Ten Ways 3D Printing Could Change Space
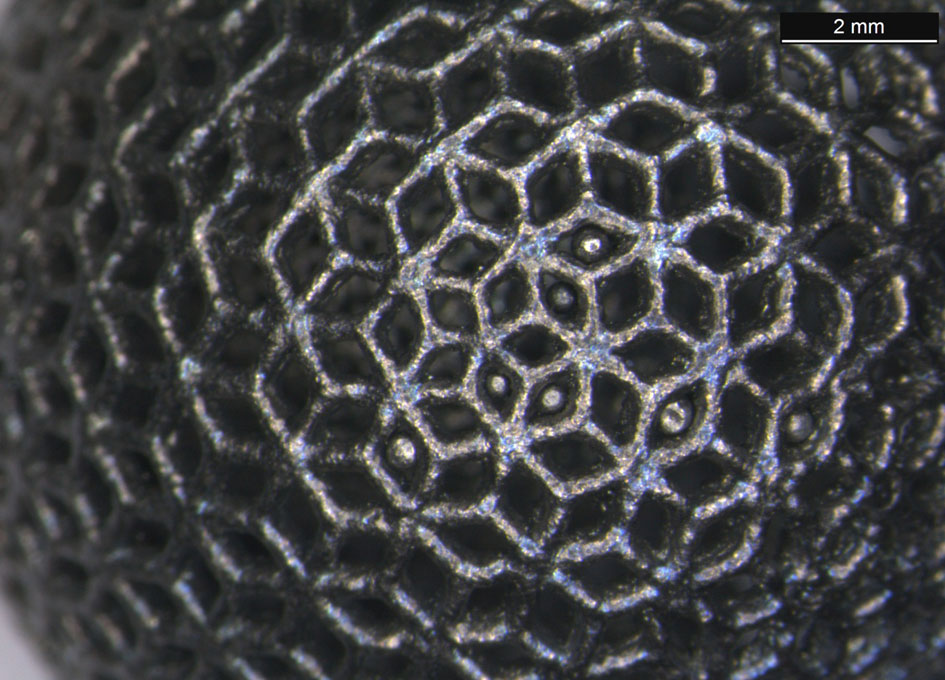
This close-up shows a titanium ball manufactured by 3D printing. ESA is investigating the potential of this promising new technology to transform the way space missions are put together.
1. Items impossible to make any other way
“This design is a perfect example of additive manufacturing (AM),” explains ESA materials engineer Benoit Bonvoisin. “These balls are hollow with a complex external geometry, making them incredibly light while remaining stiff. They simply could not have been manufactured in a single part, conventionally.”
With the idea that similar geometries could be used in future for ultralight satellite structures, the balls have been analysed in ESA’s Materials and Electrical Components Laboratory. Residue from the metallic beads used to clean the 3D-printed structure can be seen trapped within the ball lattice, showing the need for an improved cleaning process in future.
2. Computer designs translated to physical models
Instead of standard ‘subtractive manufacturing’ – where material is cut away from a single piece – AM involves building up a part from a series of layers, each one printed on top of the other. It is the difference from digging out a bunker to building a house.
The process starts with a computer-aided design (CAD) model, which is then sliced horizontally apart to plan its layer-based physical construction. Anything suitable for the printing process can be designed by computer then printed as an actual item, typically by melting powder or wire materials, in plastic or metal.
In February ESA hosted a ‘mapping meeting’ for the future development of AM for space at its ESTEC technical centre in Noordwijk, the Netherlands. Its 70 participants included representatives of 12 national delegations and the European Commission.
3. Novel design rules
“AM offers a totally different way of designing,” explains Laurent Pambaguian of ESA’s Materials Technology Section, coordinating the Agency’s AM research. “Traditional design rules are often linked to giving a cutting tool access to the bulk part – how do we remove the surplus material to produce the final item?
“AM, on the other hand, doesn’t mean we do away with all restrictions, but we are moving away for the traditional ‘design for manufacturing’ approach towards ‘design for need’.
“We also require fewer manufacturing steps, less material and energy – making it a greener process as well. The real challenge is to grasp the new AM design rules, and change our standard way of thinking accordingly, in order to maximise the benefits AM can bring us.”
4. Benefiting space, a low-volume industry
Laurent believes that AM, if applied well, can overcome many problems manufacturing for space has traditionally faced: “Space is a low-volume industrial sector, we need a relatively small amount of parts, but very well made. So, for instance, we might require only several kilos of a particular material, but then find it is only available to be purchased in 10-tonne bulks.