Forecasting The Performance Of A Space Antenna – Before It Is Built
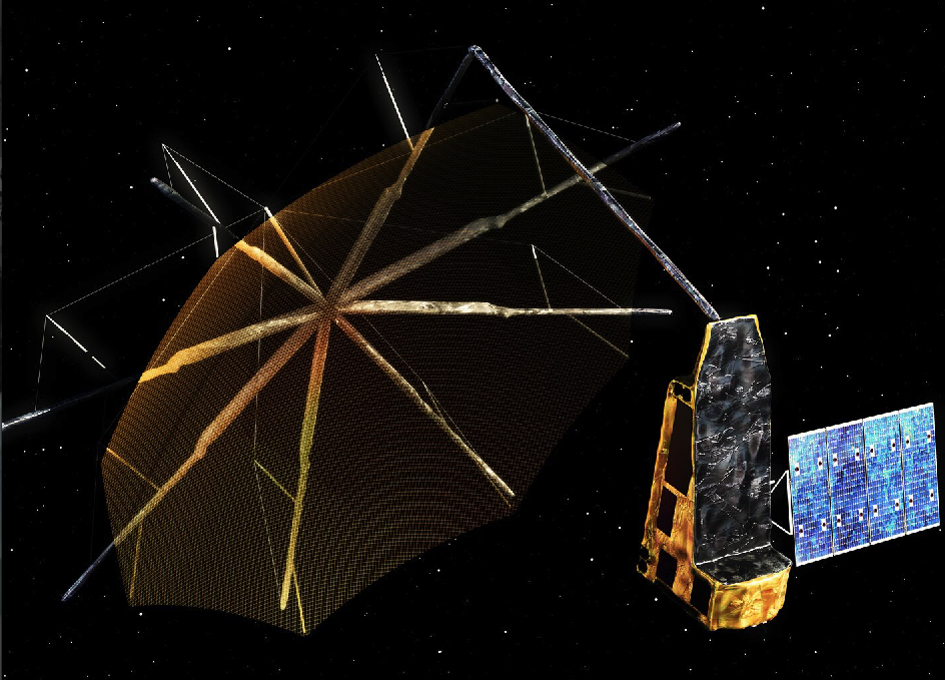
Antennas are among the most complex systems aboard a satellite – making them demanding to produce and often unpredictable to test.
Tiny variables in their building, mounting or operation may impact their working performance in a big way. So ESA teamed up with Danish company TICRA to develop a method of forecasting such discrepancies well before an antenna construction even starts.
Direct inspiration for the project came from ESA’s Biomass mission. Due to be launched next year, Biomass will deploy a massive 12-m diameter reflector to harness long-wavelength ‘P-band’ radar signals, piercing through forest canopies in order to perform a five-year census of all the trees on Earth.
“In the case of Biomass’s antenna, we face a very specific problem,” explains ESA antenna engineer Nelson Fonseca. “Because of its sheer size and the signals it employs, it is not feasible to test on Earth. Instead we predict its in-orbit performance using software modelling – but then we also need a way to quantify the reliability of our model.”
Consulting with Denmark’s TICRA, Nelson found the antenna software company was already looking into this question more generally, in response to the wider needs of the space industry. In particular -with the number of satellites in orbit forecast to grow radically, driven by commercial megaconstellations – satellite antennas are shifting from grand scale one-offs in nature towards a future of efficient, economical mass production.
“Current antenna simulation tools can only predict nominal performance,” explains Erik Jørgensen, Chief Technology Officer at TICRA. “But when we actually test the built versions of antennas we almost never observe nominal performance – there is always a degree of variation.
“Why? Because the built version of anything can never be entirely identical to the original design. There will always be slight variations introduced in the course of manufacturing, mounting and operating these extremely complex radio-frequency systems. Even a size difference of a few tenths of a millimetre, tiny power variations or structural misalignments will add uncertainty into the actual working performance.”
“One way antenna designers take account of this uncertainty is by engineering in generous performance margins,” Nelson explains. “This is in fact the approach used in Biomass, but this leads to demanding requirements with an impact on cost and schedule.”
Oscar Borries, Head of Team Mathematics and AI at TICRA, likes to illustrate this problem as follows: “Imagine you have the job of putting up chandeliers, but you’re not sure how many screws you need to fix them to the ceiling. So you use lots of screws to be on the safe side – but in space terms such margins mitigate against price and performance.
“Another approach is what is called ‘Monte Carlo simulations’ – like putting up tens of thousands of chandeliers to see how many of them will stay up without falling. Space companies and agencies run simulation after simulation of their antenna in action to see small variations in performance each time, gradually building up a statistical picture of the uncertainty range.
“Such bulk simulations are hugely costly in terms of time and computing resources however, and provide only very rough approximations – unless you commit to run millions of simulations.”
As an alternative, TICRA investigated an uncertainty quantification approach based on ongoing calculations based on a single continuous function that represent the full system performance, rather than a large number of functions that each only represent a small part of the system. The mathematics involved are hugely challenging, but the result is a much more efficient method of quantifying uncertainty.
“Our antenna software makes us a world leader in this field, but we are also a small company, and this concept represented a challenging and risky development,” adds Oscar.
“So we ended up collaborating with ESA through the Agency’s General Support Technology Programme, GSTP, to help bring promising technology to the market. One of the main advantages this brings was the continuous consultancy from the ESA side, including many of the best people in the sector.”
In practice the software will be used in various ways, beyond simulating the expected performance of antennas. Designs can be carefully optimised, not just for performance but also in terms of cost, by pinpointing the components that prove to have the least impact on performance, allowing them to be swapped out with cheaper commercial alternatives. It could also be used for yield analysis, to predict how many components in a batch will perform within specifications.
Nelson adds: “This project is really a win-win, because we get specific benefit for the Biomass mission, but the resulting software, which will be released commercially later this year, will also boost the competitiveness of the overall European space industry.”