Building Block Architecture for Space Exploration
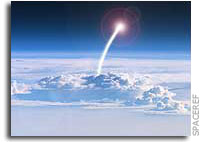
1. Description
It is proposed that a basic building block architecture with a large built-in growth potential be used to provide mission capabilities for LEO, lunar and Mars missions. By using a common core and launch facilities, two, four, or six standard RSRM’s could be added for meeting various mission requirements. Available and operational space transportation equipment, technologies and processes would be incorporated to save both time and money and to ensure safety and reliability of the system. A new launch facility would be a pacing item.
The vehicle is derived from operational elements of the Space Shuttle and commercial EELV’s including the Shuttle RSRM’s, External Tank diameter tooling, RD-180 rocket engines (LOX-RP) from the Atlas 5, and from planned J-2X LOX/H2 engines for upper stage use. The core tank would be modified to allow 2, 4, or 6 strap-on solid rocket boosters as demonstrated on numerous rocket systems. With this arrangement, a flexible and robust space launch system can be readily developed and operated with many inherent cost savings.
Reference: AIAA 2005-4181 “The Business Case for Spiral Development in Heavy-Lift Launch Vehicle Systems” 41st AIAA/ASME/SAE/ASEE Joint Propulsion Conference July 10-13, 2005 / Tucson, AZ Rebecca A. Farr, David L. Christensen, Edward L. Keith
2. Status of Proposed System
The referenced paper provides additional details concerning the proposed space transportation architecture. The technology elements are operational and readily available. Design and development is needed to integrate the key elements, modify the existing STS external tank to accommodate new structural loading and propellant arrangements, etc. The use of kerosene in the core stage instead of hydrogen provides a number of advantages which enhance operational and cost factors. A new launch facility (or perhaps two will be preferable) is required.
3. Cost and Schedule
The basic cost and schedule for the proposed system needs further assessment. Commonality of the core stage and use of 4 segment solid rocket boosters should realize a large cost saving compared to the current architectural approach being considered by NASA. A single core design to accommodate crew, cargo, or a combination of both payload capabilities is less complex and allows engine out capability due to the six RD-180 engine cluster / propulsion system in the core stage. By adding the RSRM (4 segment) elements, cost savings are obvious over the currently planned use of the five segment solid rocket motors. This alone should reduce the development cost by over one billion dollars.
4. Estimated Benefits
The proposed Building Block Architecture will allow the United States to meet our Space Transportation needs throughout the Solar System. By adding additional boosters to the common core stage, the exploration of the Moon, Mars and the Solar System can be achieved with one basic architecture and transportation system (including up to 850,000 lbs to LEO, 340,000 for a trans-lunar trajectory or 250,000 lbs for a Mars transfer orbit). In addition, very large scientific payloads can be sent throughout the Solar System and both defense and commercial payloads can be accommodated for a variety of missions and potential applications.
Prepared by: David L. Christensen
DAVID L. CHRISTENSEN
September, 2006
David Christensen began his career in rocketry in 1953 at Fort Bliss, Texas and White Sands Proving Grounds in New Mexico. He joined the Von Braun rocket team at the Army Ballistic Missile Agency in February 1956 working on Liquid Rocket Propulsion Systems for the Redstone, Jupiter and Saturn rockets and was Project Engineer for the Saturn H-1 rocket engine. During this exciting period of time, at the birth of the space program, Dave and other members of the Rocket City Astronomical Society published a quality magazine called “Space Journal” which was distributed nationally. Articles were contributed to the Journal by Dr. Oberth, Dr. von Braun, Dr. Stuhlinger and other key rocket team members to help gain public interest in space travel. The proceeds of this volunteer effort were used to help build the local observatory and planetarium.
He started his own consulting firm in June 1960 to provide representation for aerospace firms and also provided key technical and management support services on the Saturn-Apollo Program under several contracts. In 1967, he joined the University of Alabama in Huntsville (UAH) as a Senior Research Associate and initiated the Saturn History Program. This program required extensive documentation research and interviews and resulted in the NASA book entitled “Stages to Saturn”.
Mr. Christensen was Director of Alternate Energy Research at UAH and led many research studies, conferences and workshops investigating the use of solar energy for Earth-based and space-based power systems. In 1974, he led a special research effort under a NASA contract to investigate the use of the planned Space Shuttle for educational purposes. He also supported research efforts and performed extensive interviews for the book “The Rocket Team”, the definitive story of the Von Braun rocket team. He wrote the scripts for several educational filmstrips, which were narrated by Wernher von Braun including “Stations in Space” and “Dividends From Space”.
Starting in 1980, Mr. Christensen worked for several major aerospace firms including United Technologies, Wyle Laboratories and Lockheed Martin on a variety of space programs. In 1990, he organized and chaired “The Space Summit-An International Conference on Manned Space Exploration” in support of the NASA Space Exploration Initiative. He was Chairman of the National Space Club in Huntsville (1991-1992), is an Associate Fellow in the American Institute of Aeronautics and Astronautics, and a member of the Experimental Aircraft Association. During 2001-2002, he was Chairman of the Space Propulsion Synergy Team (SPST), a national organization of volunteers that supports NASA space transportation programs with emphasis on propulsion system technologies and operational assessments.
Until his recent retirement (May 2004), Mr. Christensen was Senior Staff Engineer and Manager of Business Development for Lockheed Martin Astronautics in Huntsville (1996-2004) He was the Project Lead for liquid rocket engines and propulsion system integration on the Liquid Fly Back Booster considered by NASA for replacement of the Solid Rocket Boosters on the Space Shuttle, and Program Manager for a high speed test-bed study by NASA to test combined cycle rocket/ramjet engines needed for our future space launch systems. He was also the Lockheed Martin Team Lead on a NASA funded task to design a “clean sheet” reusable space launch vehicle incorporating air-breather engines for the booster and liquid hydrogen/liquid oxygen based rocket engines for the orbiter.
Since his retirement, Mr. Christensen has supported the UAH space program archives development and oral history projects. As a consultant, he has performed peer reviews of internal space exploration proposals for NASA Headquarters and performed research studies for Bigelow Aerospace to assess design concepts for inflatable structures used as habitats in orbit and on the surface of the Moon and Mars. He is currently supporting NASA in the development of knowledge based information systems that can provide selected expertise, lessons learned and related examples based on space systems design, development, operational and program management activities from numerous sources.”