Supporting Life Beyond Earth Could Be Possible — Thanks To Graphene Innovation
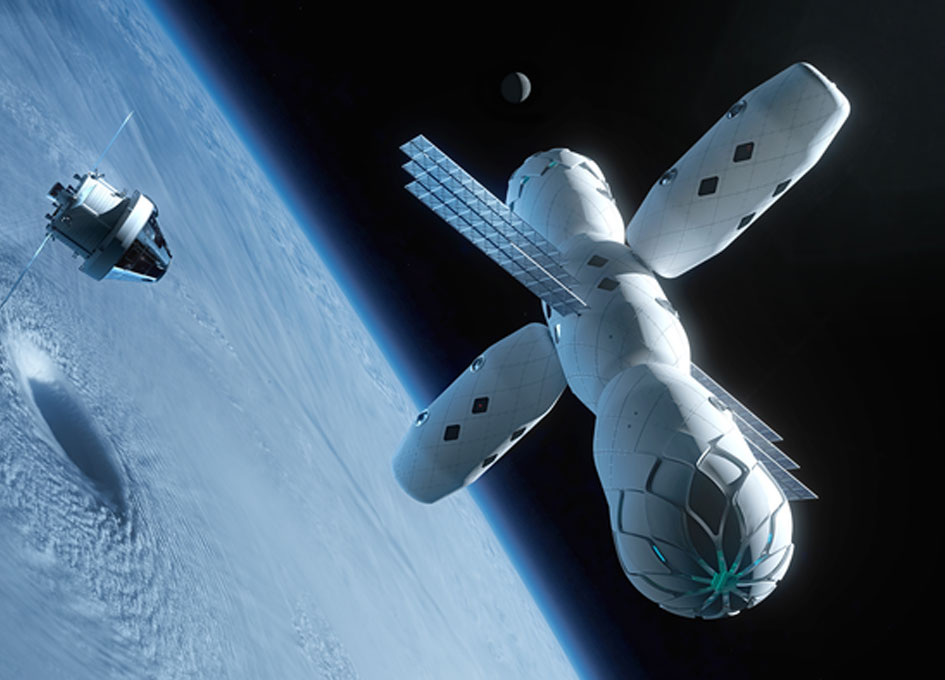
Advanced manufacturing experts from Manchester have revealed what human life in space could look like – with a graphene-enhanced space habitat developed to meet anticipated demand for human settlements beyond Earth.
A community of specialists at The University of Manchester have teamed up with global architect firm Skidmore, Owings & Merrill (SOM) to research the design and manufacturing of space habitats for the space industry.
With projections that the global space economy could grow to $1 trillion revenue by 2040, the innovation will raise the technology readiness level (TRL) of new lightweight composites using 2D materials for space applications.
In an international collaboration, Dr Vivek Koncherry and his team – supported by the Manchester-based Graphene Engineering Innovation Centre – are creating a scaled prototype of a space habitat with pressurised vessels designed to function in a space environment.
SOM, the architects behind the world’s tallest building – Burj Khalifa in Dubai – are contributing design and engineering expertise to the space architecture. Daniel Inocente, SOM’s senior designer in New York, said: “Designing for habitation in space poses some of the greatest challenges – it means creating an environment capable of maintaining life and integrating crew support systems.
“As architects, our role is to combine and integrate the most innovative technologies, materials, methods and above all the human experience to designing inhabited environments,” added Inocente. “Conducting research using graphene allows us to test lightweight materials and design processes that could improve the efficacy of composite structures for potential applications on Earth and future use in space.”
In the next five to 10 years most governments are expected to want a permanent presence in space to manage critical infrastructure, such as satellite networks – as well as considering the potential opportunity of accessing space-based resources and further scientific exploration.
Dr Koncherry said: “A major barrier to scaling up in time to meet this demand is the lack of advanced and automated manufacturing systems to make the specialist structures needed for living in space. One of the space industry’s biggest challenges is overcoming a lack of robotic systems to manufacture the complex shapes using advanced materials.”
The solution is incorporating graphene for advanced structural capabilities, such as radiation shielding, as well as developing and employing a new generation of robotic machines to make these graphene-enhanced structures. This technology has the potential to revolutionise high-performance lightweight structures – and could also be used for terrestrial applications in the aerospace, construction and automotive sectors.
James Baker, CEO Graphene@Manchester, said: “The work being led by Dr Koncherry and his colleagues is taking the development of new composites and lightweighting to another level, as well as the advanced manufacture needed to make structures from these new materials. By collaborating with SOM there are opportunities to identify applications on our own planet as we look to build habitats that are much smarter and more sustainable.”
The space habitat launch coincides with a series of world firsts for graphene in the built environment currently happening here on Earth – including the first external pour of graphene-enhanced Concretene and pioneering A1 road resurfacing – all supported by experts in the city where the super strong material was first isolated.
Tim Newns, Chief Executive of MIDAS, Manchester’s inward investment agency, said: “This exciting piece of research further underlines the breadth of applications where advanced materials and in particular graphene can revolutionise global industries such as the space industry. In addition to world-leading expertise in graphene, facilities such as the new Advanced Machinery & Productivity Institute (AMPI) in Rochdale, will also support the development of advanced machines and machinery required to bring these applications to reality.”