United Launch Alliance Creates Fix for Centaur V Hydrogen Leak, Targets Late 2023 for Inaugural Vulcan Centaur Launch
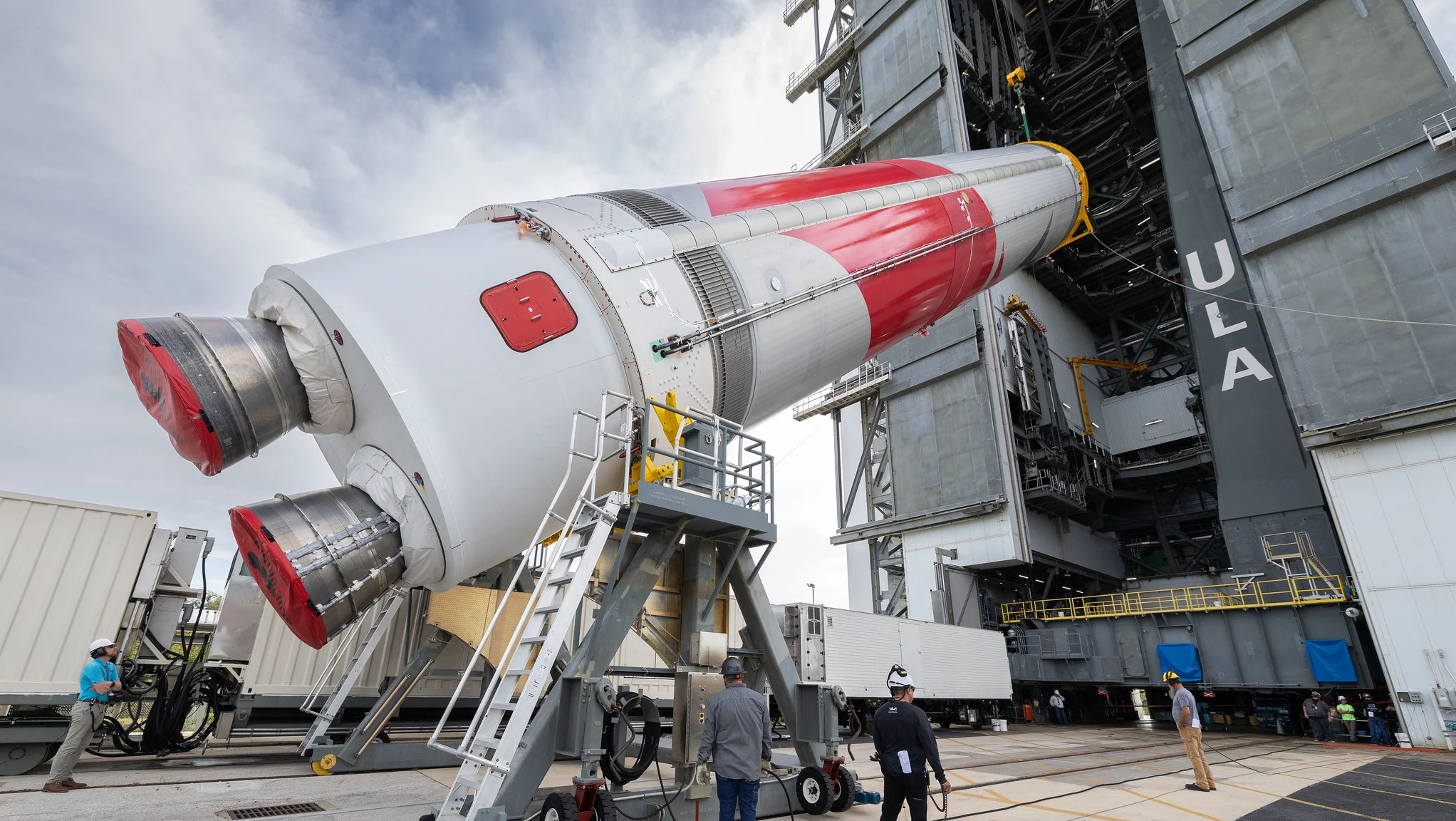
The inaugural launch of United Launch Alliance’s next-generation Vulcan-Centaur heavy-lift rocket will now take place in 2023, according to a recent announcement by ULA CEO and President Tory Bruno.
Speaking to reporters Thursday morning (July 13), Bruno said that United Launch Alliance had determined the source of the hydrogen leak that caused a Centaur V upper stage to explode on March 29 during a test at NASA’s Marshall Space Flight Center — and that the company had developed a fix for the leak on future rockets. The explosion forced ULA to delay the inaugural launch, initially scheduled for May, pending that investigation.
“We expect to fly in the fourth quarter of this year, before the end of the year,” Bruno told reporters.
Bruno added that the recent explosion of a Blue Origin-made BE-4 engine during a test conducted last month was likewise already understood by engineers and would not disrupt the new launch schedule for the inaugural Vulcan-Centaur certification launch, or Cert-1.
The Vulcan Centaur rocket, which ULA began developing in 2014, is the company’s next-generation replacement for both the Atlas V and the Delta IV Heavy rockets it has been flying for years. ULA already has contracts to launch private and government payloads aboard the Vulcan Centaur, including 38 launches of Kuiper broadband internet satellites for Amazon, and National Security Space Launch (NSSL) payloads for the US Space Force.
The two-stage launch vehicle consists of the Vulcan main booster stage, which uses two methane- and liquid oxygen-fueled BE-4 engines, and the Centaur V upper stage, which uses liquid oxygen and liquid hydrogen to power two RL-10 engines. Together, the two Vulcan Centaur rocket stages will lift up to 60,000 pounds (27,215 kg) into low Earth orbit.
Minus 150 to 300 pounds, that is.
During Thursday’s call with reporters, Bruno explained that the fix for the hydrogen leak that led to the March 29 explosion will involve adding a slight bit of mass to the Centaur V upper stage.
The Centaur V upper stage, he explained, is essentially a 40-foot-long steel cylinder, 18 feet in diameter, with walls that are only fractions of an inch thick.
“The thickest part of that structure is probably similar to really high-quality cardstock,” he said. “Once upon a time, you have likely held a wedding invitation that was thicker than the walls of this structure.”
Capping the ends of the cylinder are two domes made of 15 curved steel triangles that are surface-milled even thinner, to about 26 thousandths of an inch, and laser-welded together along 12-foot seams, Bruno explained. At their apex is a thick steel door that allows access to the liquid hydrogen tank in the upper dome, and the liquid oxygen tank in the lower dome.
During the March 29 test, which was designed to put the Centaur V test vehicle through every possible stress and load it might encounter during service, and qualify the entire rocket fleet for all possible missions, Bruno says, a crack formed near the upper door and propagated along one of the triangle seams. Once enough hydrogen had concentrated, a spark ignited the fuel and it caused the explosion.
The initial crack formed because of two failures, Bruno explained. First, the geometry of the triangular metal sheets meeting the thick door at the top of the upper dome couldn’t handle the stress it was exposed to. Second, the seams between the triangles were not as strong as initial laboratory tests indicated.
The solution, Bruno said, is to add a steel ring around the top of the domes, as well as strips of steel that will run the length of the seams between each of the 15 triangular pieces.
“We call these doublers,” Bruno said. “Not a very sophisticated or high-tech or high-risk action or design because we just simply need it to be just a little bit thicker; 20 percent thicker.”
The doublers will initially add about 300 pounds to the weight of the Centaur V upper stage, though surface milling after testing could reduce the added weight by about half, he said. Though it represents less than 1 percent of the rocket’s payload to orbit capacity, “every pound of inert weight reduces a pound from the payload, so 300 pounds means 300 pounds less satellite.”
In the future, ULA will also return to arc welding the seams between the triangular pieces, as they had for the earlier Centaur III rocket stage, Bruno added, noting that laser welding did not appreciably speed up the production process as was anticipated.
As for the June 7 Be-4 rocket explosion, it took place during acceptance testing, Bruno said, who explained that rockets and components undergo two types of testing.
Qualification testing verifies that a design works, and Blue Origin has already completed qualification resting of the BE-4 engine.
Acceptance testing, however, is a test each component must undergo to prove that it was manufactured correctly before being incorporated into a launch vehicle, Bruno explained, noting that acceptance test failures are common, even among engines.
“This is not unexpected,” he told reporters. “It won’t be the last and there will be other components on the rockets that also fail acceptance testing. I’m flattered by the attention we have now that a routine acceptance test was colorfully discussed on social media, but it really isn’t news.”
As for the fourth quarter goal for launching Cert-1, Bruno said the specific launch date actually depends on one of the payloads rather than the rocket itself. Specifically, there’s a chance Cert-1 will have to wait on the robotic Peregrine Lunar Lander made by Pittsburgh’s Astrobotic, as part of NASA’s Commercial Lunar Payload Services program developed to help private companies deliver small payloads to the Moon.
“There are a handful of days each month that are suitable for Astrobotic to be launched and arrive under the conditions they want,” Bruno said. “We are in the process right now of working with them to figure out when their windows are within that quarter. And we don’t have that answer yet, so that’s why I’m not giving you an exact date.”