Elon Musk Says SpaceX Completed All Corrective Actions for Next Starship Launch
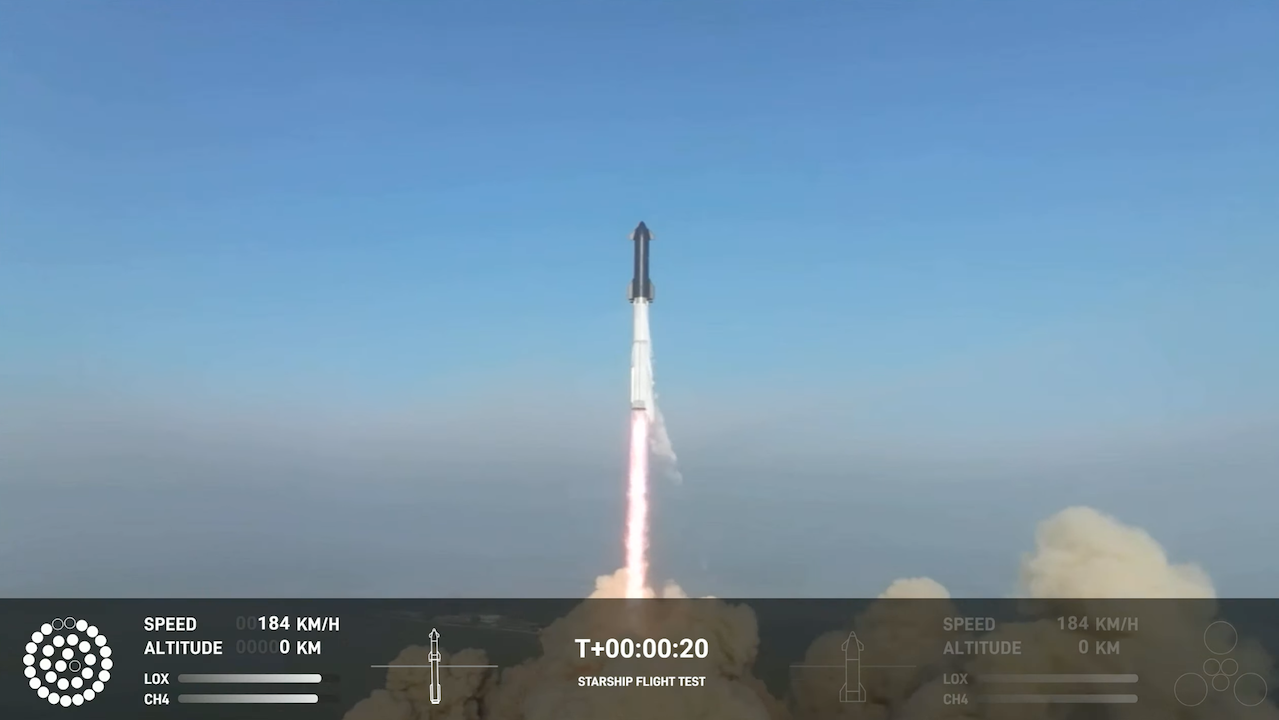
SpaceX CEO Elon Musk said on September 10 that the company has completed all of the corrective actions required by the Federal Aviation Administration (FAA) before it can conduct a second launch of its Starship/Super Heavy rocket.
Musk released images of a spreadsheet with the 63 corrective actions resulting from the failed maiden flight of Starship/Super Heavy on April 20, 2023. Six of the corrections were listed as future actions that Musk said SpaceX does not have to make before the next flight.
“Corrective actions include redesigns of vehicle hardware to prevent leaks and fires, redesign of the launch pad to increase its robustness, incorporation of additional reviews in the design process, additional analysis and testing of safety critical systems and components including the Autonomous Flight Safety System, and the application of additional change control practices,” the FAA said in a statement.
The first Starship launch in April ended, four minutes after launch, with an explosion that caused serious damage to the pad, sent debris flying into sensitive wildlife areas, and caused a fire that burned several acres of a state park (although it was reported to have not killed any of the area’s protected wildlife). The flight safety system also failed to immediately destroy the rocket when it veered off its planned trajectory.
The corrective actions came out of a SpaceX-led mishap investigation that was overseen by the FAA. The agency said it had also granted official observer status to representatives of NASA and the National Transportation Safety Board. A full list of the corrective actions, and their current status according to SpaceX, is below.
List of Corrective Actions
Starship/Super Heavy
Observation/Description | ID # | Corrective Action | Status |
---|---|---|---|
Tank sensing | C1 | Replace certain fittings with welds inside tank | Complete |
Aft end cavity environment failure | C2 | Increase fire suppression capacity by 15x | Complete |
Booster leak mitigation | C3 | Replace certain manifolds with dedicated drain per corresponding valve | Complete |
C4 | Replace certain flanges with better seals and improve joint design | Complete | |
C5 | Replace certain fittings with welds in specific location | Complete | |
C6 | Replace accessible valves of a certain type of new design | Complete | |
C7 | Replace certain flange bolts with higher strength bolts and increase torque | Complete | |
C8 | Disallow certain seal re-use, and add cameras to monitor all engines during ground operations | Complete | |
C9 | Increased scrutiny on leak checks | Complete | |
C10 | 90+ cameras added to detect leakage during operations | Complete | |
Raptor leak mitigation | C11 | Add leak capture and drain hardware for valves of a certain type | Complete |
C12 | Add leak check and screen for porosity on igniter units | Complete | |
C13 | Improved igniter seal design | Future Action | |
C14 | Weld certain alignment bolt holds shut | Complete | |
C15 | Reassess k-factor and torque for engine hot joint #1, add leak capture and route overboard | Complete | |
C16 | Reassess k-factor and torque for engine hot joint #2 | Complete | |
C17 | Add safety cable to certain fluid lines on high risk locations | Complete | |
C18 | Add one methane sensor per engine bay | Complete | |
C19 | Ground test campaign to better characterize typical engine leakage | Complete | |
C20 | Improve structural FEA/fatigue analysis for all medium to high criticality lines | Complete | |
Collateral damage from fire | C21 | Add insulation to engine lines sensitive to thermally driven loads | Complete |
C22 | Add insulation to avionic harnessing | Complete | |
C23 | Add backup wire to specific harness | Complete | |
C24 | Improve thermal protection of avionics tray | Complete | |
C25 | Change routing to flight computers | Complete | |
Booster reliability improvement | C26 | Replace sensor with more reliable units | Complete |
C27 | Cost gimbal assembly with lubricant | Complete | |
C28 | Add pump temperature sensors to certain location | Complete | |
C29 | Add pump temperature sensors to certain location | Complete | |
C30 | Replace certain bolts, and increase torque for certain flanges | Complete | |
C31 | New seal design for certain areas of booster | Complete | |
C32 | Add electric actuation system | Complete | |
C33 | Better manage engine bay pressure by increasing fire suppression capacity by 15x | Complete | |
C34 | Change certain booster valve timing | Future Action | |
Raptor reliability improvement | C35 | Add final leak checks for certain joints | Complete |
C36 | Add support bracket for certain sensor | Complete | |
C37 | Add support bracket for certain sensor | Complete | |
C38 | Add check valves to certain areas of engine | Complete | |
C39 | Improve oxygen valve design | Future Action | |
C40 | Improve oxygen valve seal design | Future Action | |
C41 | Improve design of hot manifold | Future Action | |
C42 | Change nitrogen shutdown usage | Complete | |
C43 | Change engine shutdown logic | Complete | |
C44 | Increase capability for ground leakage mitigation | Complete | |
C45 | Redesign fire suppression system | Complete | |
C46 | Change conditions around bolts | Complete | |
C47 | Changing timing of specific valve actuation | Complete | |
Avionics reliability improvement | C48 | Eliminate certain type of connector | Complete |
C49 | Redesign network architecture | Future Action | |
Risk Process | C50 | Improve risk tracking process | Complete |
Safety System | C51 | Implement improvements to safety system | Complete |
C52 | Verify flight safety system design improvements using additional type of testing article | Complete | |
C53 | Verify flight safety system design improvements via analysis | Complete | |
C54 | Perform component testing | Complete | |
C55 | Review and improve operations surrounding flight safety system | Complete | |
Change Control | C56 | Improve CAD controls | Complete |
C57 | Add engineering walkdown | Complete | |
C58 | Improve use of change management system | Complete | |
Pad Design | C59 | Redesign of launch pad deck | Complete |
C60 | Improve assumptions for new pad deck design | Complete | |
C61 | Add water cooled pad deck | Complete | |
Pad Design Process | C62 | Improve pad deck design documentation | Complete |
C63 | Improve pad design process | Complete |
Last week, the FAA announced it had closed the mishap investigation, meaning that officials were satisfied with the conclusions and actions SpaceX proposed to address the causes of the launch failure.
“The FAA conducted a final review of the mishap report, dated August 21, 2023,” the agency said in a letter to SpaceX. “The FAA has been provided with sufficient information and accepts the root causes and corrective actions described in the mishap report. Consequently, the FAA considers the mishap investigation that SpaceX was required to complete to be concluded.”
The FAA licensed SpaceX to conduct a single launch. The company must apply for a modification of the license and demonstrate compliance with all corrective actions before it can conduct a second launch.