Testing 3D-printed Metal Parts For Space
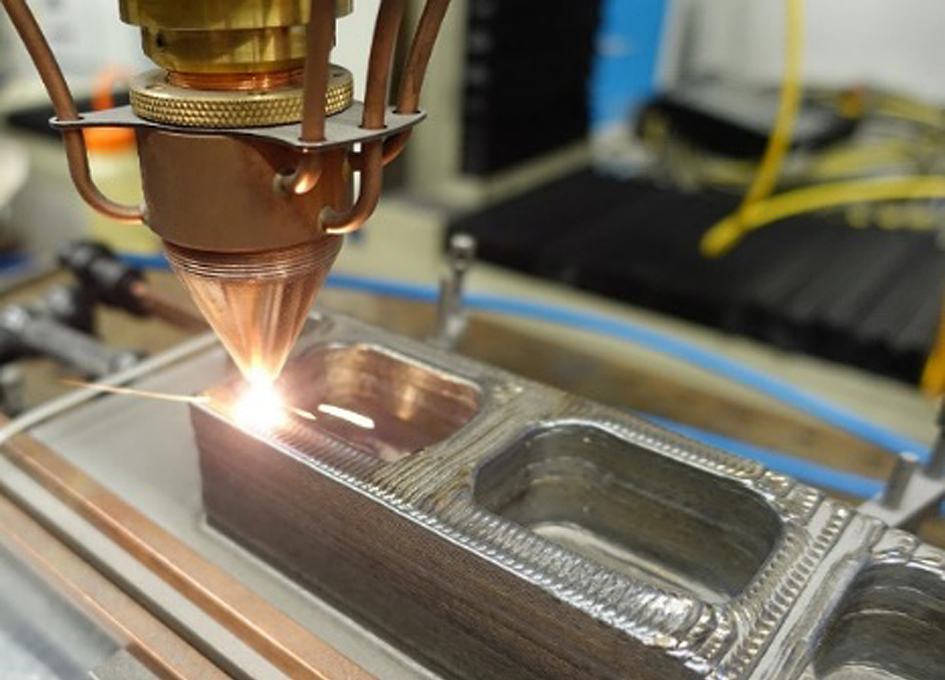
3D-printed metal parts produced through a Europe-wide collaboration of high-performance industrial sectors have undergone extensive testing for space use – tested to destruction in many cases – by ESA’s specialist advanced manufacturing lab in the UK.
ESA’s Advanced Manufacturing Laboratory based in Harwell, UK, took delivery of the sample parts, produced as an output of the four-year AMAZE programme, harnessing metal 3D printing to produce lighter, cheaper, better products.
“Space is an extremely challenging environment, so our lab had to perform a wide range of testing,” explains Lab member Maximilian Sprengel.
“The parts were pulled to failure and fatigue tested, where they were repeatedly subjected to heavy loads until breaking. They also underwent cryogenic and high-temperature testing to establish their resistance to the wide temperature fluctuations encountered in orbit: do they shrink, swell or hold their shape?”
Ranging in size from a support bracket for a Sun sensor to a metre-wide satellite core, the samples were also scrutinised using the Lab’s suite of powerful microscopes and X-ray CT scanner.
“These parts have been made using traditional materials, such as titanium or aluminium alloys as well as Invar – a nickel-iron alloy highly prized for its ability to resist expansion or contraction,” adds Andrew Barnes, overseeing the Lab.
“But unlike standard parts, these have been produced using various methods of 3D printing, post-processing and surface finishing. We need to understand the influence this has on their resulting properties and performance.”
“We’ve also been harnessing the world-class resources available around us on the Harwell campus to learn more about the underlying physics involved. Using the X-ray beam line at Harwell’s Diamond Light Source synchrotron gave us a close-up view of a laser melting metal powder as a 3D printer prints.”
The goal is to develop common procurement, qualification and acceptance standards for 3D printing. The starting point for a 3D printed part is feedstock material, such as metal powder. Companies need common standards on judging feedstock quality, how best to 3D print with it, finish parts to an acceptable standard and then test them.
“Through our involvement with the European Cooperation for Space Standardization, ESA has led the development of space industry standards for many years,” says Andrew. “Now we aim to do the same in the field of metal 3D printing.”
Last month representatives of European universities and space companies including Thales Alenia Space, Lockheed Martin UK and Airbus Defence and Space met at the Lab to discuss results from AMAZE and the Lab testing. The event was organised together with the Manufacturing Technology Centre in Coventry, coordinator of the AMAZE programme.
Launched in 2013, AMAZE – short for Additive Manufacturing Aiming Towards Zero Waste and Efficient Production of High-Tech Metal Products – was the largest R&D programme for 3D printing ever run. ESA was among 26 academic and industrial partners developing novel metal 3D-printing processes and products.
ESA helped to initiate the programme, funded by the European Commission’s Seventh Framework Programme. The Agency joined manufacturers Airbus and Thales Alenia Space in assessing prototype products for space use, while comparable end-users did the same for the automotive, aeronautics and nuclear fusion sectors.
The ESA-RAL Advanced Manufacturing Laboratory is based at the UK Science and Technology Facilities Council’s Rutherford Appleton Laboratory in Harwell, Oxfordshire, directly adjacent to ESA’s UK facility ESCAT, the European Centre for Space Applications and Telecommunications.
The Lab is focused on the assessment of new material processes, joining techniques and 3D printing technologies for application in space, in support of ESA’s Advanced Manufacturing initiative.