NASA Uses 3-D Printing for J-2X Rocket Engines
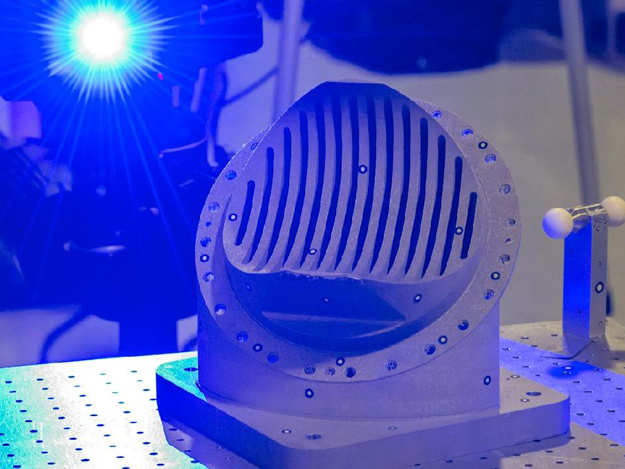
The latest in cutting-edge manufacturing is already making a significant impact in the future of space exploration.
Pratt & Whitney Rocketdyne of Canoga Park, Calif., the prime contractor for the J-2X engine, recently used an advanced 3-D printing process called Selective Laser Melting, or SLM, to create an exhaust port cover for the engine. SLM uses lasers to fuse metal dust into a specific pattern to build the cover, which is essentially a maintenance hatch for the engine’s turbo pumps.
On March 7, this part was exposed to the strenuous conditions of a rocket engine firing during a test at NASA’s Stennis Space Center in Mississippi, and will be a part of the rest of this test series. The J-2X is undergoing rigorous testing in support of the agency’s Space Launch System Program, or SLS, managed at NASA’s Marshall Space Flight Center in Huntsville, Ala.
“The successful test of this part built with new technology helps prove the concept of selective laser melting,” said Todd May, SLS Program manager. “As we pursue America’s next heavy-lift rocket, our engineers are proactively looking for methods like SLM that will make the rocket more affordable. For example, the new part cost 35 percent of what it would cost to make the same part using conventional methods. That is significant savings and something we hope to spread over the rest of the program.”
The J-2X engine before installation at the Stennis Space Center. (NASA/SSC)
The port cover is exposed to intense temperature and exhaust conditions during the engine firings. After the successful run of the engine, test conductors open this cover to check the torque on the turbo pump and visually inspect the cover itself. Initial conclusions are that it performed exactly as expected.
“This is the first time a SLM part has been hot-fire tested during a full-scale engine test,” said Mike Kynard, manager of the SLS Liquid Engines Office. “Though the port cover is a relatively simple part of a complex liquid engine, it allows us to develop design standards, inspection techniques, materials characteristics among other specifications which lead us to the ultimate goal of using a SLM manufactured part on a human-rated liquid rocket engine: the RS-25 on SLS’s first flight in 2017.”
The Marshall Center also recently proved how this technology would save on the SLS budget by shaving months off the construction of certain engine parts. One such part is the pogo z-baffle of the RS-25 engine. Four RS-25s will help drive the core stage of the SLS into orbit and the baffles help reduce the potentially violent vibrations the engine experiences during flight.
Comparing traditional manufacturing and welding, at right, with Selective Laser Melting. (NASA/MSFC)
“Traditionally, the forming, machining and welding of this baffle would take nine to ten months,” said Andy Hardin, SLS subsystem manager for liquid engines. “After creating the part using computer-aided design, we built this baffle with SLM in nine days, obviously significant time and cost savings. The lack of a traditional weld also makes this part more structurally sound.”
Selective Laser Melting is one of several cutting-edge technologies and concepts being studied by the SLS Advanced Development Office, which is researching ways to evolve SLS into the world’s most powerful launch vehicle safely, affordably and sustainably. For more on the SLM technique, visit here.
“The successful J-2X test paves the way for us to design and manufacture more complex SLM-created parts to be installed on the J-2X and RS-25 engines ultimately providing a significant cost and schedule savings,” said Kynard.
The first test launch of the SLS from NASA’s Kennedy Space Center in Florida in 2017 will send an uncrewed Orion spacecraft around the moon. A collection of four RS-25s will launch the capsule into orbit on the SLS core stage.