Upcoming Test Of SLS Hardware
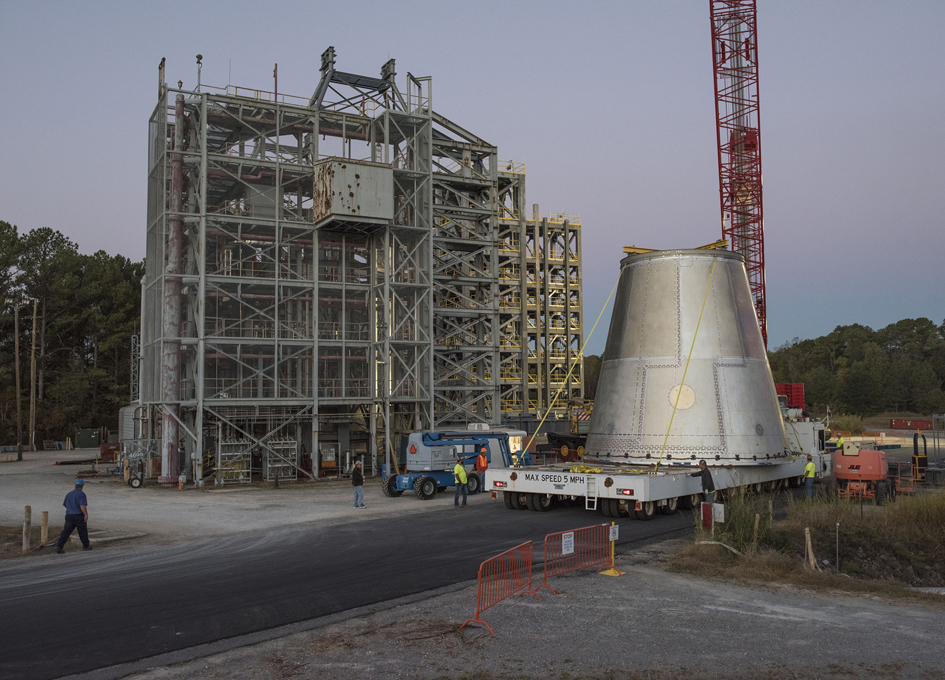
Engineers are getting ready to put the pressure on hardware for the world’s most powerful rocket, NASA’s Space Launch System, as part of a rigorous test series to ensure each structure can withstand the incredible stresses of launch.
SLS and the agency’s Orion spacecraft will travel to new destinations in deep space as NASA continues to prepare for its Journey to Mars.
“Not only is this series more cost effective by testing several qualification articles together, but it also helps us to understand how the flight-like hardware will interface together,” said Mike Roberts, mechanical team lead in the Engineering Directorate at NASA’s Marshall Space Flight Center in Huntsville, Alabama.
A 65-foot-tall test stand at Marshall is being readied for the upcoming test series, where two simulators and four qualification articles of the upper part of the SLS will be stacked and then pushed, pulled and twisted by forces similar to those experienced in flight. “We have to make sure all the hardware is structurally sound and will not compromise under the incredible amounts of force,” said Dee VanCleave, lead test engineer for the structural loads test at Marshall. “The best way to verify these major structures are ready for launch is to test them.”
The qualification articles and simulators will be stacked in order from bottom to top in a test structure with “spiders” – given that name because the hardware has 8-16 legs that span out from the center. The spider’s design helps distribute the load evenly in the test stand. The pieces are:
– Core stage simulator — a duplicate of the top of the SLS core stage that is approximately 10 feet tall and 27.5 feet in diameter. It was designed and built at Marshall.
– Launch vehicle stage adapter (LVSA) — connects the SLS core stage and the interim cryogenic propulsion stage (ICPS). The ICPS is a liquid oxygen/liquid hydrogen-based system that will give Orion the big, in-space push needed to fly beyond the moon before it returns to Earth on the first flight of SLS in 2018. The LVSA test hardware is 26.5 feet tall, with a bottom diameter of 27.5 feet and a top diameter of 16.8 feet. It was designed and built by prime contractor Teledyne Brown Engineering of Huntsville.
– Frangible joint assembly — part of the separation system on the SLS. The flight version will have small explosive devices installed that will separate the ICPS from the rest of the rocket in space. Only the structural part of the frangible joint assembly is included for this test series. It was designed and built by The Boeing Co. in Huntsville and United Launch Alliance of Decatur.
– ICPS — The qualification test article, without the engine, is around 29 feet tall and 16.8 feet in diameter. It will be filled with liquid nitrogen for testing, rather than liquid oxygen and liquid hydrogen. “Liquid nitrogen is the safest cryogenic media to use for testing,” VanCleave said. The ICPS was designed and built by Boeing and United Launch Alliance.
– Orion stage adapter – connects the Orion to the ICPS. It is 4.8 feet tall, with a 16.8-foot bottom diameter and 18-foot top diameter. It was designed and built at Marshall. The adapter technology was used for Orion’s first test flight in December 2014.
– Orion spacecraft simulator – a replica of the bottom portion of the exploration vehicle that will carry the crew to space, provide emergency abort capability, sustain the crew during the space travel, and provide safe re-entry from deep space return velocities. The simulator also was designed and built at Marshall, and is 4.5 feet tall and 18 feet in diameter.
The qualification articles are almost exact to flight hardware specifications. The core stage simulator was loaded into the test stand Sept. 21, with the LVSA following on Oct. 12. The other three qualification articles and the Orion simulator will complete the stack later this fall. Testing is scheduled to begin in early 2017.
Ready, Set, Test
Approximately 50 test cases are planned for the series. The qualification test articles will be outfitted with 28 mechanical load lines, which will use hydraulic pressure to push and pull on the test articles. The ICPS tanks also will be filled with liquid nitrogen, which will subject the hardware to pressure as high as 56 pounds per square inch — relative to atmospheric pressure. More than 170,000 pounds of liquid nitrogen will be used in the tanks for most of the load cases, and 500,000 pounds of axial hydraulic force will be applied to the entire test stack. Engineers will not test to failure for this series.
Data from the tests will be recorded through 1,900 instrumentation channels, measuring the strain on the test articles, temperature, deflection and other factors. The test data will be compared to computer models to verify the integrity of the hardware and ensure it can withstand the forces it will experience during flight. This also will be a type of practice run for assembly operations before the rocket hardware is stacked in the Vehicle Assembly Building at Kennedy Space Center in Florida ahead of launch.
The initial SLS configuration will have a minimum 70-metric-ton (77-ton) lift capability and be powered by twin solid rocket boosters and four RS-25 engines. The next planned upgrade of SLS will use a powerful exploration upper stage for more ambitious missions with a 105-metric-ton (115-ton) lift capacity. A third configuration will add a pair of advanced solid or liquid propellant boosters to provide a 130-metric-ton (143-ton) lift capacity. In each configuration, SLS will continue to use the same core stage and four RS-25 engines.