Aerojet Rocketdyne Successfully Demonstrates Low-Cost, High Thrust Space Engine
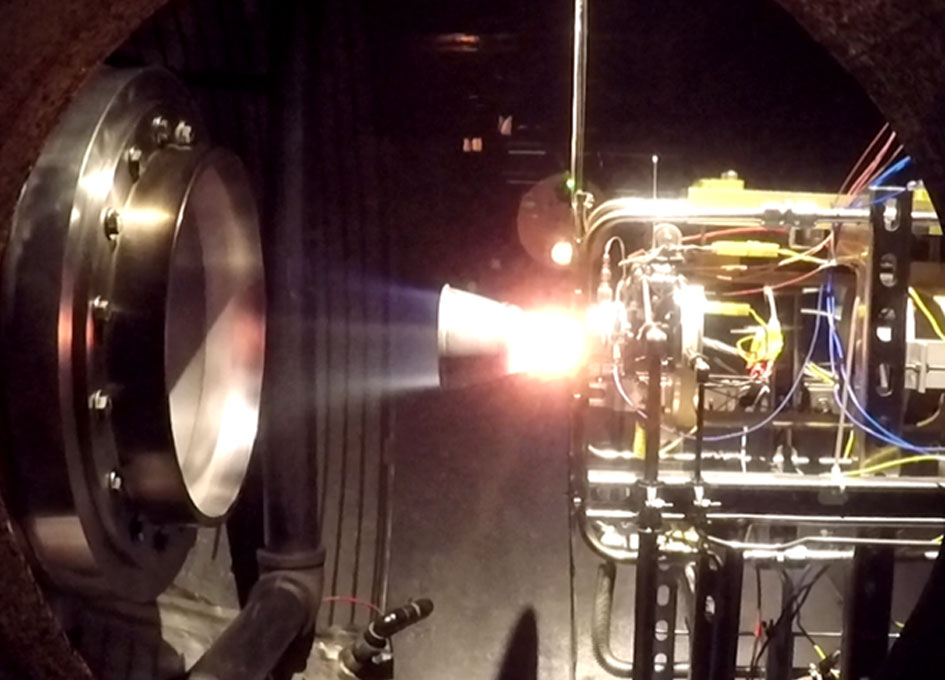
Aerojet Rocketdyne successfully completed hot-fire testing of a new in-space engine, designated ISE-100.
Developed for commercial in-space applications, ISE-100 has the potential to be a critical element for future lunar robotic missions. Producing 100 pounds of thrust, the ISE engine has the capability to provide downward thrust during landing, easing spacecraft down to the lunar surface.
ISE-100 is the latest in-space engine developed by Aerojet Rocketdyne, adding to our portfolio of mission-proven thrusters that have propelled spacecraft to every planet in the solar system and interstellar space, and provided landing propulsion for Mars and asteroid missions.
“As the nation sets its sights back on the Moon, Aerojet Rocketdyne stands ready to support commercial and NASA endeavors with reliable and affordable propulsion systems, like our new ISE-100 engine,” said Aerojet Rocketdyne CEO and President Eileen Drake.
Utilizing MON-25/MMH propellants, the ISE-100 is an affordable and dependable engine option for commercial operators to power spacecraft. MON-25 is a high performance storable oxidizer with a low freezing point that is particularly well suited to deep space environments. Another element of the low cost design approach is the engine’s additively manufactured Titanium injector, which completed the entire test series without anomaly.
During the test program, the engine successfully accumulated 75 individual tests, 774 pulses and more than 500 seconds of hot-fire time. Key tests performed in this program included multiple long duration steady state burns; multiple short pulse trains; and a long endurance duty cycle, representative of potential robotic lunar lander missions.
“We’ve developed and demonstrated an engine that is low cost, high performance and capable of landing payloads on the Moon,” said Aerojet Rocketdyne’s Vice President of Advanced Space Programs Julie Van Kleeck.
The ISE-100 engine will now move from the development phase to the certification phase where it will undergo additional configuration testing with flight qualified materials.