in-depth final report submitted at the end of each phase. Each of these milestones shall have a dollar value assigned that shall be billable at completion of the task, and payable upon confirmation of completion and acceptability by the Contracting Officer’s Technical Representative.
The Government does not intend to acquire a commercial item using FAR Part 12. See Note 26.
Interested organizations may submit their capabilities and qualifications to perform the effort in writing to the identified point of contact not later than 4:30 p.m. local time on July 10, 2008. Such capabilities/qualifications will be evaluated solely for the purpose of determining whether or not to conduct this procurement on a competitive basis. A determination by the Government not to compete this proposed effort on a full and open competition basis, based upon responses to this notice, is solely within the discretion of the government.
Oral communications are not acceptable in response to this notice.
All responsible sources may submit an offer which shall be considered by the agency.
An Ombudsman has been appointed. See NASA Specific Note “B”.
Any referenced notes may be viewed at the following URLs linked below.
Point of Contact
Name: Adrian D. Clayton
Title: Contract Specialist
Phone: 281-483-8498
Fax: 281-244-0995
Email: adrian.d.clayton@nasa.gov
Name: Robert G Kolb
Title: Contracting Officer
Phone: 281-244-8548
Fax: 281-244-5331
Email: robert.kolb-1@nasa.gov