Draft Environmental Assessment for Issuing an Experimental Permit to SpaceX for Operation of the Grasshopper Vehicle at the McGregor Test Site,Texas
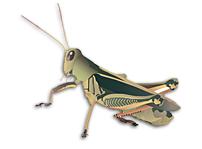
September 2011
Excerpts
1. INTRODUCTION
The Federal Aviation Administration (FAA) Office of Commercial Space Transportation (AST) proposes to issue an experimental permit to Space Exploration Technologies Corporation (SpaceX) to conduct suborbital launches and landings of the Grasshopper reusable launch vehicle (RLV) at the McGregor, Texas test site.
2.1.1 Grasshopper RLV 2.1.1.1 Description
The Grasshopper RLV consists of a Falcon 9 Stage 1 tank, a Merlin-1D engine, four steel landing legs, and a steel support structure. Carbon overwrapped pressure vessels (COPVs), which are filled with either nitrogen or helium, are attached to the support structure. The Merlin- 1D engine has a maximum thrust of 122,000 pounds. The overall height of the Grasshopper RLV is 106 feet, and the tank height is 85 feet.
The propellants used in the Grasshopper RLV include a highly refined kerosene fuel, called RP- 1, and liquid oxygen (LOX) as the oxidizer. The Grasshopper RLV has a maximum operational propellant load of approximately 6,900 gallons; however, the propellant loads for any one test would often be lower than the maximum propellant load. Even when the maximum propellant load is used, the majority of the propellant would remain unburned and would serve as ballast to keep the thrust-to-weight ratio low.
2.1.1.2 Pre-flight and Post-flight Activities
Pre-flight activities include preparing the Grasshopper RLV for launch and providing ground operations support for launch and landing. Preparing the Grasshopper RLV would begin when the vehicle is transported from its storage location at the McGregor test site to the launch pad. The Grasshopper RLV would be transported to the launch pad via a truck or tractor-trailer. Similarly, trucks would be used to transport the propellants from the propellant storage area to the launch pad.
Standard safety precautions, such as clearing the area of unnecessary personnel and ignition (including spark) sources, would be implemented. The Grasshopper RLV would be fueled with the appropriate amount of propellant for the proposed type of test (see Section 2.1.1.3 below for a description of tests). In the event of a spill or release, propellant-loading operations would be halted. Any spills would be cleaned up according to the McGregor test site’s Spill Response Procedure. Following the propellant transfer, the propellant-loading equipment would be removed from the launch area.
During preparations for launch, the electrical and mechanical connections would be inspected, and flight control diagnostics and health checks would be completed to ensure proper operation of electrical systems and moving parts. The Grasshopper RLV would initiate its formal launch sequence (i.e., ignition of its propulsion system) after all preparation and pre-flight operations were completed.
Post-flight activities include Grasshopper RLV landing and safing. During a nominal launch, the vehicle would land on the launch pad. Safing activities would begin upon completion of all launch and landing activities and engine shutdown. The LOX oxidizer system would be purged, and the fuel lines would be drained into a suitable container. Any remaining pressurants (i.e., helium or nitrogen) would be vented prior to declaring the Grasshopper RLV safe and moving the vehicle to its transport vehicle and staging area. A ground crew would perform and supervise all pre-flight, flight, and landing operations and would be familiar with the operating protocol for the specific launch.
2.1.1.3 Flight Profile (Takeoff, Flight, and Landing)
The Grasshopper test program expected to be conducted under an experimental permit would consist of three phases of test launches, which would be performed in the sequence detailed below. SpaceX would repeat tests under each phase as necessary until SpaceX is ready to proceed to the next phase. Multiple test launches could occur each day during daytime hours only, and would be consistent with SpaceX’s lease with the City of McGregor. For example, SpaceX is prohibited from conducting engine tests between the hours of 12:00 a.m. and 7:00 a.m. per SpaceX’s lease with the City of McGregor.
Launch Phases 1 and 2: Below-controlled-airspace VTVL
The goal of Phase 1 is to verify the Grasshopper RLV’s overall ability to perform a VTVL mission. During a Phase 1 test, the Grasshopper RLV would be launched and ascend to 240 feet AGL and then throttle down in order to descend, landing back on the pad approximately 45 seconds after liftoff. The Grasshopper RLV would stay below Class E Airspace (700 feet AGL). In Phase 2, there would be slightly less propellant loaded, a different thrust profile, and the maximum altitude would be increased to 670 feet, still below Class E Airspace. The mission duration during Phase 2 is again approximately 45 seconds.
Launch Phase 3: Controlled-airspace VTVL (maximum altitude)
The goal of Phase 3 is to verify the Grasshopper RLV’s ability to perform a VTVL mission at higher altitudes and higher ascent speeds and descent speeds. To achieve this, the maximum mission altitude would be increased from 670 feet incrementally up to 11,500 feet. The altitude test sequence likely would be 1,200 feet; 2,500 feet; 5,000 feet; 7,500 feet; and 11,500 feet. The maximum test duration would be approximately 160 seconds. The Grasshopper RLV would land back on the launch pad.
2.1.2 Grasshopper Launch Pad and Infrastructure
In order to support the proposed launches of the Grasshopper RLV under an experimental permit, SpaceX also proposes to construct a concrete launch pad and water lines.
The launch pad would be located to the southwest of the main portion of the McGregor test site (see Exhibit 2-2) and would encompass a total area of approximately 20,734 square feet (0.475 acre). The pad would be constructed at the end of an existing access road and would be built to comply with Texas code requirements for constructing on black clay. The launch pad would require approximately 6,534 cubic feet (242 cubic yards) of concrete, which would be supplied to the McGregor test site by approximately 27 concrete trucks in batches of 9 cubic yards. Construction of the launch pad would be expected to take 1-2 weeks. Additional support infrastructure that would be installed includes water lines, which would tap off of the main water lines approximately 500 feet from the proposed location of the launch pad. All tanks, with the possible exception of a 10,000 gallon water tank for fire suppression and washing the launch pad, would be mobile. The launch pad would be powered by portable generators. A typical Grasshopper RLV launch would use 50 kilowatt hours of energy at the launch pad.